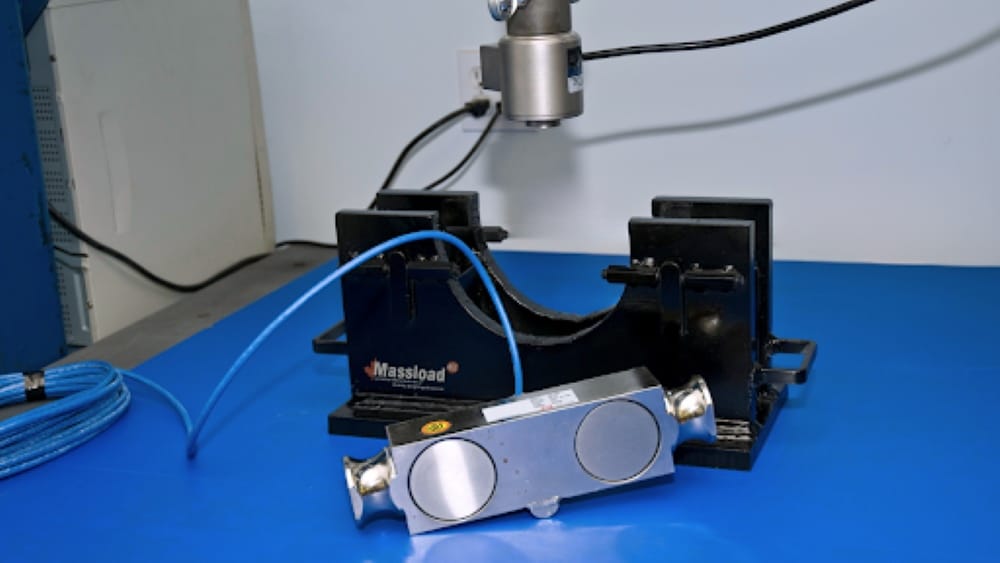
When you’re integrating load cells into OEM equipment, material selection often gets overlooked until you’re facing field failures or unexpected measurement drift. Yet this seemingly mundane decision can make or break your product’s performance in real-world conditions where theory meets harsh reality.
As an Original Equipment Manufacturer—whether you’re building agricultural machinery like seed tenders and grain carts, process equipment like mobile concrete batch plants, or specialized oil and gas equipment such as proppant tanks—your load cell material choices directly impact everything from initial accuracy to long-term field reliability. And the stakes are high: the wrong choice means warranty headaches, field retrofits, and the kind of conversations with customers nobody wants to have.
The materials science behind load cell performance isn’t just academic—it’s about ensuring your equipment delivers consistent results whether it’s operating in the Arizona desert, Michigan winters, or corrosive coastal environments. This isn’t about finding the “best” material—it’s about finding the right material for your specific operating conditions, measurement requirements, and economic constraints.
Massload Technologies has been engineering load cell solutions for OEMs throughout the United States and Canada since 1981.
We’ve seen firsthand how material selection can be the difference between equipment that performs reliably for years and systems that degrade within months of deployment.
Why Material Selection Matters for OEM Load Cells
The physics is straightforward: Load cells function by measuring microscopic material deformation. But that simple principle gets complicated fast when you’re dealing with real-world applications:
Measurement Accuracy and Stability
The elastic properties of your load cell material directly determine measurement performance:
- Elastic linearity—How consistently does the material deform in proportion to applied force? Lower-grade materials often show non-linear behavior, especially at the extremes of their range.
- Hysteresis—Does the material fully return to its original state after loading, or is there memory effect that creates measurement errors in cyclic applications?
- Temperature sensitivity—Most materials change their elastic properties with temperature. For equipment operating across wide temperature ranges, this can introduce significant measurement errors unless properly compensated.
- Creep characteristics—Under sustained loading, many materials continue to deform slightly over time. This creates the measurement drift that drives engineers crazy—readings that were perfect during testing but gradually shift out of spec in the field.
Environmental Resilience
This is where theory meets mud, dust, chemicals, and weather:
- Corrosion resistance: Not just against water, but against specific chemicals in your operating environment. The cleaning agents used in food processing equipment can be more damaging than the process materials themselves.
- Galvanic compatibility: What other metals contact your load cell? Mismatched materials create micro-galvanic cells that accelerate corrosion in the presence of even minimal moisture.
