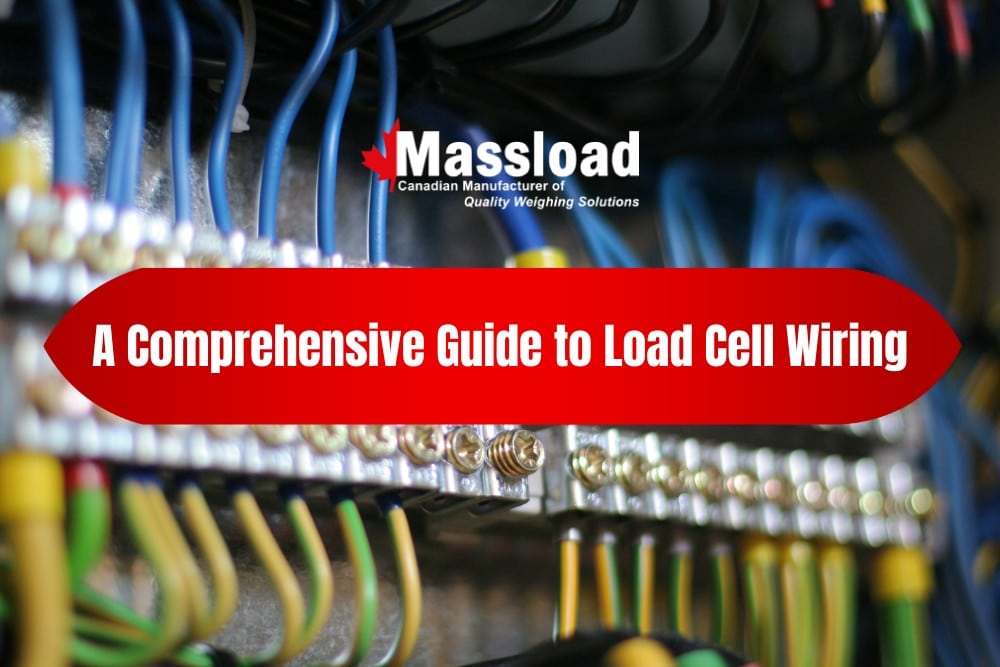
Whether you’re weighing heavy loads in truck scales, measuring flow and pressure in manufacturing or precision in industrial scales, proper load cell wiring is key to accurate and error-free measurement.
This guide covers the basics, wiring configurations, best practices and troubleshooting tips so your systems run at peak accuracy.
Basics and Components
A load cell is a force sensor that converts physical force into an electrical signal. Used across industries, from mining to OEM and agriculture load cells, to provide weight data for control and analysis.
The cable wiring in a load cell has several key wires, each with a specific function. Here are the main components:
- Excitation Wires: Power the load cell’s internal Wheatstone bridge circuit.
- Signal Wires: Carry the output signal from the load cell, the measured force or weight.
- Sense Wires (optional): Monitor the voltage at the load cell and adjust for voltage drops over long cables.
- Shielding: Protects signal wires from electromagnetic interference (EMI) to maintain signal quality.
Common color codes include:
- Excitation: Red and black
- Signal: Green and white
- Sense: Blue and yellow (if applicable)
- Shield: Bare wire or metal sheath surrounding the others
Knowing what each component does will improve the accuracy and reliability of the system.
Configurations
In the world of load cells, there are 4-wire and 6-wire configurations, each for different installation scenarios.
- 4-Wire Load Cells: Standard for short distances, these have excitation and signal wires only. They work well in controlled environments where cable length and temperature variations are minimal.
- Advantage: Easier to install, economical, for shorter distances.
- 6-Wire Load Cells: With additional sense wires 6-wire configurations are for longer cables, to compensate for voltage drops over longer distances. They are for environments where temperature variations will affect voltage stability.
- Advantage: More stable readings over long distances and in temperature variable environments, better measurement precision.
Understanding 4-Wire Load Cells
The 4 wires of a standard load cell are:
- Excitation+ (EXC+ or E+): Positive voltage to the load cell.
- Excitation- (EXC- or E-): Negative voltage or ground, completes the power circuit.
- Signal+ (SIG+ or S+): Carries the positive side of the output signal, the force or weight measurement.
- Signal- (SIG- or S-): Carries the negative side of the output signal, balances the signal circuit.
In a 4-wire load cell, these wires handle both excitation (power) and signal (measurement), with each having a specific role in the reading.
