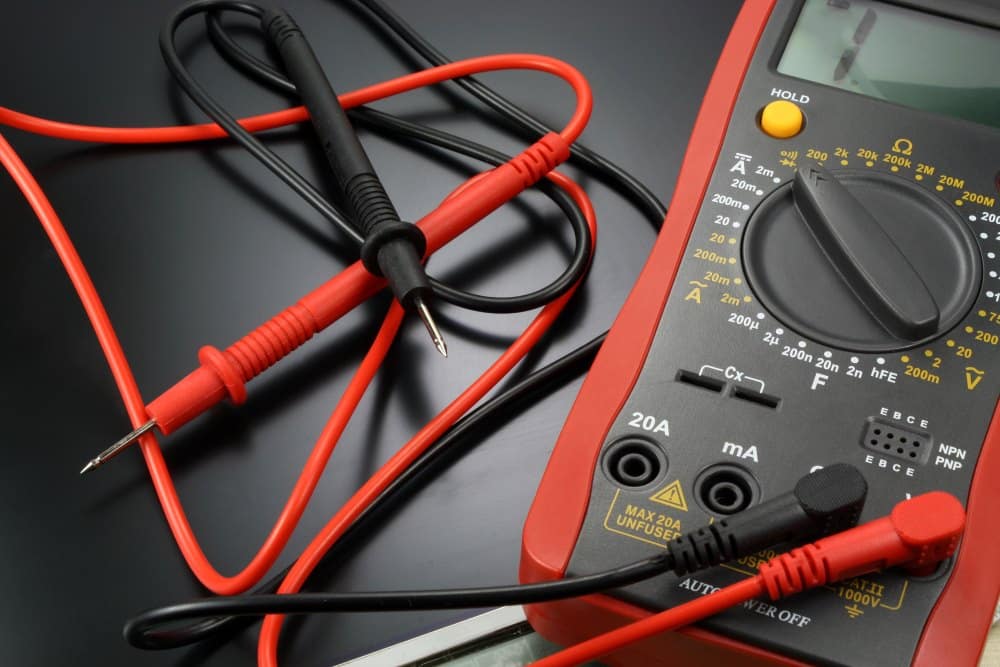
What happens when a load cell starts to falter? Testing and troubleshooting load cells is essential to maintaining the accuracy and reliability of your weighing systems.
In this guide, we’ll walk you through the key steps to identify issues, ensure optimal performance, and extend the lifespan of these vital components.
Whether you’re a seasoned engineer or new to the field, mastering load cell testing will keep your operations running smoothly.
How Do You Know if a Load Cell is Bad?
Key indicators of a bad load cell include visible physical damage, inconsistent or unstable output signals, and deviations from expected resistance values.
By performing a zero balance test, checking the excitation voltage, and measuring bridge resistance, you can assess whether the load cell is compromised.
Additionally, monitoring the load cell’s response under load and considering environmental factors can help identify issues that may require recalibration, repair, or replacement.
9 Steps to Troubleshooting Load Cells
Load cells are integral components in weighing systems, and their accurate functioning is critical for precise measurements.
However, like any electronic device, load cells can encounter issues that disrupt their performance.
Understanding how to test a scale load cell and assess its longevity is essential for maintaining system reliability. Below are the key steps to effectively troubleshoot load cells:
1. Visual Inspection
Before diving into technical tests, start with a thorough visual inspection. Check for any visible signs of wear, corrosion, or physical damage on the load cell and its connectors and cable..
Inspect the wiring for loose connections, fraying, or breakage, as these can affect signal transmission and lead to inaccurate readings.
2. Excitation Voltage Check
Load cells require a stable excitation voltage to operate correctly. Measure the excitation voltage supplied to the load cell and ensure it matches the manufacturer’s specifications.
Variations in voltage can lead to incorrect readings or complete failure of the load cell.
3. Zero Balance Test
Perform a zero balance test to determine if the load cell is functioning correctly without any applied load. Disconnect the load cell sense wires from the system and measure the output signal using a multimeter.
If the output is outside the manufacturer’s specified zero balance range (usually within ±1% of the full-scale output), the load cell may be damaged or faulty.
4. Bridge Resistance Test
Testing the bridge resistance is an essential step in load cell troubleshooting. An ohmmeter is used to measure the resistance between each pair of load cell terminals.
Compare the readings with the manufacturer’s specifications. Significant deviations may indicate internal damage or a fault in the load cell’s strain gauge or wiring.
5. Signal Output Test
To test how well the load cell responds under load, apply a known weight and measure the signal output. The output should be proportional to the applied load.
If the output signal is inconsistent or does not correlate with the known weight, the load cell might be compromised.
6. Insulation Resistance Test
An insulation resistance test can help identify moisture ingress or insulation breakdown within the load cell. Use a multimeter and/or megohmmeter to check the resistance between the load cell body and its signal lines.
Low insulation resistance suggests that the load cell may be exposed to moisture or has degraded insulation, leading to erratic performance.
7. Test for Load Cell Longevity
Understanding how long a load cell will last involves testing its performance over time and under varying conditions. Conduct fatigue testing by repeatedly applying and removing loads to simulate real-world usage.
Monitor the load cell’s output stability and check for any drift or deviation from the expected readings. This will give insights into the load cell’s lifespan and reliability under continuous use.
8. Environmental Assessment
Consider the operating environment where the load cell is installed. Factors like temperature fluctuations, exposure to chemicals, or heavy vibrations can affect load cell performance.
Troubleshooting should include an assessment of these environmental factors and determining whether the load cell is suitable for the conditions.
9. Calibration Check
Lastly, if all tests indicate the load cell is functioning correctly, ensure that it is properly calibrated. Regular calibration checks are essential for maintaining the accuracy of the weighing system.
