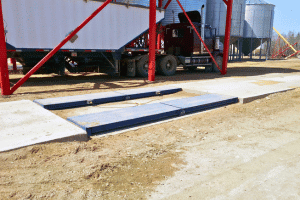
Mining hoisting operations are some of the most critical and potentially dangerous activities in the entire extraction process. When you’re moving multi-ton loads of personnel, equipment, and raw materials through vertical shafts at significant depths, there’s zero margin for error. A single miscalculation or equipment failure can lead to catastrophic consequences.
This is where high-capacity load cells come into play, though they’re frequently overlooked in system design. These force measurement devices have become essential technology for modern mining operations that demand both optimal safety and maximum operational efficiency. They’re not just “nice to have”—they’re critical engineering components that directly impact both your safety metrics and your operational throughput.
What Are The Advantages of High-Capacity Load Cells in Modern US Mining Operations?
At their core, high-capacity load cells function as force transducers, converting mechanical force into measurable electrical signals through strain gauge technology. But in mining applications, they’re doing far more than basic weight measurement—they’re providing critical real-time data on load distribution, dynamic loading effects, and potential overload conditions that could compromise both equipment integrity and personnel safety.
The technical advantages are substantial:
- Precision under extreme loads: Quality high-capacity load cells (including load pins, and tension links) maintain linearity within 0.1-1.0% even when measuring forces exceeding 100,000s of lbs
- Dynamic response capabilities: Good cells capture transient loading effects during acceleration/deceleration phases with minimal hysteresis
- Temperature stability: Properly compensated cells maintain calibration across thermal gradients from -40°F to +176°F.
- Signal integrity in noisy environments: Advanced cells provide clean outputs despite electromagnetic interference from drive motors and power systems
- Fatigue resistance: Engineered units withstand millions of load cycles without zero shift or sensitivity degradation
Massload Technologies has been supplying advanced load cell solutions throughout key mining regions in the USA, including operations in Nevada, Arizona, Texas, and West Virginia. The implementation challenges in these regions vary significantly due to different geological conditions and mining methods, requiring application-specific engineering rather than generic solutions.
The Secret to Safer, Smarter Hoisting
Preventing Overloads and Equipment Failures
Here’s the engineering reality that often gets overlooked: Most catastrophic hoisting failures don’t result from sudden, complete failures but from incremental degradation caused by repeated overloading just beyond design parameters. This creates cumulative fatigue damage that eventually leads to component failure under what appear to be “normal” operating conditions.
High-capacity load cells serve as the primary defense against this failure mode by:
- Providing accurate real-time loading data that prevents operation beyond design parameters
- Capturing dynamic loading effects that might otherwise go undetected
- Enabling trend analysis to identify developing mechanical issues before catastrophic failure
- Creating documented load history for maintenance planning and compliance verification
When properly implemented, these systems effectively transform hoisting operations from “best guess” management to data-driven precision that optimizes both safety and efficiency.
Protecting Hoist Cables from Dangerous Stress
Hoist cables represent one of the most vulnerable components in the entire system, with failure modes that can be difficult to predict through visual inspection alone. The technical challenge lies in the complex loading patterns these cables experience:
- Combined tensile and bending stresses as cables pass over sheaves
- Torsional effects during acceleration and deceleration
- Localized stress concentrations at attachment points
- Fatigue cycling during normal operations
- Potential resonant vibration under certain load conditions
Load cells provide critical data for cable management by:
- Monitoring actual tensile forces throughout the hoisting cycle
- Detecting load imbalances that could create abnormal stress patterns
- Identifying gradually increasing load resistance that might indicate developing mechanical issues
- Providing factual data for cable replacement scheduling based on actual loading history rather than arbitrary time intervals
This precision monitoring significantly extends cable service life while simultaneously reducing the risk of catastrophic failure—a classic engineering win-win that improves both safety and operational economics.
Smart Safety Features for Emergency Situations
The integration of high-capacity load cells into emergency response systems creates several advanced safety capabilities:
- Automated emergency braking triggered by load anomalies
- Detection of sudden load changes indicating potential equipment failure
- Backup monitoring systems that maintain safety monitoring even during primary system failures
- Data logging for post-incident analysis and system improvement
These capabilities transform safety systems from simple mechanical interlocks to intelligent monitoring systems that can detect developing problems before they become dangerous failures.