- Abrasion resistance: Particulates in the environment, especially in applications like cement batching or mining, can literally wear away protective coatings and expose base materials.
Perfectly good stainless steel load cells can fail rapidly in certain chemical environments where specialized coatings would have prevented corrosion, while in other applications, economical tool steel with proper plating outperforms more expensive alternatives.
What are the Common Materials Used in Load Cells?
The material selection palette for load cells isn’t infinite, but it offers crucial variations that significantly impact performance:
Alloy Tool Steel
Tool steels like 4140 and 4340 remain the workhorses of heavy-duty load cells for good reasons:
- High yield strength—Typically 600-900 MPa after heat treatment, providing excellent capacity range
- Cost-effectiveness—Approximately 40-60% the cost of comparable stainless options
- Excellent fatigue resistance—Critical for applications with high cycle counts
- Good machinability—Allows complex geometries at reasonable manufacturing costs
The main differences between common alloy steels aren’t just academic:
- 4140 offers better machinability and lower cost, making it suitable for general-purpose applications where extreme toughness isn’t required.
- 4340 provides superior impact resistance and fracture toughness, essential for applications with shock loading, extreme duty cycles, or lower temperatures.
The downside? Limited corrosion resistance. Even with electroless nickel coating (the standard protection), these materials remain vulnerable to corrosion if the coating is compromised—a common occurrence in abrasive environments.
Stainless Steel
When engineers talk about stainless for load cells, they’re usually referring to 17-4 PH (precipitation hardened) stainless—not your standard 304 or 316:
- Corrosion resistance that’s frankly remarkable across a wide range of environments
- Hardenability to high strength levels (1000-1100 MPa) that approach tool steels
- Excellent elastic properties when properly heat-treated
- Superior performance in wet environments without requiring additional protection
The downside? Cost. Expect to pay roughly twice what you would for tool steel alternatives, plus additional cost for machining. But in applications where corrosion is unavoidable, this premium typically pays for itself many times over through extended service life and measurement stability.
Aluminum
Don’t dismiss aluminum for appropriate applications:
- Weight advantage: At roughly 1/3 the density of steel, aluminum provides significant weight savings for portable equipment or applications where mass matters
- Natural corrosion resistance: The oxide layer provides inherent protection in many environments
- Thermal conductivity: Approximately 4x that of steel, creating more uniform temperature distribution that can improve measurement stability during temperature changes
- Cost-effectiveness: Material costs competitive with tool steels for many alloys
The limitations? Lower strength (typically 200-500 MPa depending on alloy and treatment) restricts aluminum to low and medium capacity applications. Aluminum also exhibits higher hysteresis than properly processed steels, potentially limiting precision in some applications.
Surface Coating
The base material tells only part of the story—surface treatments often determine field performance:
- Electroless nickel coating remains the gold standard for tool steel protection, providing excellent corrosion resistance without dimensional changes. But it’s not invincible—micro pockets or cracks from impact or abrasion can create corrosion pathways.
- Epoxy coatings provide additional protection in highly aggressive environments, though thickness control can be challenging for precision applications.
- Paint and powder coating offer economical protection for less demanding applications, particularly for agricultural equipment where cost constraints are significant.
In some cases, the right coating can extend load cell life from months to years in highly corrosive environments—a classic example where a small premium for proper treatment paid enormous dividends in field durability and reliability.
What to Consider When Choosing Load Cell Materials for OEMs
The material selection process requires a systematic evaluation of multiple factors:
Environmental Considerations
Start with a brutally honest assessment of your operating environment—not the idealized conditions of a test lab, but the worst-case scenarios your equipment will face:
- What temperature range will your equipment experience? Not just ambient, but considering solar loading, process heat, and seasonal extremes.
- What chemicals contact your load cells? Consider cleaning agents, process materials, and environmental factors like road salt or ocean spray.
- What physical abrasives exist in the environment? Cement dust, grain particles, and mining debris can wreak havoc on protective coatings.
At times, OEMs may be tempted to select materials based on typical operating conditions rather than worst-case scenarios, only to face field failures when their equipment encounters temperature extremes or unexpected chemical exposure.
Load Capacity & Measurement Range
Material selection directly impacts the practical capacity and precision of your measurement system:
- What’s your safety factor requirement? Different industries have different standards, from 1.5x rated capacity in some applications to 5x or higher in safety-critical systems.
