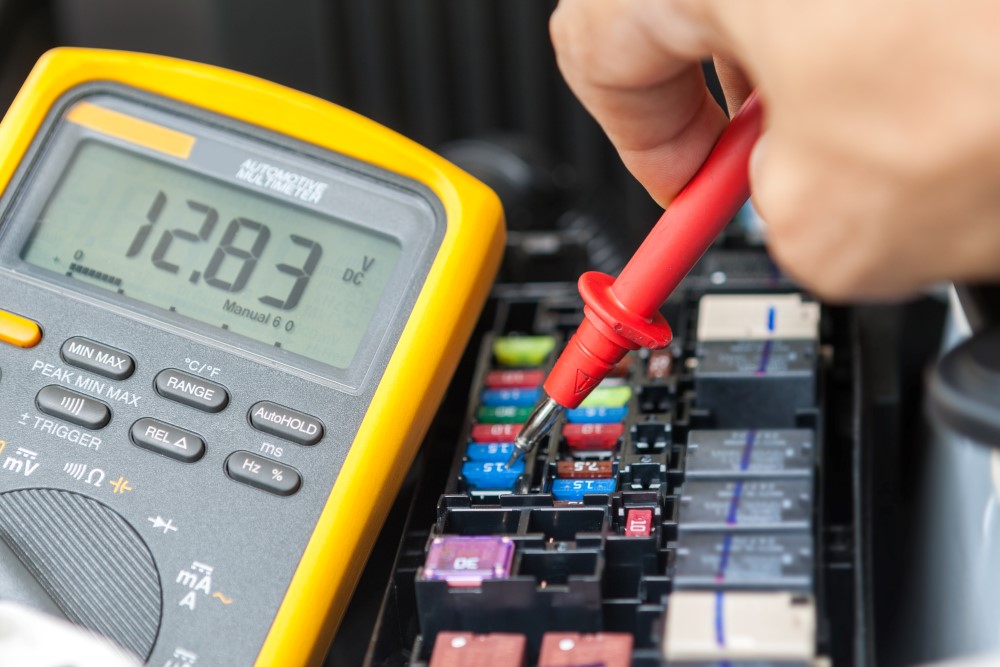
A load cell controller can manage multiple load cells at the same time, but it depends on the controller and how the load cells are connected.
Some controllers can only handle one load cell while others can handle several. When multiple load cells are used together they usually need to be connected in a way that the controller can read all of them correctly.
This can be done by wiring them in parallel or using a summing junction box which helps to combine the signals from all the load cells into one. The controller then processes the signals and gives a final weight reading.
Let’s get into more detail about how to integrate multiple load cells, the challenges involved and best practices for optimal performance.
Understanding Load Cell Signal Processing Components
Each of these devices plays a different role in processing the signal from a load cell. Here’s how they differ:
1. Load Cell Signal Amplifier
- Purpose: Boosts the small electrical signal from the load cell to a higher voltage or current level.
- Why It’s Needed: Load cells output very weak signals (millivolts) which are too small for many devices to read.
- Output: Still an analog signal but at a higher voltage (e.g. 0-10V) or current (e.g. 4-20mA) for easier transmission and processing.
- Use Case: When the signal needs to travel a long distance or be fed into another system like a PLC.
2. Load Cell Signal Conditioner
- Purpose: Converts, filters and stabilizes the signal from the load cell.
- Why It’s Needed: Load cell signals can be affected by noise, temperature changes or long cable runs, so conditioning improves accuracy.
- Includes:
- Amplification (like a signal amplifier)
- Filtering (removes noise and interference)
- Signal conversion (e.g. from millivolts to 0-10V, 4-20mA or digital formats like RS485)
- Use Case: When the signal needs to be cleaned and formatted for specific control systems.
3. Load Cell Controller
- Purpose: The “brain” of the system that reads, processes and displays weight data.* Why It’s Needed: It not only amplifies and conditions the signal but also calculates and interprets weight in real-time.
- Includes:
- Everything a signal amplifier and conditioner do
- A digital display or communication output
- Calibration and scaling functions
- Optional features like alarms, data logging or automation integration
- Use Case: When you need a standalone system to manage weight measurement, often found in weighing scales, batching systems or industrial automation.
How to Connect Multiple Load Cells Together?
When multiple load cells are connected to one controller, their signals need to be combined in a way that makes sense for accurate weight measurement. There are two common ways to do this:
Parallel Wiring
- Each load cell is connected to the same input points on the controller.
- The controller averages the signals or sums them up, depending on the setup.
- This method is used when all the load cells need to contribute equally to the weight measurement, like in a platform scale.
Using a Summing Junction Box
- Instead of connecting all load cells directly to the controller, they first go to a small device called a summing junction box.
- This box takes all the individual signals and combines them into a single output signal.