Keeping Lifting Operations Balanced and Controlled
Load balance represents one of the most overlooked aspects of hoisting safety. Imbalanced loading creates:
- Eccentric forces on guide systems that accelerate wear
- Uneven loading on hoisting mechanisms
- Potential binding during movement
- Accelerated fatigue in structural components
- Increased energy consumption during operation
High-capacity load cells, when deployed in multi-point monitoring configurations, ensure balanced loading throughout the hoisting cycle, significantly reducing these operational issues while extending equipment life.
Making US Mining Operations Faster and More Efficient
How Load Cells Streamline the Hoisting Process
Beyond safety improvements, properly engineered load cell systems deliver substantial operational benefits through:
- Optimized payload management: Maximizing load capacity without exceeding safety parameters
- Reduced cycle times: Enabling faster operation through precise load control
- Energy efficiency: Minimizing power consumption through balanced loading
- Decreased maintenance requirements: Reducing component wear through controlled operation
- Extended equipment life: Preventing cumulative damage from overloading
The technical ROI is clear—for a typical mid-sized mining operation, optimizing hoisting efficiency can increase material movement by 15-20% without additional capital equipment, directly impacting production economics.
Preventing Costly Breakdowns with Smart Monitoring
The maintenance economics of hoisting systems present a clear case for integrated load monitoring. Consider these engineering realities:
- Unplanned downtime typically costs 4-5x more than planned maintenance
- Component failures rarely occur without preceding load anomalies
- Most catastrophic failures result from cumulative damage, not single events
- Repair costs increase exponentially when failures damage multiple system components
Load cell monitoring transforms maintenance from reactive to predictive by:
- Identifying abnormal loading patterns before component failure
- Enabling condition-based maintenance rather than arbitrary time intervals
- Documenting actual load history for component life prediction
- Providing objective data for maintenance prioritization
This transition to data-driven maintenance typically reduces overall maintenance costs while simultaneously improving equipment availability—another dual benefit improving both operations and economics.
Built Tough for Harsh Mining Environments
The engineering challenge in mining applications extends beyond basic measurement to ensuring reliability in extremely hostile environments characterized by:
- Continuous exposure to corrosive dust and chemicals
- Temperature extremes from below freezing to >100°F
- High humidity and water exposure
- Constant vibration and occasional shock loading
- Exposure to electromagnetic interference from equipment
Quality high-capacity load cells for mining applications incorporate:
Sealed stainless steel construction (IP67/IP68/IP69K rated)
- Temperature compensation circuits calibrated across operational ranges
- Reinforced cable entries and connection systems
- Vibration-resistant mounting methods
- Advanced signal conditioning for electrical noise rejection
These design features ensure reliable operation where standard measurement systems would rapidly deteriorate or provide unreliable data.
Choosing the Right Load Cell for Your US Mine
Selection of appropriate high-capacity load cells for mining applications requires systematic engineering analysis considering:
- Maximum and typical loading: Not just peak loads, but the entire loading profile throughout operational cycles
- Environmental exposure: Specific temperature ranges, chemical exposure, and environmental contaminants
- Mounting constraints: Available space, attachment methods, and structural considerations
- Signal requirements: Output type, communication protocols, and control system integration
- Safety classifications: Certifications required for the specific installation environment
Each application presents unique challenges requiring thoughtful engineering rather than simply selecting the highest capacity available. Factors like frequency response, vibration resistance, and signal stability often prove more important than basic capacity ratings in determining actual performance.
Understanding Safety Ratings and Load Limits
Engineering safe hoisting systems requires understanding the critical differences between various load ratings:
- Rated capacity: The maximum load for which the cell is calibrated and specified
- Safe overload: The maximum load that can be applied without calibration shift (typically 150%)
- Ultimate overload: The load at which structural failure may occur (typically 300% for standard applications, but often >1000% for mining safety applications)
For mining hoisting applications, safety factors must account for:
- Dynamic loading during acceleration/deceleration
- Shock loading from operational anomalies
- Potential eccentric loading due to load shifting
- Progressive degradation of supporting structures
- Environmental factors affecting material properties
These considerations typically dictate selection of load cells with significant margins beyond theoretical maximum loads, particularly for personnel hoisting applications where safety consequences are most severe.
