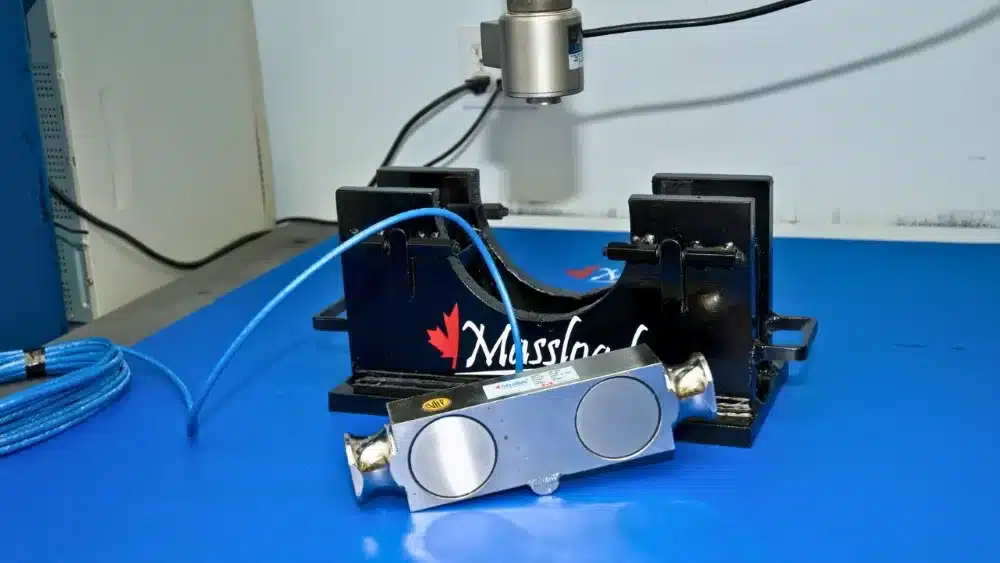
Nestled within the heart of every scale, load cells transform physical force into quantifiable data, offering a bridge between the physical and the digital.
But what elevates a load cell from a mere component to an indispensable asset? It’s a symphony of sensitivity, precision, and resilience, fine-tuned to perform under the most demanding conditions.
This exploration delves into the intricacies of load cell design, uncovering the elements that dictate their performance, durability, and, ultimately, their ability to meet the exacting standards of various industries.
How Does Load Cell Design Work?
At the heart of every industrial scale is a load cell, a device designed to convert force into electrical signals.
These come in various types, each suited to different applications. Whether it’s a canister load cell used in heavy-duty applications or a single-point load cell for platform scales, understanding the specific needs of your industry is key.
The principle behind these devices is straightforward: accuracy and reliability are paramount.
What Makes a Good Load Cell?
A superior load cell balances sensitivity, precision, and durability. It’s not just about measuring weight; it’s about doing so consistently, even in challenging conditions.
Performance Factors in Load Cell Design
1. Material Selection
The choice of material, often stainless steel or aluminum, plays a pivotal role in a load cell’s longevity and accuracy. Stainless steel is favored for its resilience in harsh environments, ensuring the load cell’s performance over time.
2. Sensitivity and Accuracy
These are the core of load cell performance. High sensitivity ensures minor changes in weight are detected, while accuracy guarantees these measurements are correct.
3. Temperature Compensation
Varied temperatures can skew a load cell’s readings. Incorporating temperature compensation mechanisms ensures consistent accuracy, regardless of environmental conditions.
4. Creep and Its Management
Creep refers to the gradual change in load cell output over time under a constant load, which can significantly affect long-term measurement accuracy. This phenomenon occurs due to the slow deformation of the load cell materials under sustained pressure. Effective management of creep includes selecting load cells designed with materials that minimize this effect and incorporating proper calibration procedures to compensate for potential creep over time.
5. Addressing Side and Eccentric Loads
Load cells are typically designed to measure force in a specific direction. However, side and eccentric loads occur when forces are applied at angles or positions that deviate from the load cell’s intended axis. This misapplication can distort measurement results and reduce the lifespan of the load cell.
