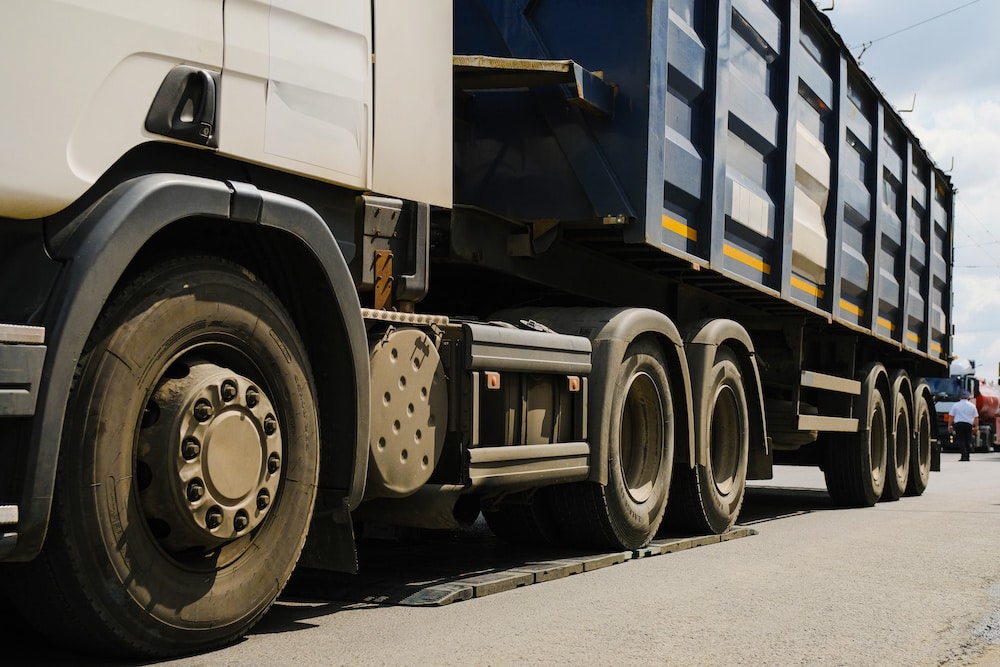
We all know that accurate weight measurement isn’t just a “nice-to-have” in mining operations—it’s absolutely critical. When you’re dealing with massive loads, extreme forces, and hazardous working conditions, precision becomes a safety issue, not just an operational metric. Inaccurate measurements in these environments don’t just hurt your bottom line; they can lead to catastrophic equipment failures, compliance violations, and worst-case, personnel injuries.
Mining operations across Nevada, Arizona, Wyoming, West Virginia, Pennsylvania, and Montana face some of the most challenging measurement environments imaginable. The combination of extreme loads, harsh conditions, and regulatory requirements creates a perfect storm where standard measurement technology often fails outright or degrades rapidly.
This is where high-capacity load cells designed specifically for mining applications come into play. These aren’t your standard industrial load cells with higher capacity ratings—they’re purpose-engineered measurement devices designed to maintain accuracy and reliability in conditions that would destroy conventional sensors within weeks or sometimes days.
Massload Technologies has been supplying these specialized load cells throughout the United States mining sector for decades. We’re not interested in selling you catalog items that “might work”—we engineer measurement solutions for your operation’s specific challenges.
What Are High-Capacity Load Cells, and Why Are They Essential for Mining?
Let’s get technical for a minute. High-capacity load cells are force transducers that convert mechanical force into measurable electrical signals, typically using strain gauge technology bonded to engineered metal elements. For mining applications, we’re typically talking about capacities ranging from 25,000 lbs to 250,000 lbs, though specialty applications sometimes require even higher ranges.
What makes mining applications different isn’t just the capacity requirements, though. It’s the combination of factors that create a uniquely hostile environment for precision measurement:
What Is the Load Cell Principle in Mining Operations?
The fundamental principle remains consistent with standard load cell technology—strain gauges detect microscopic deformation in the cell’s metal structure proportional to applied force, changing their electrical resistance. This resistance change is measured in a Wheatstone bridge configuration, generating a millivolt output signal proportional to the applied load.
The technical challenge arises when implementing this technology in mining environments where:
- Operating temperatures can swing from -40°F in Wyoming winters to 120°F in Nevada summers
- Constant vibration introduces signal noise and accelerates component fatigue
- Exposure to mining dust containing silicates and other abrasives degrades seals and cable entries
- Chemical exposure from process materials and groundwater creates corrosion issues
- Electromagnetic interference from high-powered equipment corrupts measurement signals
- Shock loading from operational anomalies creates forces well beyond normal measurement ranges
Standard load cells simply aren’t engineered for these conditions. Their sealing systems fail, their temperature compensation drifts, their cables degrade, and their structural elements develop fatigue cracks. The result? Erratic measurements, progressive drift, and eventual catastrophic failure—often at the worst possible moment operationally.