Connecting 6-Wire Load Cells
Connecting a 6-wire load cell involves adding two more wires called Sense+ and Sense-, along with the standard 4 wires.
These extra sense wires will measure excitation voltage directly at the load cell, compensating for any losses due to cable length or temperature variations.
Here’s how to connect a 6-wire load cell with a 6-wire load cell indicator:
1. Identify the 6 Wires:
- Excitation+ (E+): Power supply positive
- Excitation- (E-): Power supply ground or negative
- Signal+ (S+): Positive output signal
- Signal- (S-): Negative output signal
- Sense+ (Sen+ or Sense+): Voltage feedback positive
- Sense- (Sen- or Sense-): Voltage feedback negative
2. Connect the Excitation Wires:
- Excitation+ (E+) to the positive terminal of your power source or indicator.
- Excitation- (E-) to the ground or negative terminal of your power source or indicator.
3. Connect the Signal Wires:
- Signal+ (S+) to the positive input terminal of your indicator or data acquisition system.
- Signal- (S-) to the negative input terminal of your indicator.
4. Connect the Sense Wires:
- Sense+ (Sense+) to the Sense+ (Sense+) terminal of the indicator. This will allow the indicator to monitor the exact excitation voltage the load cell is receiving.
- Sense- (Sense-) to the Sense- (Sense-) terminal of the indicator.
5. Check Connections:
- Double-check that all connections are secure and match the load cell and indicator wiring diagram. Matching the wires is critical for accurate readings.
6. Ground the Shield (if applicable):
- If your cable has a shield, ground it on one end (usually at the indicator) to reduce electromagnetic interference.
With these connections, your 6-wire load cell will compensate for any voltage drops over long cables and give you stable and precise readings.
Component Breakdown
To maintain high accuracy, each component in load cell wiring has a specific role:
- Excitation Wires: Consistent excitation voltage is key to the load cell’s operation. Excitation wires provide this and usually require 5V to 10V. Any variation here will affect the data.
- Signal Wires: These carry the output signal (usually in millivolts per volt, e.g. 2.0mV/V or 3.0mV/V). Signal clarity is critical as signal integrity affects data accuracy.
- Sense Wires: By monitoring the actual excitation voltage at the load cell, sense wires will compensate for losses due to cable length. Especially useful for cables over 20 meters long, they will keep the load cell – indicator calibrated accurately.
- Shielding: Shielding prevents EMI from affecting the data signal. Ground the shield at one end, usually at the indicator or controller, to divert the interference and stabilize the signal.
Installation Guidelines
Installation is critical to a working load cell system. Here’s what to do:
- Strip wires to clean metal-to-metal contact with terminals
- Don’t have excess wire exposed to prevent grounding or interference
- Connect each wire to its terminal securely to prevent signal loss or data corruption
- Follow the manufacturer’s color codes and wiring diagrams to avoid incorrect connections
- Ground the shield at the indicator end to deflect EMI
- For longer cables, ground as needed to maintain signal clarity
How Do I Troubleshoot Common Issues?
Even with good wiring, issues will sometimes occur. Here are some common problems and how to fix them:
- Voltage Drops: Long cables or high temperatures can cause excitation voltage drops. Add sense wires or upgrade to a thicker cable to mitigate these.
- Signal Interference: EMI from nearby machinery or electrical wiring can affect the load cell signal. Check the shielding and grounding and reroute the cables if the interference persists.
- Loose Connections: Over time connections can come loose and cause data loss or erratic readings. Check the terminals and secure any loose wires to stabilize the signal.
By following these troubleshooting steps you will save time and get consistent results from your load cell system.
Tips for Accurate and Reliable Measurements
Proper load cell wiring is key to getting accurate readings. The first step is to check the wiring against the manufacturer’s diagram and make sure the color codes match and connections are secure to prevent signal loss.
Incorrect wiring can cause:
- Wild readings
- Reduced accuracy
- Damage to the load cell itself
Regular wiring checks are a must. We recommend checking load cell wiring every 6 months and more often in harsh environments or high-vibration areas.
Proper load cell wiring is critical for force measurement in:
- Industrial scales
- Truck weighing
- OEM solutions
Follow these guidelines to get reliable and accurate data. For more information, check your load cell manual or call a technician.
Want to Learn More About Load Cells?
Check out our other articles on load cell configurations, troubleshooting techniques, and advanced calibration methods.
Explore the full range of our blog for insights tailored to enhance your weighing and measurement accuracy!