6. Temperature Influence and Compensation
Temperature variations can significantly affect a load cell’s accuracy by causing material expansion or contraction, leading to output signal changes. Implementing temperature compensation within the custom load cell design is crucial for maintaining accuracy across a wide range of operating conditions.
7. Humidity’s Impact
Just as temperature affects load cell performance, humidity can also influence measurement accuracy over time. High humidity levels can alter the load cell’s material properties or electronic components, skewing the data.
8. The Crucial Role of Mounting
A load cell design guide shows the proper mounting for accurate measurements. An off-center mount can lead to significant inaccuracies, as the interaction between the measured product and the load cell is compromised. Following the manufacturer’s mounting instructions meticulously, ensuring clean and aligned surfaces, and verifying the orientation of the load cell are all vital practices. Additionally, the load path through the load cell must be singular and direct, avoiding any misalignment that could introduce measurement errors.
How Do You Determine the Accuracy of a Load Cell?
Accuracy is crucial to load cell performance. Calibration is essential, as is adjusting the load cell to ensure its readings are as close to the actual weight as possible. Equally important is how the load cell is mounted; incorrect installation can lead to inaccurate readings. Protecting the load cell from overload and minimizing signal noise are also crucial steps in maintaining its accuracy.
What Factors Should You Consider When Choosing a Load Cell for a Particular Application?
Selecting a load cell that can withstand these conditions without a dip in performance is essential. Understanding the load’s nature—whether static or dynamic—and ensuring the load cell is appropriately installed will maximize its efficiency and accuracy.
Environmental Conditions
The first step in selecting a load cell is to assess the environmental conditions it will face. This includes temperature extremes, humidity levels, exposure to corrosive substances, and the presence of potentially explosive gases or dust. For example, load cells used in outdoor agricultural equipment need to be waterproof and resistant to moisture, while those used in oil & gas applications may require intrinsic safety ratings to prevent the ignition of flammable gases.
Load Characteristics
Understanding whether the load will be static or dynamic is essential. Static loads require load cells that can maintain accuracy over long periods, while dynamic loads require load cells with high response speeds and the ability to withstand shock and vibration.
Accuracy Requirements
The required level of load cell accuracy is a critical factor. High-precision applications, such as pharmaceutical or aerospace component manufacturing, necessitate very high accuracy and repeatability.
Capacity and Range
The load cell must be capable of accurately measuring the maximum expected load while also providing reliable readings at the lower end of its range. It’s often advisable to select a load cell with a capacity slightly above the maximum expected load to avoid overload conditions.
Physical Size and Mounting Options
The physical space available for the load cell and the mounting configuration are important considerations. The load cell must fit within the designated area and be compatible with the mounting structure to ensure accurate force measurement.
Output Signal Type
The compatibility of the load cell’s output signal with the existing data acquisition or control system is another important consideration. Common output types include analog voltage, current (4-20 mA), or digital signals.
Material and Construction
The choice of material (e.g., stainless steel, aluminum) affects the load cell’s durability and performance in specific environments. Stainless steel is preferred for its corrosion resistance and strength in harsh conditions.
Legal and Regulatory Requirements
Depending on the application and location, there may be legal and regulatory standards that the load cell must meet, such as approvals for use in hazardous environments or compliance with industry-specific standards.
In the quest for accuracy, the design and selection of a load cell transcend mere technical specifications, evolving into a strategic decision that influences the efficiency and integrity of industrial measurements.
Whether braving the extremes of temperature and humidity or adapting to the dynamic forces at play, the load cell remains an unheralded protagonist in the narrative of technological progress.
In this complex interplay of factors, one truth remains constant: the right load cell is not just chosen; it’s engineered to excel in the specific theatre of its application, ensuring that every measurement, no matter how small, counts towards the larger goal of accuracy, reliability, and innovation.
Beyond Accuracy: Explore Load Cell Excellence with Massload
In a field where precision means everything, choosing the right partner for your load cell needs is crucial.
With Massload’s commitment to quality and innovation, your search for the perfect weighing solution ends here.