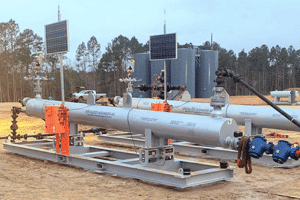
If you’re integrating load cells into OEM equipment, you’ve probably discovered the frustrating reality that most manufacturers pitch “standard” solutions that never quite fit your design parameters. Or maybe you’ve been quoted a custom solution that made your procurement department stop in their tracks.
The truth? Both approaches have their place, and the right choice isn’t always obvious. But making the wrong selection can lead to compromised measurement accuracy, premature field failures, and the kind of warranty claims that keep engineering managers awake at night.
For OEMs operating in the highly regulated U.S. industrial landscape, these decisions have serious implications. Your measurement system isn’t some bolt-on accessory—it’s a critical component that directly impacts your equipment’s performance, reliability, and regulatory compliance. Get it wrong, and you’re looking at redesigns, field retrofits, and the kind of conversations with management that nobody enjoys.
What Are Load Cells, and Why Are They Essential for OEMs?
At the most basic level, load cells convert mechanical force into electrical signals through strain gauge deformation. However, that textbook definition completely misses the practical reality of OEM applications. In your equipment, load cells are the critical sensors that enable:
- Precise force control in automated systems
- Overload protection for mechanical components
- Process validation for quality assurance
- Regulatory compliance documentation
- Feedback for closed-loop control systems
Why Load Cells Are Important in OEM Systems
For OEMs developing industrial equipment in today’s market, load cells aren’t just about measuring weight – they’re fundamental control system components that enable:
- Force-based control loops: Essential when you need to maintain specific pressures, tensions, or compression forces
- Critical safety functions: When your equipment needs to shut down before mechanical failure occurs
- Process verification: Documented evidence that operations stayed within specified parameters
- Quality control: Confirmation that assembly forces or material properties meet specifications
- Compliance documentation: Hard data showing you’ve stayed within regulatory limits
The harsh reality is that many OEMs treat load cell selection as an afterthought and then wonder why their equipment performs inconsistently in the field or fails prematurely under real-world conditions.
Industries That Rely on Load Cells
Different OEM sectors face wildly different measurement challenges:
Oil & Gas
Equipment in this sector operates in genuinely brutal conditions:
- Explosive atmospheres requiring intrinsic safety certification
- Exposure to H₂S, drilling mud, and caustic cleaning agents
- Temperature swings from -40°F to 180°F (sometimes in the same day)
- Constant vibration that destroys standard electronics
- Pressure washing that finds every weakness in your sealing system
Standard catalog load cells typically fail rapidly in these environments unless they’re specifically engineered for these conditions.
Mining
If you think oil & gas is tough, mining environments take it to another level:
- Continuous exposure to abrasive dust that finds its way into everything
- Corrosive groundwater that makes stainless steel look like it’s made of sugar
- Shock loading that regularly exceeds 500% of rated capacity
- Temperatures ranging from freezing in deep shafts to 120°F in surface operations
- Constant vibration that works hardened bolts loose within weeks
Load cells in these applications need to be mechanical tanks first, precision instruments second.
Agriculture
Modern agricultural equipment presents unique challenges:
- Continuous outdoor exposure to UV, rain, and temperature extremes
- Chemicals that attack standard sealing materials
- Rough terrain creating constant mechanical shock
- Seasonal use patterns with long storage periods
- Price sensitivity that makes gold-plated solutions impractical
The engineering challenge becomes finding the sweet spot between durability and cost-effectiveness.
Construction and Material Handling
Construction equipment subjects load cells to:
- Constant vibration and mechanical shock
- Concrete dust that’s as abrasive as it is alkaline
- Operators who view “gentle handling” as a theoretical concept
- Wide temperature ranges at job sites
- Electrical systems that would make power quality engineers weep
These conditions quickly separate genuinely robust designs from those that just look good in a catalog.
Transportation
Transportation OEMs need load cells that can handle:
- Continuous road vibration and occasional impacts
- All-weather operation from Arizona summers to Alaska winters
- Exposure to road salt, diesel, and whatever else splashes up from the highway
- Limited installation space in already crowded designs
- Power systems that fluctuate with engine RPM
Standard load cells designed for stable environments typically fail quickly in these mobile applications.
What Are Custom Load Cells, and How Are They Different from Standard Load Cells?
Here’s what manufacturers won’t tell you: many “custom” load cells are just standard designs with minor modifications, not purpose-engineered solutions for your specific application.
What Makes Load Cells “Custom”?