Mining-grade high-capacity load cells incorporate specialized features to overcome these challenges:
- Enhanced environmental sealing with redundant protection systems
- Wide-range temperature compensation circuits calibrated across operational extremes
- Heavy-duty cable systems with reinforced entry points and abrasion protection
- Special alloy selections with improved fatigue resistance and corrosion properties
- Signal conditioning electronics designed for noise rejection in industrial environments
- Structural designs with generous safety factors for shock and overload protection
These design elements ensure reliable measurement where standard load cells would rapidly degrade or fail outright.
Applications of High-Capacity Load Cells in US Mining Equipment
Vehicle Weighing for Surface and Underground Mining Vehicles
Mining vehicles represent massive capital investments, with typical haul trucks costing $3-5 million each. Operating these assets at optimal efficiency requires precise weight measurement to:
- Prevent payload underutilization that reduces operational efficiency
- Avoid overloading that results in payload dumping
- Avoid overloading that accelerates component wear and increases maintenance costs
- Ensure even load distribution to maximize tire life and structural durability
- Verify compliance with manufacturer specifications and safety guidelines
- Optimize fuel efficiency through proper loading practices
The technical challenge here isn’t just the high capacities (from 40,000-600,000 lbs per rear axle) but the ability to obtain accurate measurements despite:
- Uneven surfaces at measurement points
- Dynamic effects from vehicle positioning
- Temperature variations between morning and afternoon operations
- Dust and moisture contamination at measurement surfaces
- Vibration from engine operation during measurement
Mining operations throughout the U.S. implement specialized axle scales, vehicle weighbridges, and onboard weighing systems incorporating high-capacity load cells specifically designed for these challenging conditions.
Hoisting Applications In Underground Mining
Underground mining operations depend critically on hoisting systems to move personnel, equipment, and extracted materials through vertical shafts. The failure of these systems can have catastrophic consequences, making accurate load measurement absolutely essential.
Custom load pins represent an optimal technical solution for these applications by:
- Replacing existing structural clevis pins within rigging arrangements with minimal modification to the hoisting system
- Maintaining the mechanical integrity of the lifting system while adding measurement capability
- Providing real-time monitoring of forces without additional space requirements
- Delivering reliable measurement despite exposure to shaft conditions
- Integrating seamlessly with safety monitoring and control systems
- Provide optional 0-10V, 4-20mA or wireless connectivity to Process Line Controllers
These specialized components typically incorporate:
- 17-4 PH stainless steel construction for optimal strength and corrosion resistance
- Hermetic sealing systems rated to IP68 for prolonged submersion protection
- Integrated temperature compensation for the specific operating environment
- Reinforced cable connections or wireless transmission options
- Customized dimensions to exactly match existing equipment
These specialized devices incorporate enhanced safety factors (typically 10:1 rather than the standard industrial 3:1) along with redundant sealing systems to ensure reliability in the harsh conditions of underground mining. The implementation of these systems directly enhances both operational efficiency and safety margins in critical underground operations.
Galloway Workstage Platforms for Shaft Sinking and Development
Shaft development represents one of the most challenging aspects of underground mining. Galloway workstage platforms—multi-deck structures suspended in the shaft during development—require precise load monitoring to prevent dangerous overloading conditions.
Large custom tension links provide the optimal solution for these applications through:
- Direct in-line force measurement at critical suspension points
- Real-time monitoring of load distribution across multiple support points
- Early detection of developing overload conditions
- Documentation of loading history for safety compliance
- Integration with emergency systems for rapid response to unsafe conditions
These specialized devices incorporate enhanced safety factors (typically 10:1 rather than the standard industrial 3:1) along with redundant sealing systems to ensure reliability in the harsh conditions of shaft development.
Tensioning Machinery for Conveyor Belts
Conveyor systems serve as the arteries of mining operations, moving massive material volumes continuously throughout the facility. Proper belt tension is critical for operational efficiency, component life, and safety.
- High-capacity load cells in tensioning systems provide:
- Continuous monitoring of actual belt tension rather than inferred measurement
- Detection of dynamic tension variations during operation
- Early identification of developing mechanical issues
- Data for optimal tension adjustment to minimize wear and energy consumption
- Integration with control systems for automated tension management
Properly implemented, these systems significantly extend belt life while reducing energy consumption and maintenance requirements—a significant operational advantage in large mining operations.
