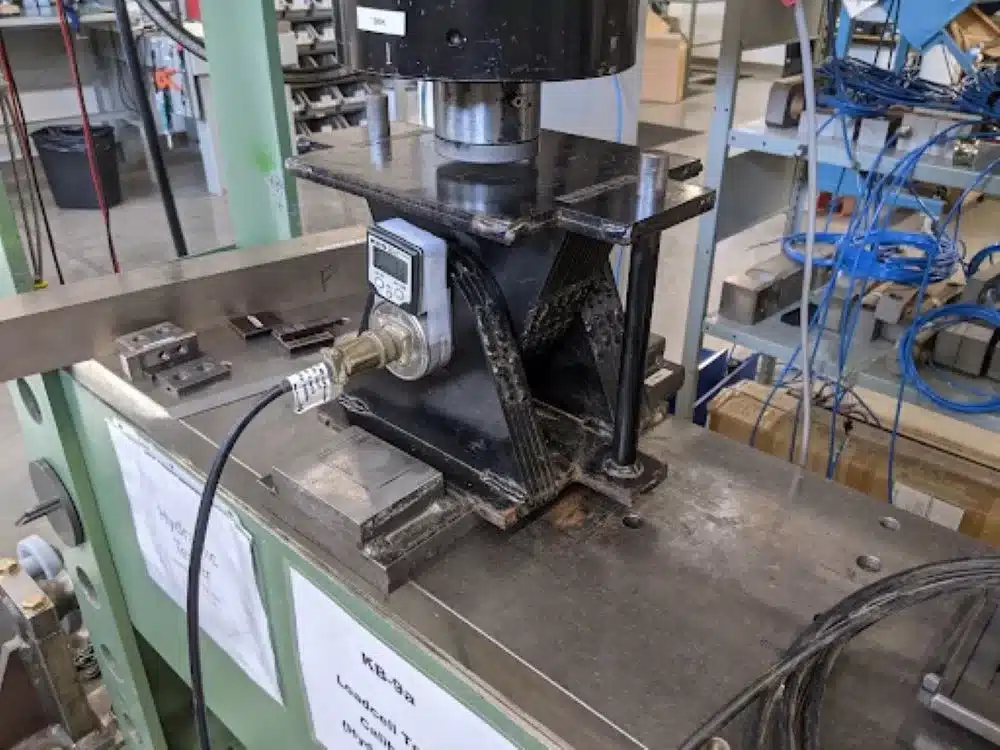
Load cells are the silent heroes of the weighing world. When functioning normally, they ensure accurate measurements and utmost performance.
However, like any sophisticated technology, they’re not immune to problems. Recognizing the signs of malfunction and understanding when to call in the experts can save time and resources as well as ensure operational efficiency.
Continue reading to learn how to recognize the signs that your load cell may be malfunctioning and when to seek professional repair services.
Understanding Load Cells
Load cells are a key part of industrial weighing systems. They convert a physical force (usually weight or pressure) into an electrical signal, which is then measured to give the weight of an object. This is done by a strain gauge which deforms under pressure and the deformation causes a change in electrical resistance. This change is measured and translated into a weight reading.
There are many types of load cells used in industry each with its own characteristics and applications. The most common are:
- Compression Load Cells: Used to measure compressive forces. Found in weighbridges and platform scales.
- Tension Load Cells: Used to measure tensile forces. Used in systems that monitor force during lifting or pulling.
- Shear Beam Load Cells: Reliable and versatile. Used where a compact high performance load cell is required.
- S-Type Load Cells: Used in smaller capacity applications. Used in tank weighing and precise applications.
Understanding Load Cell Malfunctions
At the heart of every industrial scale, load cells convert force into electrical signals, allowing us to measure weight with remarkable accuracy. Common signs of trouble include:
- Zero drift: The scale doesn’t return to zero when unloaded.
- Calibration issues: Difficulty in calibrating the scale to ensure accurate readings.
- Inconsistent readings: Fluctuating weight measurements for no apparent reason.
- Total system failure: The scale stops providing readings altogether.
If you notice one or more of these symptoms on your equipment, It’s time to ask for technical help. Otherwise, if ignored, can lead to inaccurate data and potential operational disruptions.
Common Causes of Failures
Several factors can compromise load cell performance. Here are six of the most common ones:
1. Mechanical Damage
Physical impacts or mishandling can lead to mechanical damage in load cells. This type of damage is not just about the external dents or scratches that are visible to the eye; it’s the internal components that often suffer the most. Strain gauges, integral to a load cell’s function, can become misaligned or damaged, leading to inaccurate readings or complete failure.
2. Overloading
Load cells are designed to measure up to a certain weight, and exceeding this limit can have dire consequences.