True custom load cells are fundamentally different from standard products:
- Application-Specific Design: Engineered from first principles for your specific load paths and measurement objectives
- Form Factor Optimization: Physical dimensions tailored to fit your available space, not the other way around
- Environmental Engineering: Sealing, materials, and protection designed for your specific exposure conditions
- Performance Tuning: Capacity, response characteristics, and temperature compensation optimized for your actual operating range
- Interface Integration: Output signals and connections designed to plug directly into your control system
The main difference is a holistic engineering approach, not just tweaking dimensions or changing a connector.
Advantages of Custom Load Cells
When properly engineered, custom load cells offer significant advantages:
- Optimized Signal Quality: Better S/N ratio because the cell is designed specifically for your loading conditions
- Improved Long-Term Stability: Less drift and recalibration because the design accounts for your specific cyclic loading
- Enhanced Environmental Resilience: Better reliability because protection systems address your actual exposure conditions
- Simplified Integration: Lower installation costs because the cell fits your equipment, not vice versa
- Improved Measurement Accuracy: Better precision because the capacity and response are matched exactly to your application
For demanding applications, these advantages translate directly to better field performance and lower lifetime costs.
What Are Considered Standard Load Cells?
Standard load cells are catalog products with:
- Fixed Form Factors: Predetermined dimensions that may require adaptation to fit your equipment
- Standardized Capacities: Typical increments like 5K, 10K, 25K, 50K that may not optimize your resolution
- Generic Environmental Protection: Usually IP67/IP68, which may not address specific chemical exposures
- Limited Output Options: Typically mV/V, 0-5V, 0-10V, or 4-20mA without customization for your system
- Volume Production Economics: Lower unit costs through standardized manufacturing
For applications with common requirements and benign environments, these standardized solutions offer cost advantages without significant performance compromises.
When to Choose Custom Load Cells Over Standard Load Cells?
This is where honest engineering analysis beats marketing every time.
OEM Applications Requiring Specialized Load Cells
Custom load cells become technically necessary when your application presents:
- Non-Standard Force Vectors: Loads applied in directions or combinations that standard cells weren’t designed to handle
- Extreme Environmental Conditions: Exposure that exceeds the protection capabilities of standard designs
- Severe Space Constraints: Installation locations that can’t accommodate standard dimensions
- Unique Performance Requirements: Accuracy, response time, or stability needs beyond standard specifications
- Special Electrical Interfaces: Output or communication requirements not available in standard products
- Critical Safety Applications: Uses where failure modes must be specifically engineered and documented
In these situations, attempting to use standard products typically leads to compromised performance or premature failures that ultimately cost far more than the initial savings.
When are Standard Load Cells Sufficient?
Standard load cells make perfect sense when:
- Conventional Loading: Forces applied in ways that match standard load cell design assumptions
- Normal Industrial Environments: Operating conditions within typical temperature, moisture, and contamination ranges
- Adequate Installation Space: Sufficient room to accommodate standard dimensions without compromises
- Basic Measurement Needs: Accuracy and stability requirements within standard catalog specifications
- Common Signal Requirements: Interface needs that match standard output options
- Non-Critical Applications: Uses where occasional recalibration or maintenance doesn’t significantly impact operations
In these scenarios, standard products offer a cost-effective solution without significant performance compromises.
What to Consider When Selecting a Load Cell for Your OEM Application
Here’s where the rubber meets the road in engineering terms.
Load Capacity and Measurement Range
Don’t just look at maximum load – consider the entire operational profile:
- Normal Operating Range: Where you need optimal resolution and accuracy (typically 20-80% of rated capacity)
- Occasional Overloads: Peak forces during abnormal operations
- Safety Margins: Additional capacity to prevent damage (typically 150% for safe overload, meaning no damage to the load cell)
- Resolution Requirements: The smallest force change you need to reliably detect
- Dynamic Loading: Additional effective forces created during acceleration/deceleration
Most applications benefit from selecting a capacity approximately 150-200% of maximum normal operating load—this provides adequate overload protection while maintaining good resolution in the primary operating range.
Environmental Conditions
This is where most load cell failures originate:
- Temperature Range: Both extremes and rate of change
- Moisture Exposure: Condensation, splash, washdown, or immersion
- Chemical Contact: Process fluids, cleaning agents, and atmospheric contaminants
- Particulate Exposure: Dust, grit, and abrasive materials
- Vibration Profile: Frequency and amplitude of operational vibration
Be brutally honest here – load cells will see your equipment’s worst days, not just ideal lab conditions.
Material Compatibility and Durability
Material selection directly impacts both performance and longevity:
- Corrosion Resistance: Specific chemical compatibility, not just generic “stainless steel”
- Fatigue Resistance: Ability to withstand millions of load cycles without sensitivity drift
- Temperature Stability: Maintaining calibration across your actual operating range
- Wear Resistance: Durability of contact surfaces in high-cycle applications
- Galvanic Compatibility: Prevention of corrosion between dissimilar metals
Standard 17-4PH stainless works for many applications, but specialized alloys or treatments may be necessary for challenging environments.
