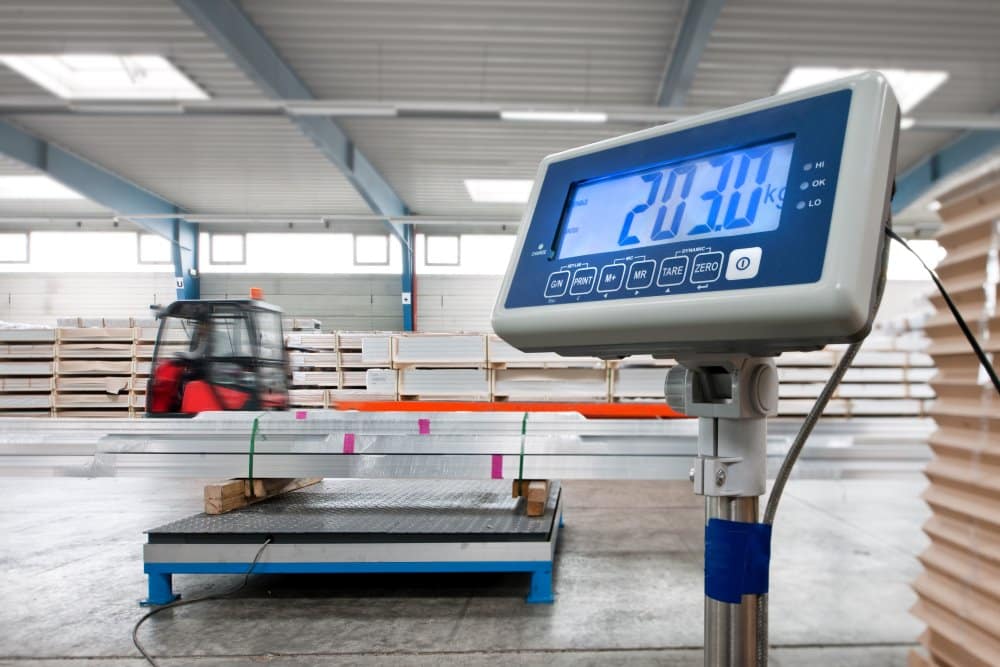
Automated process controls for weight measurement aren’t just a trend—they’re essential for industries aiming to stay competitive.
These advanced technologies accurately and efficiently measure and record material weights, delivering real-time data that seamlessly integrates into quality control processes.
Automated processing enables precise inventory management, improves quality control, and generates significant cost savings.
Harnessing real-time data from automated weighing systems empowers industries to optimize process controls, enhance production efficiency, ensure regulatory compliance, and make informed decisions.
If you’re interested in leveraging automated weighing solutions with real-time data in your industry, read on to learn more!
What are Automated Weighing Solutions?
Automated weighing solutions are advanced systems and technologies designed to measure and record the weight of materials or products accurately and efficiently without manual intervention.
Here Are Some Key Components and Features of Automated Weighing Solutions:
Load Cells and Sensors
These core components measure the weight of the material or product. Load cells convert the weight into an electrical signal the system can process.
Weighing Scales and Platforms
These include tank and hopper scales, bench scales, floor scales, conveyor scales, and other types designed to handle different sizes and types of materials or products.
Data Processing Units
These units receive the electrical signals from the load cells and convert them into readable weight data. They often include processors and analog-to-digital converters.
Software and Control Systems
Software systems collect, analyze, and store weight data. They can integrate with other process control systems to automate various functions. The most used software for this is WIM, or weigh-in-motion.
User Interfaces
These can include digital displays, touchscreens, or remote monitoring interfaces that allow operators to interact with the system, view weight data, and configure settings.
Connectivity and Integration
Automated weighing solutions often feature connectivity options such as Wi-Fi, Ethernet, or Bluetooth, allowing them to integrate with other industrial systems and databases.
Understanding the Industrial Weighing System Process
The industrial weighing system involves several critical steps to measure and manage weights accurately in various applications.
Here’s a Detailed Overview of Each Stage:
- Loading: The material or product is placed on the weighing platform, causing deformation in the load cells.
- Signal Generation: Load cells produce an electrical signal proportional to the weight of the load, typically a low-voltage analog signal.
- Signal Processing: Signals from multiple load cells are combined in a junction box before being transmitted to the data processing unit.
- Analog-to-Digital Conversion: The data processing unit converts the analog signal from load cells into a digital format for processing.
- Weight Calculation and Display: The digital signal is processed to calculate the weight and displayed on an indicator or screen in real-time.
- Data Logging and Analysis: Weight data is logged and stored for analysis using software tools to track trends and optimize processes.
- Integration with Control Systems: The weighing system integrates with other control systems to automate processes, such as ingredient addition in batching.
- Automation and Alerts: Configurable to automate processes like triggering alarms for weight limits, controlling conveyors, or adjusting feed rates in real-time.
Applications of Automated Weighing Solutions
- Manufacturing: Used for batching and mixing materials, ensuring consistent product quality and reducing material waste.
- Logistics and Warehousing: Helps track inventory, verify shipment weights, and optimize loading processes.
- Agriculture: Used for weighing crop inputs and fertilizers, crop yield, and livestock feed to ensure precise measurements and efficient resource use.
- Food and Beverage: Automated weighing solutions ensure accurate portion control, ingredient mixing, and packaging weights to maintain product quality and regulatory compliance.
- Mining and Quarrying: Used for weighing extracted materials, monitoring output, and optimizing transportation logistics.
10 Ways That Real-Time Data from Automated Weighing Solutions Can Optimize Process Controls
Here are ten forms in which real-time data from automated weighing solutions can optimize advanced process controls:
1. Inventory Management
Real-time weight data allows for accurate tracking of raw materials and finished goods, ensuring optimal inventory levels and reducing stockouts or overstock situations.
2. Production Efficiency
Automated weighing systems provide precise measurements that enable consistent production output, minimizing waste and rework and improving overall quality control process efficiency.
3. Quality Control
Continuous monitoring of product weight ensures that items meet specified standards, enhancing product quality and reducing the risk of defects.
4. Cost Reduction
Accurate real-time data helps optimize the use of materials, reduce waste, and lower production costs by ensuring that only the necessary amount of material is used.
5. Compliance and Reporting
Automated weighing solutions ensure compliance with industry regulations by providing accurate and timely data for reporting and audits, reducing the risk of fines and penalties.
6. Maintenance Scheduling
Real-time data can indicate when equipment is experiencing wear and tear, allowing for predictive maintenance and reducing downtime.
7. Supply Chain Management
Real-time data integration with supply chain systems enhances visibility and coordination, leading to better planning and execution of logistics and transportation.
8. Process Automation
Automated weighing systems can be integrated with other process controls to automate production lines, improving consistency and reducing manual intervention.
9. Energy Efficiency
Monitoring the weight of materials can help optimize energy usage in processes like mixing, blending, and transporting, contributing to energy savings.
10. Data-Driven Decision Making
Real-time access to weight data enables managers to make informed decisions quickly, improving responsiveness to changes in production demands or process issues.
The Weigh Forward: Achieve Peak Performance with Massload’s Automated Solutions
At Massload Technologies, we specialize in providing consultative manufacturing solutions tailored to your unique needs.
Our seasoned team of engineers is dedicated to helping you find the best automated weighing systems that leverage real-time data to optimize your process controls.
Ready to transform your operations with cutting-edge weighing solutions? Reach out to us today and let our experts guide you toward enhanced efficiency and productivity.