- What’s your required resolution across the measurement range? Materials with different elastic modules provide different signal levels for the same deformation.
- Do you have fatigue concerns from cyclic loading? High-cycle applications may require premium materials with superior fatigue characteristics even if basic strength requirements could be met with standard alternatives.
Compliance & Industry Regulations
U.S. regulatory requirements can drive material selection independent of pure engineering considerations:
- FDA compliance for food processing equipment typically pushes material selection toward 17-4 PH stainless with specific surface finish requirements.
- Equipment for explosive environments may require materials and coatings with specific non-sparking characteristics.
- Military and aerospace applications often have detailed material traceability requirements that limit options to certified suppliers.
Durability & Longevity
Material selection directly impacts not just initial performance, but the long-term reliability and service life of load cells in OEM applications. This is where the real engineering trade-offs happen—balancing initial cost against total lifecycle performance.
Several material-dependent factors determine how load cells perform over extended periods:
- Fatigue resistance: Repeated loading cycles eventually cause microscopic structural changes in the load cell material. The right material selection can extend cycle life from thousands to millions of cycles. For high-cycle applications like vehicle weighing or vibrating equipment, this becomes the primary failure mode.
- Creep characteristics: Under sustained loading, many materials exhibit progressive deformation that doesn’t recover when the load is removed. This creates measurement drift that gradually degrades accuracy. Properly heat-treated alloy steels and certain stainless alloys show dramatically lower creep than aluminum or lower-grade materials.
- Hysteresis stability: The load cell’s ability to return to the same output for a given load, even after experiencing higher loads, degrades over time with some materials. This effect is particularly pronounced in aluminum load cells but can be minimized in properly processed tool steel and stainless variants.
- Corrosion progression: Even minor corrosion doesn’t just affect appearance—it changes the stress distribution in the load cell element, altering calibration and eventually compromising structural integrity. The right material selection prevents this entirely rather than merely delaying it.
The strain gauge technology itself is extraordinarily reliable—most load cell failures result from material or sealing issues, not strain gauge degradation. When properly bonded to appropriate substrate materials, strain gauges typically maintain calibration for decades.
What is the Best Material for a Load Cell in Your Specific OEM Sector?
The honest answer is always “it depends”—but here are some sector-specific considerations:
Process Batching Plants & Mobile Concrete Batch Plants
These represent some of the harshest environments for load measurement:
- Abrasive cement dust finds its way into every seam and connection
- Caustic materials attack many standard protective coatings
- Wide temperature swings from winter to summer operations
- Vibration from mixing and transport operations
- Periodic washdown that drives moisture into any available pathway
For stationary plants, 17-4 PH stainless often proves most economical despite higher initial cost. For mobile plants, the additional shock and vibration may require either premium stainless or alloy steel with resilient protection afforded by thicker high phosphorus electroless nickel coating, with enhanced sealing systems. Don’t underestimate the impact of transport vibration on coating integrity—what works for stationary equipment may fail in mobile applications.
Agriculture
Agricultural equipment presents unique challenges:
- Seasonal use patterns mean equipment often sits unused for months, creating corrosion opportunities
- Fertilizers and pesticides create unexpectedly corrosive environments
- Cost constraints in competitive equipment markets limit material options
- Wide temperature variations in field operations
- Exposure to impact and abrasion from normal operation
For high-capacity applications like grain carts, properly plated alloy steels typically offer the best balance of performance and cost. For precision applications like seed tenders, the measurement stability of stainless or aluminum often justifies their premium.
Oil and Gas
Few environments match the measurement challenges in oil and gas:
- Exposure to H₂S and other highly corrosive gases
- Extreme temperature ranges from desert to arctic operations
- Potentially explosive atmospheres requiring intrinsic safety
- High-pressure washdown during maintenance
- Remote installations where reliability trumps initial cost
For these applications, 17-4 PH stainless typically represents the minimum viable material, with exotic alloys required for extreme sour gas environments. The cost premium for premium materials is easily justified by the extreme consequences of failure and inaccessibility of many installations.
Construction
Construction equipment represents one of the most challenging applications for load cells, combining heavy loads with harsh environmental exposure and frequent shock loading. Material selection for these applications prioritizes robustness and longevity over absolute precision:
- High-strength alloy steels provide the optimal balance of strength, fatigue resistance, and cost for high-capacity applications in construction equipment. These materials withstand the frequent overloads and shock loading common in construction while maintaining reasonable accuracy.