If recalibration fails to correct measurement discrepancies, the load cell may need replacement.
How to Test a Scale Load Cell with a Multimeter
Testing a load cell with a multimeter is a straightforward yet crucial process to ensure your weighing system operates accurately and efficiently.
Load cells are precision devices that convert force into an electrical signal, and regular testing helps maintain their reliability.
Whether you’re troubleshooting an existing setup or checking the lifespan of your load cell, understanding the correct testing procedure is essential.
This guide will walk you through the steps of testing a load cell using a multimeter, with a focus on checking load cell resistance.
How to Check Load Cell Resistance
One of the key steps in load cell troubleshooting is to measure the resistance across its terminals. This helps determine if the load cell is functioning correctly or if there are internal issues affecting its performance. Here’s how to perform this test:
- Prepare Your Tools: Ensure your multimeter is set to measure resistance (ohms). Before starting, disconnect the load cell from any connected devices or power sources to avoid false readings.
- Identify the Terminals: Load cells typically have four or six wires. The common colors are red, black, white, and green, which correspond to excitation and signal pairs. Refer to the load cell’s wiring diagram to accurately identify the terminals.
- Measure Excitation Resistance: Place the multimeter probes on the excitation terminals (typically red and black wires). Record the resistance reading. This value should match the manufacturer’s specifications. A significant deviation indicates potential damage within the load cell.
- Measure Signal Resistance: Next, measure the resistance across the signal terminals (typically white and green wires). Again, compare the reading with the manufacturer’s specifications. Inconsistencies here can signal a fault in the load cell’s strain gauge.
- Cross-Check Terminal Pairs: For load cells with six wires, you may need to measure the resistance between additional pairs, such as sense wires, which help compensate for voltage drops. Ensure all readings are within the specified range.
- Assess the Results: If the resistance values are within the expected range, the load cell’s internal circuitry is likely intact. If not, it may indicate an issue such as wire damage, moisture ingress, or a failing strain gauge, all of which require further investigation.
Testing the Load Cell’s Functionality
Once you’ve checked the resistance, the next step is to test how the load cell responds under load. Here’s how to proceed:
- Apply a Known Load: Place a known weight on the scale connected to the load cell. Ensure the weight is within the load cell’s capacity range.
- Measure the Output Signal: Set the multimeter to measure millivolts (mV) and connect it to the signal output wires. As you apply the load, the output should change proportionally to the weight.
- Verify Against Specifications: Compare the output signal with the manufacturer’s specifications. The output should be linear and consistent with the applied load. Any deviation might indicate wear or damage, affecting the load cell’s accuracy.
How to Test How Long a Load Cell Will Last
The longevity of a load cell is influenced by several key factors that can affect its performance over time. Understanding these elements can help predict how long a load cell will last and ensure its reliability in various applications. Here are the main determinants:
1. Material Quality
- Construction Materials: The quality of materials used in the load cell, such as stainless steel, aluminum, or alloy, directly impacts its durability. High-quality materials are more resistant to environmental factors like corrosion, wear, and fatigue.
- Strain Gauges: The type and quality of strain gauges used in the load cell also play a significant role. Precision-engineered strain gauges with robust adhesive bonds ensure better performance over time.
2. Environmental Conditions
- Temperature: Load cells exposed to extreme temperatures, whether hot or cold, may experience material expansion or contraction, affecting accuracy and longevity.
- Humidity and Moisture: Prolonged exposure to moisture can lead to corrosion, insulation breakdown, and eventual failure of the load cell.
- Vibration and Shock: Load cells subjected to constant vibration or shock loading can suffer from mechanical fatigue, leading to a shortened lifespan.
3. Load Cell Design
- Rated Capacity: Operating a load cell within its rated capacity ensures its longevity. Overloading or consistently operating near the maximum capacity can accelerate wear and tear.
- Fatigue Rating: Load cells designed with high fatigue ratings are built to withstand numerous loading cycles without significant degradation in performance.
- Sealing and Protection: Load cells with proper sealing (e.g., IP ratings) offer better protection against environmental factors such as dust, water, and chemicals, extending their lifespan.
4. Operational Factors
- Loading Cycles: The number of loading and unloading cycles a load cell undergoes during its operational life is crucial. More cycles mean more stress on the load cell, which can lead to fatigue and eventual failure.
- Load Distribution: Uneven or off-center loading can cause additional strain on certain parts of the load cell, leading to premature failure.
- Calibration and Maintenance: Regular calibration and maintenance help detect potential issues early, preventing damage and extending the load cell’s life.
5. Application-Specific Factors
- Dynamic vs. Static Loads: Load cells in dynamic applications (e.g., weighing systems in motion) experience more wear than those in static applications.
- Exposure to Chemicals or Abrasives: In industries where load cells are exposed to chemicals or abrasive materials, there is a higher risk of corrosion or physical damage, reducing the load cell’s lifespan.
6. Manufacturer Specifications and Quality Control
- Manufacturing Quality: Load cells manufactured with strict quality control standards tend to have a longer lifespan due to fewer defects and better consistency.
- Warranty and Certifications: Load cells that come with longer warranties and relevant certifications often reflect a higher confidence in the product’s durability from the manufacturer.
Don’t Let Your Weighing Systems Go Off Balance
Ready to optimize your weighing systems and avoid costly downtime? Regular maintenance and calibration are key, but when unexpected issues arise, we’ve also got you covered.
Our highly recommended technical support team is just a call away at 1-306-242-2020, ready to assist with any challenge. Contact us today today to speak with one of our experts!
Don’t just take our word for it—view this glowing customer testimonial about how we saved the day with our reliable weighing solutions and dedicated service team!