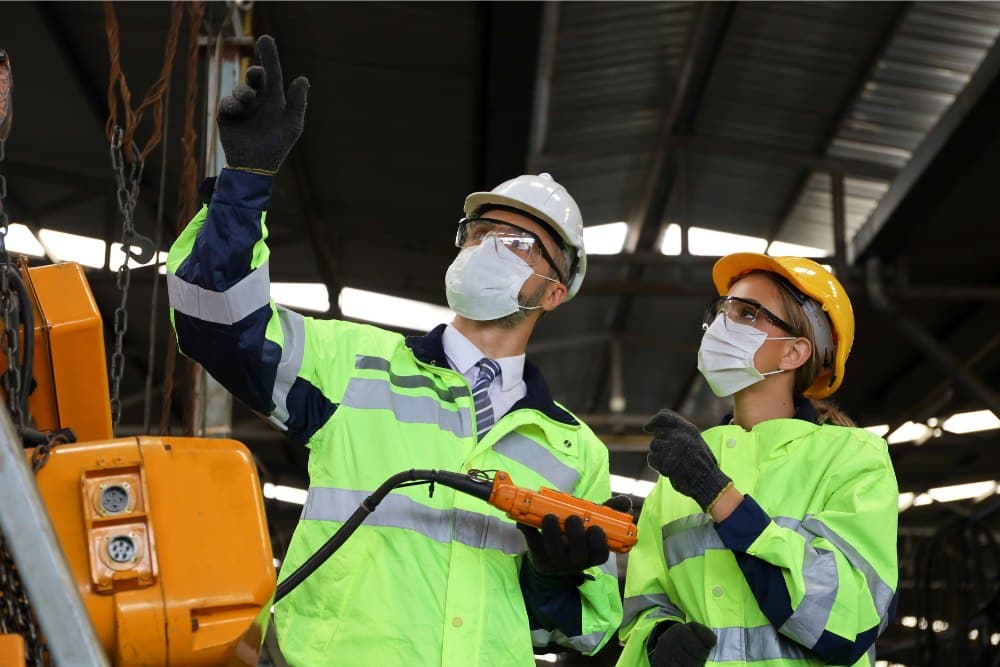
Strain gauges are everywhere in the manufacturing industry. They measure small deformations in structures or components by converting physical forces into electrical signals.
But with so many strain gauges out there, how do you choose the right one for your application?
Let’s get into the key factors to help you decide.
What is a Strain Gauge?
A strain gauge is a sensor that measures the strain, or change in length or deformation, of a material when subjected to forces like tension, compression, or bending.
It converts the applied force into a proportional change in electrical resistance. These are for safety, product design, and operational efficiency across industries.
In manufacturing and OEM, strain gauges are used to measure stresses and ensure optimal performance of critical parts.
In agriculture and construction, they measure the durability of equipment under heavy loads. In oil and gas, they measure pipeline integrity and structural safety.
How Does a Strain Gauge Work?
A strain gauge measures the deformation of an object under stress. It works on the principle of electrical conductance, which is affected by the geometry of the conductor.
When a conductor is stretched or compressed, its electrical resistance changes. This change in resistance can be measured precisely using a Wheatstone bridge circuit, which is the fundamental circuit that allows a strain gauge to work.
The gauge factor is the key in this process. Defined as the ratio of the change in electrical resistance to the mechanical strain, the gauge factor allows you to convert resistance changes into measurable strain. So you can measure the deformation of the object being monitored.
A strain gauge consists of an insulating flexible backing that carries a metal foil pattern. This foil is bonded to the object using a suitable adhesive like cyanoacrylate.
As the object deforms, the metal foil deforms, too, and its electrical resistance changes. This change is directly proportional to the strain of the object, so you get accurate and reliable readings.
Common Strain Gauge Applications
Here are some real-world applications of strain gauge transducers:
- Mining: Strain gauges are used to monitor heavy machinery to ensure critical components like shafts and gears perform under extreme stress.
- Agriculture: They are applied to weigh harvest loads and monitor equipment durability so farmers can make informed decisions about their machinery.
- Oil and Gas: Strain gauge applications monitor pipeline pressure and detect potential failures in pipelines or drilling rigs so operational safety is ensured.
- OEM and Manufacturing: Strain gauges are used in product testing to monitor stress and fatigue so the design can be improved and product longevity can be ensured.
Strain gauges also measure torque and power to ensure equipment reliability and safety in industries like power plants, maritime, automotive and aerospace.
Strain Gauge Benefits
Here are some common advantages of using strain gauges for your application:
- Precision: Strain gauges give you precise measurements, essential in detecting structural weaknesses or ensuring product quality in manufacturing. Strain gauges measures strain directly to infer values like stress, torque and deflection.
- Easy Installation: Strain gauges are easy to install, which is important in industries like construction and mining, where downtime is costly.
- Durability: With proper selection, strain gauges can operate in harsh environments like extreme temperatures in oil and gas or under constant load in lifting equipment.
- Cost-Effective: Strain gauges is a low cost solution for measuring critical forces so industries can maintain operational safety and avoid costly repairs or replacements.
