Original Equipment Manufacturers
OEMs face unique challenges when integrating measurement capability into equipment designs. Operational forces often include vectors beyond simple gravitational loading, creating complex stress patterns that standard cells aren’t designed to handle.
We partner with OEMs to develop measurement solutions that function as integral components of equipment designs, not afterthought additions. This includes custom load pins for lifting equipment, specialized tension links for cable monitoring, and embedded force sensors for process control—all engineered to maintain accuracy while withstanding the mechanical stresses of equipment operation.
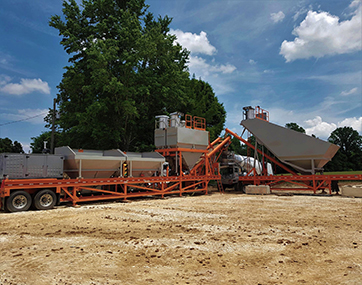
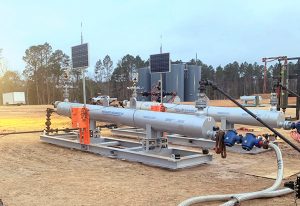
Manufacturing and Industrial Processing
Process weighing differs fundamentally from simple inventory measurement. Accuracy requirements often exceed commercial standards while operating conditions include vibration, temperature extremes, and chemical exposure beyond the capabilities of standard systems.
Our process weighing solutions incorporate:
- Vessel analysis to identify optimal mounting configurations
- Vibration isolation designed for your specific frequency spectrum
- Chemical-resistant materials matched to your process exposure
- Signal conditioning optimized for integration with process controls
Tank and Hopper Weighing and Batch Processing
Vessel weighing introduces complex structural interactions that standard load cell calculations don’t address. Thermal expansion, piping constraints, and material movement during processing all affect measurement accuracy.
Our engineered vessel weighing systems include:
- Structural analysis of support members and load introduction points
- Thermal modeling to account for expansion effects during operation
- Specialized mounting hardware that accommodates vessel movement
Agriculture
Agricultural applications combine harsh environmental exposure with continuous motion and shock loading during operation. Standard systems quickly deteriorate under these conditions.
Our agricultural solutions include specialized mounting systems for grain carts, feed mixers, and seed tenders that maintain accuracy despite field vibration and temperature extremes. These systems typically incorporate mechanical isolation, enhanced environmental sealing, and signal processing optimized for mobile operation.


Bulk Material Handling
Bulk material handling systems present unique weighing challenges due to the dynamic nature of material flow, environmental conditions, and the critical impact of measurement accuracy on operational efficiency:
- Flow Dynamics: Conventional weighing systems struggle with variable densities, flow rates, and material characteristics inherent in aggregate, mineral, and powder handling. Our engineered solutions incorporate customer-designed belt scales, weigh feeders, and impact flow meters that maintain accuracy despite material inconsistencies and flow variations.
- Harsh Operating Environments: Dust, vibration, temperature fluctuations, and continuous operation in bulk handling facilities quickly degrade standard measurement systems.
- Reliability Under Continous Operation: Our bulk material handling solutions are engineered for minimal maintenance requirements, featuring self-cleaning designs, accessible calibration points and modular components that facilitate service without extended downtime.
Crane and Hoisting
Lifting operations present unique measurement challenges where accuracy directly impacts safety and operational efficiency. Standard force transducers rarely address the complex mechanical stresses inherent in lifting systems:
- Structural Integration Constraints: Load cells must function as integral components of load paths without compromising mechanical integrity or introducing stress concentration points.
- Dynamic Loading Profiles: Measurement systems must handle startup acceleration, stopping deceleration, and occasional shock loading without degradation or zero shift.
- Environmental Exposure: Outdoor operations subject systems to temperature extremes, moisture intrusion, and UV degradation that standard protection methods inadequately address.
Our crane and hoisting solutions include custom load pins that directly replace existing structural elements, tension links with enhanced torsional stability, and wireless monitoring systems with redundant safety protocols. These systems maintain measurement accuracy while meeting the stringent safety requirements of lifting applications.
Transportation, Logistics, and Heavy Equipment
Mobile equipment combines challenging environmental exposure with continuous shock and vibration that quickly degrades standard measurement systems:
- Chassis Flexion Effects: Vehicle frames experience continuous flexion during operation, creating parasitic loads that standard mounting methods transfer directly to sensing elements.
- Temperature Cycling: Equipment operating between heated facilities and outdoor environments experiences rapid thermal cycling that induces substantial zero drift in conventional systems.
- Vibration Profiles: Road vibration, engine operation, and hydraulic systems generate complex vibration spectra that excite resonant frequencies in standard mounting arrangements.
Our transportation and heavy equipment solutions incorporate floating mount designs that isolate sensing elements from chassis flexion, advanced temperature compensation networks calibrated across operating ranges, and vibration damping tuned to application-specific frequency profiles.