Custom Load Cells for Unique Mining Challenges
Standard catalog load cells rarely address the specific constraints of mining hoisting applications, particularly for:
- Headframe sheave monitoring
- Rope attachment sensing
- Galloway stage monitoring
- Skip/cage weight verification
- Winch drum force measurement
These specialized applications frequently require custom engineered solutions with:
- Purpose-designed mechanical configurations
- Specialized mounting features
- Enhanced environmental protection
- Application-specific signal processing, such as internal 4-20mA amplifiers
- Custom calibration protocols
The engineering investment in custom solutions delivers substantial returns through improved safety, reliability, and operational efficiency compared to compromised implementations using standard products.
Why Massload Is the Go-To for US Mining Load Cells
The extreme demands of mining hoisting operations require load cells engineered specifically for this challenging environment, not just adapted from general industrial applications. Massload Technologies has developed specialized high-capacity load cells that address the unique challenges of mining hoisting through purpose-built designs rather than compromised adaptations.
For a comprehensive look at how these specialized load cells transform mining operations, check out Massload’s informative video on mining applications.
Visit our YouTube channel to watch the mining applications video
High-Performance Engineering for Mining-Grade Load Cells
Mining hoisting applications demand measurement systems that maintain accuracy and reliability under conditions that would rapidly destroy standard commercial load cells:
- Exceptional structural design: Load cells for hoisting applications incorporate enhanced safety factors to account for the severe consequences of failure in personnel hoisting
- Environmental resilience: Sealed construction prevents contamination from mine dust and moisture, while specialized materials resist corrosion from mine water
- Temperature stability: Sophisticated compensation systems maintain calibration across the extreme temperature variations encountered in both underground and surface operations
- Enhanced vibration resistance: Optimized structural designs and advanced strain gauge bonding techniques prevent measurement drift despite the continuous vibration present in hoisting systems
These advanced engineering features translate directly to reliable, consistent performance under the extreme conditions encountered in mining hoisting applications, where measurement failures can have catastrophic consequences.
Continuous Duty Performance
Mining hoisting systems typically operate continuously, requiring measurement components that maintain stable performance without degradation:
- 24/7 duty cycle capability: Designed for continuous operation without performance drift or recalibration requirements
- Extended calibration stability: Maintaining accuracy over months or years rather than requiring frequent verification
- Superior fatigue resistance: Material selection and heat treatment optimized for millions of load cycles without sensitivity degradation
- Minimal maintenance requirements: Designed for “install and forget” operation with no scheduled service or adjustment
- Comprehensive self-diagnostics: Built-in signal validation ensuring measurement integrity is maintained
These characteristics ensure continuous, reliable operation in applications where measurement system failure can result in both significant safety hazards and substantial production losses.
Trusted by Mining Companies Across the U.S.
The practical challenges of mining hoisting operations vary significantly across different regions and mining methods. Massload Technologies has developed specialized expertise in addressing the unique requirements of major U.S. mining regions:
Mining companies trust Massload’s load cell technology based on demonstrated performance in the most demanding applications:
- Personnel hoisting systems: Where safety is paramount and measurement reliability directly impacts human lives
- Production-critical equipment: Where unexpected downtime creates substantial economic impact
- Harsh environment installations: Where standard measurement systems rapidly degrade
- Safety-certified applications: Where regulatory compliance requires documented reliability
- Remote operations: Where servicing is difficult and reliability is essential
This proven performance in critical applications has established Massload as a trusted partner for mining operations nationwide, providing measurement solutions that deliver both operational benefits and peace of mind in safety-critical systems.
The combination of application-specific design, regional expertise, and proven field performance makes Massload the go-to source for high-capacity load cells in mining hoisting applications throughout the United States.
Ready to Upgrade? Improve Your US Mining Hoisting with Massload
Implementing high-capacity load cell technology represents one of the most effective engineering improvements available for mining hoisting operations, delivering simultaneous benefits in safety, efficiency, and maintenance economics.
Massload Technologies specializes in developing custom-engineered load cell solutions specifically designed for the extreme demands of mining hoisting applications. Our engineering team understands both the theoretical and practical challenges of force measurement in these demanding environments.
Contact Massload today to discuss your specific requirements and discover how our high-capacity load cell technology can transform your mining hoisting operations.
Since 1981, Massload Technologies has been engaged in the design and manufacture of strain gauge load cell transducers, electronic instrumentation, and scale products for industrial weighing. Today, Massload is Canada’s only VCAP certified load cell manufacturer and has become a leading solutions provider of custom engineered load cells and weigh scales, supplying industrial customers across North America and beyond. Massload load cells have demonstrated Proven Durability Under The Toughest Conditions.