- The controller then reads this final signal as if it came from just one big load cell.
- This method is useful when load cells might have slightly different readings due to positioning or variations in manufacturing.
The load cell controller then interprets this combined signal and converts it into a weight reading that makes sense. It may also have a feature called individual load cell calibration which helps to adjust for any small differences between the load cells to keep the readings accurate.
Advantages of Centralized Signal Conditioning
Centralized signal conditioning for load cells offers several benefits that improve system efficiency, accuracy and reliability:
Simplified Wiring & Integration
- Reduces the need for multiple signal conditioners, consolidates all load cell signals into a single unit.
- Minimizes cabling complexity, makes installation and troubleshooting easier.
Better Accuracy & Signal Consistency
- Centralized conditioner balances and processes all load cell signals together, preventing inconsistencies.
Ensures uniform signal amplification and noise reduction across all load cells.
Improved Noise Filtering
- Centralized units include advanced filtering and shielding to minimize electrical noise and interference.
- Ideal for industrial environments where long cables can introduce signal degradation.
Simpler Calibration & Load Balancing
- Single-point calibration adjusts each load cell’s signal for uniform weight distribution.
- No need to calibrate multiple load cells individually.
More Reliable
- Fewer components = fewer failure points and less maintenance.
- Consistent power to all load cells for long-term performance.
Standardized Output for Easy Integration
- Converts multiple load cell signals into one standard output (e.g., 0-10V, 4-20mA, RS485, Modbus).
- Connect to PLCs, controllers or display systems.
Cost Savings for Large Systems
- Fewer signal conditioners means lower equipment and installation costs.
- Easier system upgrades when adding more load cells.
Challenges and Considerations
While centralized signal conditioning has many benefits, there are issues to be aware of.
Load cell compatibility is important to consider when involving multiple load cells. The load cells must have the same specs (capacity, sensitivity and output resistance) for accurate measurements.
- Signal loss and interference can occur with long cables, so proper shielding and grounding is necessary.
- Calibration and load balancing can also often be complex. If one load cell drifts or fails the whole system will be affected and will require regular maintenance.
- There’s also a single point of failure risk. If the signal conditioner fails, the whole weighing system will be impacted, so you need to have a redundancy plan.
- System integration is another factor. While centralized conditioners standardize the output (0-10V, 4-20mA, RS485), they must be compatible with existing PLCs, controllers or software, sometimes requiring additional configuration.
- Cost is also a concern for smaller applications. High-end conditioners, junction boxes, and proper cabling can be more expensive than multiple small conditioners.
Best Practices for Multi-Load Cell Systems
Implementing a multi-load cell system requires careful planning for accuracy, reliability and long-term performance. Here are the best practices:
1. Use Load Cells with Same Specifications
To get consistent and accurate readings all load cells in the system must have the same capacity, sensitivity (mV/V) and resistance. Mismatched load cells will cause uneven weight distribution and incorrect measurements.
2. Wiring and Summing
For multiple load cells, proper wiring is key. A summing junction box collects signals from all load cells and outputs a single balanced signal to the signal conditioner. Load cells should be wired in parallel, with excitation and signal lines connected correctly.
3. Stable Excitation Voltage
A stable and consistent excitation voltage (5V or 10V) is essential to prevent signal variations. The signal conditioner should supply enough power to all load cells without dropping voltage.
4. Minimize Electromagnetic Interference
To reduce interference:
- Use shielded cables and keep them short.
- Avoid running load cell cables near power lines, motors or other noise sources.
- Ground the system to prevent floating signals or interference.
5. Calibrate and Balance
Once all load cells are connected, perform zero and span calibration:
- Zero Calibration: Zero weight reading when unloaded.
- Span Calibration: Use a known reference weight to adjust load cell outputs and balance the system.
If using a junction box, some have trim adjustments to fine tune individual load cell outputs and ensure even weight distribution.
6. Choose the Right Signal Conditioner
The signal conditioner should have multi-load cell inputs and the required output (0-10V, 4-20mA, RS485). It should also have filtering to remove noise and stabilize the reading.
7. Maintenance and Monitoring
- Check connections and cables for wear or damage.
- Watch for drifting readings, which may indicate a faulty load cell or calibration issue.
- If a load cell fails, replace it with one of the same specs to maintain accuracy.
8. Consider Environmental Factors
If used in harsh environments (moisture, temperature fluctuations, vibration), ensure:
- Load cells have the right IP rating.
- Signal cables are sealed against dust and moisture.
- Signal conditioner compensates for temperature variations.
By following these guidelines, a multi-load cell system will give you precise and reliable weight measurements for your industrial application.
Find the Right Load Cell Setup with Massload
Need expert guidance on selecting the best load cells, signal conditioners, or wiring setup for your application? Contact us today to find the perfect solution for your weighing system!