- Surface treatments become critical in this sector due to exposure to weather, concrete dust (highly alkaline), and frequent washing. Electroless nickel coating (ENC) remains the industry standard, providing excellent corrosion resistance while maintaining dimensional stability for precision components. Note however, that ENC is available in a wide range of protection depending on thickness and phosphorus content, with lower priced products typically having a weaker protective coating.
- Stainless steel finds increasing application in critical components where failure risk must be minimized despite higher cost. The superior corrosion resistance proves particularly valuable in concrete processing equipment where exposure to corrosive materials may be unavoidable.
Applications like crane load monitoring, concrete batch weighing, and material handling systems benefit from these material selections, delivering the ruggedness construction operations demand while maintaining sufficient accuracy for operational requirements. The ability to withstand rough handling and overload conditions often proves more important than absolute precision in this sector.
Mining
Mining applications combine extreme loads with possibly the harshest environmental conditions in industrial weighing. Material selection must account for continuous exposure to abrasive dust, corrosive groundwater, extreme temperature variations, and constant vibration:
- Stainless steel becomes the default material for many mining applications despite its cost premium. The corrosion resistance proves essential in environments with acid mine drainage, high humidity in underground operations, and chemical exposure from mineral processing. 17-4PH stainless offers the optimal combination of corrosion resistance and mechanical properties for most mining applications.
- Nickel alloy steel such as 4340 and 4140 are most economical in applications that do not have aggressive environments.
Special alloys including Inconel, Hastelloy, or duplex stainless may be required for particularly aggressive chemical environments encountered in certain mineral processing applications. These materials provide exceptional corrosion resistance but at significant cost premiums. - Aluminum finds limited application in mining operations, primarily in non-critical or temporary installations where its lower cost and weight offer advantages. However, its limited fatigue life and susceptibility to certain types of corrosion restrict its use in permanent critical measurement systems.
- Enhanced sealing systems often become as important as the base material. Double or triple redundant sealing systems with specialized polymers resistant to mining chemicals protect the strain gauges and internal components from contamination.
Load cells in applications like conveyor belt tension monitoring, hopper weighing systems, and crusher load monitoring face continuous exposure to the mining environment while being expected to deliver reliable measurements for years without maintenance. This demanding combination makes material selection particularly critical for mining OEM applications.
Transportation & Logistics
The transportation sector presents unique material selection challenges, combining regulatory compliance requirements with exposure to road chemicals, weather extremes, and continuous vibration:
- Alloy steels with specialized coatings dominate high-capacity applications like truck scales, offering the necessary strength at reasonable cost. The high strength-to-weight ratio is particularly valuable in portable systems where weight impacts portability.
- Stainless steel finds application in specialized transport applications where regular washing or chemical exposure occurs, such as food transport or hazardous material handling. The ability to withstand regular sanitization without degradation justifies the cost premium.
- Aluminum plays a larger role in transportation applications than other sectors, particularly for on-board weighing systems where weight minimization offers operational benefits. However, its application requires careful design to account for its fatigue characteristics and lower elastic modulus.
- Material certification often plays a crucial role in transportation applications, particularly for systems used in regulatory weight enforcement. Materials must not only perform well but must be fully traceable and certified to maintain legal standing of weight measurements.
Load cells used in transportation applications must meet both technical performance requirements and regulatory standards. They must maintain accurate calibration despite road vibration, temperature cycling, and exposure to road chemicals like salt and de-icing solutions. Certification for legal-for-trade use adds another dimension to material selection, requiring proven stability and documented performance.
Contact Massload for Expert Guidance When Selecting OEM-Approved Load Cell Materials
Material selection for OEM load cells isn’t a theoretical exercise—it’s a practical decision with significant implications for your product’s field performance, reliability, and customer satisfaction. The right selection balances measurement requirements, environmental challenges, regulatory compliance, and economic constraints to deliver optimal performance in your specific application.
Massload Technologies has been engineering load cell solutions for OEMs throughout North America since 1981. Our technical team combines theoretical knowledge with practical field experience to guide material selection for optimal long-term performance.
Contact Massload today to discuss your specific OEM application and discover the material selection approach that will deliver optimal performance for your unique requirements.