Industry-Specific Standards (FDA, ASTM, OSHA, etc.)
Regulatory requirements often drive material and design choices:
- FDA Compliance: For food and pharmaceutical equipment, requiring specific materials and finishes
- Hazardous Area Certification: For explosive environments, requiring specific design approaches
- ASTM Compliance: For testing applications, requiring specific performance documentation
- OSHA Requirements: For safety-related applications, requiring specific reliability characteristics
These requirements frequently necessitate custom designs rather than standard catalog products.
Is It Worth Investing in Custom Load Cells for OEM Applications?
This is ultimately an engineering economics question.
Pricing Overview for Custom Load Cells
Let’s be honest about the cost structure:
- Non-Recurring Engineering: One-time design and tooling costs (typically $2K-5K)
- Unit Pricing: Generally 30-100% higher than equivalent standard products
- Minimum Order Quantities: Usually required to amortize setup costs
- Development Timeline: Typically 8-12 weeks versus immediate availability for standard products
These factors must be weighed against the long-term benefits and total cost of equipment ownership.
Long-Term Savings vs. Initial Investment
The full economic picture often favors custom solutions when considering:
- Integration Costs: Simplified installation without adaptation components
- Warranty Claims: Reduced field failures from optimized environmental protection
- Maintenance Requirements: Less frequent calibration and longer service life
- Downtime Reduction: Improved reliability in critical applications
- Performance Benefits: Enhanced accuracy, stability, and control capability
For many OEM applications, these long-term benefits to the owner substantially outweigh the initial purchase cost premium, particularly for higher-volume production or critical applications.\
Accuracy & Efficiency for Project Needs
Your accuracy requirements significantly impact this decision:
- Critical Measurement: Applications where force measurement directly affects product quality
- Safety Systems: Where measurement accuracy has safety implications
- Compliance Documentation: Where force recording falls under regulatory oversight
- Process Optimization: Where precise force control improves efficiency or quality
For these applications, the enhanced performance of custom solutions typically justifies their cost premium through improved operational results.
How To Choose the Right Load Cell with Help From Massload
Selecting between custom and standard load cells involves technical trade-offs that significantly impact equipment performance and reliability. Massload Technologies functions as an engineering partner rather than a mere component supplier, analyzing your specific application parameters including:
- Actual load paths and force vectors specific to your mechanical design
- Environmental exposure conditions unique to your operating environment
- Dynamic loading characteristics including vibration and fatigue considerations
- Signal integrity requirements within your electrical environment
- Mechanical integration constraints and space limitations
- This analysis helps determine whether standard or custom solutions are optimal for your specific OEM application.
Massload’s Expertise in Custom Load Cells for OEM Applications
When standard solutions fall short, Massload offers specialized expertise in custom development:
- Application-Specific Design: Load cells optimized for exact requirements rather than adapted standard designs
- Advanced Analysis: FEA modeling to optimize strain gauge placement and verify structural integrity
- Material Expertise: Selection of optimal alloys and surface treatments for specific environments
- Prototype Testing: Validation under simulated conditions before production
- Quality Manufacturing: Repeatable processes ensuring consistency in volume production
These capabilities are particularly valuable for challenging applications like agricultural machinery in corrosive environments or construction equipment subject to extreme shock loading.
Tailored Solutions for U.S. Markets
Massload’s experience across North American markets provides insight into U.S.-specific requirements:
- Regulatory Compliance: Understanding of FDA requirements, OSHA standards, and other regulations
- Industry Standards: Knowledge of ASTM test methods and sector-specific certification requirements
- Regional Considerations: Designs accounting for environmental challenges across different U.S. regions
- Market Expectations: Familiarity with performance and reliability standards in competitive U.S. markets
Comprehensive Support Services
Massload provides support throughout the entire development and deployment cycle:
- Initial consultation and technical specification development
- Design review and prototype testing
- Integration guidance and field performance analysis
- Long-term technical support throughout your product lifecycle
This comprehensive approach transforms load cell selection from a simple component decision to a strategic engineering advantage for OEMs developing precision-dependent equipment.
Making the Right Decision for Your OEM Load Cell Needs
Selecting between custom and standard load cells requires honest assessment of:
- Specific load characteristics and measurement objectives
- Actual environmental challenges in your operating environment
- True space constraints and mounting requirements
- Real-world performance needs and control system integration
- Applicable regulatory requirements and certification needs
By analyzing these factors against both custom and standard options, you can determine which approach provides the optimal balance of performance, reliability, and cost for your specific OEM application.
Contact Massload today to discuss your OEM load cell requirements and determine whether custom or standard solutions represent the best engineering approach for your application.