Overloading a load cell can permanently deform its structure, affecting its ability to return to zero or provide accurate measurements.
This kind of damage is often irreversible, necessitating a replacement to maintain the scale’s precision.
3. Moisture and Chemical Ingress
The operational environment can significantly affect the integrity of a load cell. Exposure to moisture and chemicals can lead to corrosion of the load cell’s components, especially the electrical connections and strain gauges. Over time, this corrosion can degrade the load cell’s performance, leading to faulty readings or total failure.
4. Electrical Damage
Electrical surges, often caused by lightning strikes or power fluctuations, can wreak havoc on the delicate electronics within a load cell. Such surges can fry circuits, leading to immediate failure or erratic performance.
5. Temperature Changes and Creep
Temperature fluctuations can impact the accuracy of load cells in several ways. Materials expand and contract with temperature changes, which can affect the mechanical structure of the load cell and its ability to measure accurately.
Additionally, sustained pressure over time, known as creep, can cause a slow drift in the load cell’s zero point, especially at high temperatures, complicating accurate measurements over long periods.
6. Vibration and Noise
External vibrations and noise can also disrupt the accuracy of load cells. In industrial environments, machinery and heavy vehicles can generate significant vibrations, which may cause load cells to produce fluctuating readings.
Similarly, electromagnetic noise from nearby equipment can interfere with the electrical signals in a load cell, leading to inaccurate or inconsistent weight measurements.
Diagnosing Load Cell Issues
Before you call for help, some simple checks can diagnose or even resolve basic issues:
- Inspect for visible damage or loose connections.
- Verify that the load cell is not overloaded or subjected to environmental hazards.
- Perform basic functional tests to see if the issue might be with peripheral equipment or cables.
If these steps don’t clear up the problem, it’s time to seek professional advice.
Symptoms of Load Cell Failure
Several symptoms can indicate a malfunctioning load cell. If you observe any of the following signs, investigate further:
- Inaccurate Readings: One of the most obvious signs of a load cell failure is a calibration drift or unstable outputs. If the weight readings are all over the place or the scale won’t zero out, then there’s an issue with the load cell and you need to take a closer look.
- Physical Damage: Load cells get beat up in the field. Cracks, dents or visible deformation on the load cell housing or strain gauges means physical damage. This can be caused by overloading, misuse, or external impact.
- Response Time: Slower response times are a subtle but telling sign. If there’s a delay between applying weight and the scale showing the measurement, it could be internal damage, electrical problems or strain gauge issues. This affects both accuracy and productivity.
When to Contact a Professional
Seeking Professional Repair Services is Advisable When:
- Basic troubleshooting doesn’t resolve the issue.
- The load cell shows signs of physical damage.
- Calibration and operational tests fail repeatedly.
Experts in load cell repair can provide diagnostic services and precision repairs or advise if a replacement is more cost-effective.
Maintaining Your Load Cells
Preventive maintenance is key to avoiding unexpected downtimes. Here are some tips:
- Regular Calibration: Ensures ongoing accuracy and helps identify issues early.
- Environmental Protection: Use covers and shelters to protect scales from harsh conditions.
- Load Management: Avoid exceeding the scale’s capacity and ensure loads are evenly distributed.
Choosing the Right Repair Service
When selecting a repair service, it’s important to make sure that you choose a provider that is reliable and has the technical expertise to solve your problem. Before making that choice, remember to consider:
- Experience and Reputation: Look for firms with a proven track record in your industry.
- Certification: Ensure the service provider has the appropriate credentials.
- Range of Services: Prefer providers that offer a comprehensive suite of repair and maintenance options.
Load cells are reliable electronic devices, and when treated properly, they deliver accuracy, performance, and safer operations.
By understanding the most common issues that load cells can encounter, you will be equipped to recognize and act promptly at the slightest sign of trouble.
This approach ensures compliance with industry standards, helps prevent downtime, saves money, and keeps operations safe and on schedule.
At the end of the day, load cells are not just another component of a scale; they are the critical element that makes all the difference.
Massload’s Load Cell Repair Service
As a trusted Canadian Load Cell Manufacturer, we stand behind the quality of our products with warranties ranging from 1 to 5 years. We know how critical load cells are to the accuracy and efficiency of your operations, which is why we’re committed to providing reliable support to keep your systems running smoothly.
Our dedicated support team is always ready to go the extra mile to address the unique challenges our clients encounter in their daily operations. If you need assistance, don’t hesitate to contact us today!
We understand that downtime can be costly, which is why we prioritize fast response times and effective solutions to minimize disruption.
Want to hear from our satisfied clients? Check out their feedback on our exceptional support services here:
For more information, including our full Terms & Conditions and Warranties, click here.