Surge Bin Weighing
Surge bins provide critical buffer capacity between mining and processing operations. Accurate weight measurement in these applications enables:
- Real-time inventory management of extracted materials
- Optimization of downstream processing based on available material
- Prevention of overflow conditions that create safety hazards
- Detection of flow restrictions that could impact production
- Documentation of production volumes for reporting and planning
High-capacity load cells for surge bin applications must withstand not just the static load of the bin structure and contents but also the dynamic forces created during filling operations—a significant engineering challenge requiring specialized design approaches. In addition, suspended surge bins need to have centre of gravity monitoring to ensure stability throughout operations.
Shaft Girder Lifting and Installation
Mine shaft construction and rehabilitation involves the precise placement of massive structural components under challenging conditions. Wireless load pins used in these applications provide:
- Real-time monitoring of lifting forces without vulnerable cable connections
- Detection of load imbalances that could compromise installation safety
- Documentation of installation loads for engineering verification
- Enhanced safety through continuous monitoring during critical lifts
- Elimination of cable management issues in complex lifting operations
These specialized measurement systems significantly improve both safety and efficiency during critical shaft construction and maintenance activities.
Why Proper Calibration and Maintenance Are Important in Mining Applications
Even the most robust high-capacity load cells require regular calibration and maintenance to ensure continued accuracy in demanding mining applications. Key considerations include:
- Annual calibration verification against traceable standards
- Regular inspection of sealing systems and cable connections
- Signal verification to detect developing electronic issues
- Documentation of calibration history for compliance purposes
- Environmental protection assessment to prevent contamination
Through proper maintenance, mining operations ensure their measurement systems continue to provide the accurate, reliable data essential for both operational efficiency and safety compliance.
How to Choose the Right Load Cell for Your US Mine
Selecting appropriate high-capacity load cells for mining applications requires systematic engineering analysis considering:
- Actual load ranges during both normal and abnormal operations
- Environmental exposure specific to the installation location
- Mechanical integration requirements with existing equipment
- Signal output needs for compatibility with control systems
- Safety certifications required for the specific application
Massload Technologies specializes in helping mining operations navigate these considerations to select or design the optimal measurement solution for their specific operational requirements.
Massload’s High-Capacity Load Cells and Weighing Solutions for US Mining
The extreme demands of mining operations require specialized force measurement solutions beyond standard industrial products. Massload Technologies provides a comprehensive range of high-capacity load cells engineered specifically for the unique challenges encountered in mining applications throughout the United States.
Load Pins for Hoisting Applications
Custom-designed load pins serve as direct replacements for existing structural pins in hoisting systems while adding precision force measurement capability:
- Bucket Lifting Applications: Load pins installed in excavator boom linkages or bucket attachment points provide real-time weight data during material handling, enabling precise loading control and preventing equipment overload. These systems help operations in Nevada’s open pit mines and Wyoming’s surface coal operations optimize loading efficiency while preventing equipment damage.
- Shaft Boring Operations: Specialized load pins integrated into boring machine thrust systems monitor cutting forces and material resistance, providing critical data for operation optimization and equipment protection. The ability to monitor these forces in real-time helps operations in Arizona and West Virginia maintain optimal boring rates while minimizing tool wear and energy consumption.
The integration of force measurement directly into structural elements eliminates the need for separate load cells, simplifying installation while providing more accurate data under actual operating conditions.
Tension Links/Load Cells for Shaft Sinking
Shaft sinking operations represent some of the most challenging and safety-critical activities in mining. Specialized tension links provide crucial weight measurement during these operations:
- Galloway Work Stage Monitoring: Tension links installed at suspension points provide continuous monitoring of platform loading, ensuring even distribution and preventing dangerous overload conditions during shaft development work.
- Material Handling Verification: Tension links in material hoisting systems verify weights during concrete placement, steel installation, and equipment movement, preventing overloading while optimizing material transport.
- Emergency Systems Integration: Advanced tension links with alarm outputs provide immediate notification of abnormal loading conditions, triggering safety protocols before dangerous situations develop.
For operations in regions like West Virginia and Nevada, where shaft development is critical to accessing new resources, these measurement systems enhance both safety and efficiency in extremely challenging environments.
Pillow Block Load Cells for Sheave Mounting
Sheave assemblies represent critical points in hoisting systems where accurate load monitoring provides valuable operational and safety data:
- Winch Rope Load Monitoring: Pillow block load cells integrated into sheave bearings provide direct measurement of rope tension without requiring additional structural modifications or separate load cells.
- Balanced Load Verification: Multiple pillow block sensors installed at different points in the hoisting system ensure proper load distribution and detect developing imbalances before they cause operational issues.
- Duty Cycle Tracking: Continuous load monitoring through pillow block cells documents actual operating cycles for maintenance planning and component life prediction.
For underground operations in regions like Arizona and Wyoming, where hoisting system reliability directly impacts both safety and production, these measurement systems provide critical data while minimizing modifications to existing infrastructure.
Wireless Load Pins for Surge Bin Weighing
Surge bins serve as critical buffers between mining and processing operations, requiring accurate inventory monitoring in challenging installation environments:
- Underground Applications: Wireless load pins and tension links eliminate the vulnerability of cable runs in underground environments while providing real-time bin level data for production management.
- Surface Operations: For surface bins with complex structures or in remote locations, wireless systems simplify installation while providing reliable data transmission over significant distances.
For operations throughout the U.S. mining industry, these wireless systems eliminate one of the most common failure points in traditional measurement systems—damaged cables—while simplifying installation in difficult-to-access locations.
Regulatory Compliance Support
Beyond operational benefits, Massload’s measurement systems help mining operations meet increasingly stringent regulatory requirements:
- MSHA Documentation: Measurement systems provide objective load data for compliance with Mine Safety and Health Administration requirements regarding hoisting and lifting operations.
- Equipment Certification: Documented load testing and monitoring supports equipment certification and inspection requirements.
- Safety System Integration: Load measurement integrated with safety systems provides automated protection against overload conditions as required by various regulations.
- Record Keeping: Automated data collection supports the comprehensive documentation requirements for safety-critical systems.
These compliance benefits are particularly valuable for U.S. mining operations facing both federal oversight and state-specific regulatory requirements that vary across different mining regions.
High-Capacity Load Cells Are Changing the US Mining Industry
Emerging Technology Trends
The integration of advanced measurement technology with modern communication and data management systems is transforming how mining operations monitor and control critical systems:
- Wireless Mesh Networks: Advanced installations now implement mesh network topologies that provide redundant communication paths, ensuring data reliability even if individual transmission paths are interrupted.
- Cloud-Based Data Management: Integration with cloud platforms enables comprehensive data analysis across multiple sites, identifying operational patterns and improvement opportunities not visible in isolated systems.
- Mobile Interfaces: Smartphone and tablet applications provide maintenance personnel with real-time access to measurement data anywhere in the operation, enhancing response time for developing issues.
- Customized Software Solutions: Application-specific software transforms raw measurement data into actionable information tailored to specific operational requirements and management processes.
These technological advances are particularly valuable for multi-site operations in regions like Nevada and Wyoming, where centralized monitoring and analysis can optimize operations across numerous locations.
Supporting Mining Automation
U.S. mining companies increasingly implement automation to enhance safety, efficiency, and consistency in their operations:
- Autonomous Equipment Support: Load cells provide critical force and weight data necessary for safe operation of autonomous loading and hauling equipment.
- Process Control Integration: Measurement systems deliver real-time data to automated control systems, enabling closed-loop control of critical processes.
- Predictive Maintenance Systems: Continuous load monitoring feeds AI-based predictive maintenance platforms, identifying developing issues before they cause failures.
- Remote Operation Centers: Wireless load cell networks provide essential data to centralized control rooms, supporting the industry shift toward remote operation of critical systems.
For mining operations throughout the United States, these automation capabilities translate directly to improved safety, reduced operating costs, and enhanced productivity in increasingly competitive global markets.
Why Choose Massload for US Mining Applications?
Design for Mining Conditions
Mining environments present some of the most challenging conditions for measurement equipment, requiring specialized designs that go far beyond standard industrial products. These design characteristics ensure reliable performance in conditions that would quickly destroy standard measurement equipment, providing both accuracy and longevity in the most demanding applications.
Long-Term Reliability
Mining operations require measurement systems that deliver consistent performance over extended periods without requiring frequent maintenance or recalibration. This long-term stability translates directly to lower maintenance costs, reduced calibration requirements, and most importantly, consistent operational data for decision making and process control.
Customization and Durability
Standard catalog products rarely address the unique requirements of mining applications effectively. Massload’s custom engineering approach delivers solutions precisely matched to specific operational needs.
For mining operations across Nevada, Wyoming, Arizona, and West Virginia, this customization capability ensures optimal performance in their specific operating environments while minimizing installation complexity and maintenance requirements.
Take the Next Step in Enhancing Your US Mining Operations
Implementing high-capacity load cell technology specifically engineered for mining applications represents one of the most effective operational improvements available to modern mining operations. These specialized measurement systems enhance safety, improve efficiency, and reduce maintenance costs across multiple critical applications.
Contact Massload today to discuss your specific requirements and discover how our high-capacity load cell technology can transform your mining operations.
Since 1981, Massload Technologies has been engaged in the design and manufacture of strain gauge load cell transducers, electronic instrumentation, and scale products for mining and industrial weighing.
Today, Massload is Canada’s only VCAP-certified load cell manufacturer and has become a leading solutions provider of custom engineered load cells and weigh scales, supplying mining customers across North America and beyond. Massload load cells have demonstrated Proven Durability Under The Toughest Conditions.