What to Consider When Choosing a Strain Gauge
Choosing the right strain gauge transducer for your application depends on:
Geometry
Strain gauges come in different sizes and shapes to fit various installation spaces and measurement requirements. Consider the dimensions and layout of the strain gauge to the equipment or surface it will be monitoring.
For cranes or lifting and hoisting systems, the strain gauge must be aligned perfectly to the mechanical components so you get accurate force measurement without compromising the load cell’s integrity.
Strain Gauge Series
Different series are for different environments. For example, some applications of strain gauge transducers are for mining equipment that faces high stress, others for crane applications where dynamic loading requires gauges that can handle fluctuating forces. A typical strain gauge has a long thin conductive strip in a zig-zag pattern which is important for sensitivity and resistance measurement.
Connections
The type of connection (wired or wireless) affects how data is transmitted. In lifting and hoisting, wireless gauges are more flexible and convenient in confined spaces.
Temperature Response
Temperature changes can affect strain gauge readings. In oil and gas or mining, where extreme temperatures are common, you’ll need a strain gauge with thermal compensation to avoid errors.
At Massload Technologies, we use strain gauges with temperature compensation so you get consistent performance even in harsh environments.
Active Grid Length
Active grid length of a strain gauge affects its sensitivity and the area it measures. For high precision applications like OEM production lines, choose the right active grid length to get accurate data.
Electrical Resistance
Resistance of the strain gauge affects its signal output and power consumption. In agriculture or construction where equipment has to run in remote areas, choose strain gauges with optimal resistance to minimize power consumption and get precise results.
Durability and Installation
Strain gauges must be durable enough to withstand environmental factors like dust, moisture and mechanical wear. At Massload Technologies, we use strain gauges that are easy to install and highly resistant to environmental stress so you get long term reliability in applications like mining or manufacturing.
Strain Gauge Design and Selection
Strain gauges are designed for specific applications. They can be classified by:
- Type: Mechanical, electrical or optical strain gauges are used based on the application. Electrical strain gauges are used in OEM manufacturing lines for real-time stress analysis.
- Mounting: Bonded strain gauges are more suitable for equipment where long-term monitoring is required, like crane arms or construction machinery. Strain gauges bonded to transducers like pressure-sensitive diaphragms detect strain caused by various forces and pressures.
- Material: Most strain gauges are made of constant alloy, which reduces errors caused by temperature changes—an important consideration for oil and gas or mining applications where equipment runs under fluctuating environmental conditions.
Strain Gauge Accuracy and Calibration
Strain gauges are accurate when chosen, installed, and calibrated properly. Their accuracy comes from their ability to measure minute changes in deformation (strain) and convert this into a corresponding change in electrical resistance.
However, the accuracy of a strain gauge depends on the following:
- Gauge Quality: Higher quality strain gauges like those used in Massload Technologies’ load cells are designed to give consistent and precise readings even in harsh environments.
- Installation: Accurate installation is key. Any misalignment, improper bonding or environmental interference can affect a strain gauge’s readings.
- Temperature Compensation: Strain gauges are sensitive to temperature changes but those with built-in compensation like constant alloy based gauges maintain accuracy across temperature variations.
- Calibration: Calibration is crucial to ensure strain gauges maintain their accuracy over time. Calibration is more important in dynamic environments like crane lifting or mining operations.
One of the challenges in strain gauge measurement is temperature change. Temperature changes can make materials expand or contract and cause measurement errors.
For industries like oil and gas or agriculture where equipment is exposed to different climates, you need a strain gauge with built-in temperature compensation.
Choosing the right adhesive and proper installation can further reduce errors so you get more accurate readings.
Installation and Calibration
Installation and calibration is key to get accurate results from your strain gauge application. Most applications use a Wheatstone bridge circuit to detect the tiny change in resistance caused by strain. Number of active strain gauges in this configuration depends on the application.
Strain gauges are bonded to load cells, and when force is applied to the load cell, the strain gauge deforms and causes measurable changes in electrical resistance. This setup measures strain inside objects under stress.
For example, in lifting and hoisting equipment, the setup might have multiple strain gauges to measure forces in different directions.
Strain Gauge Load Cell FAQs
1. Can strain gauges measure stress?
Yes, strain gauges can measure stress. By measuring the strain on the object, the stress can be calculated using the material’s properties.
2. What is the difference between a strain gauge and a load cell?
A strain gauge measures the deformation of an object under stress, and a load cell measures the force on an object. Load cells often use strain gauges to measure the force.
3. Can strain gauges be used in high temperatures?
Yes, strain gauges can be used at high temperatures. However, the gauge material and adhesive must be suitable for the temperature range.
4. Can strain gauges be used in a corrosive environment?
Yes, strain gauges can be used in corrosive environments. However, the gauge material and adhesive must be suitable for the environment.
5. What is a typical foil strain gauge?
A typical foil strain gauge is an insulating flexible backing with a metallic foil pattern. The gauge is attached to the object with a suitable adhesive like cyanoacrylate.
6. How do strain gauges measure strain?
Strain gauge applications measure strain by detecting the change in electrical resistance across a thin conductive foil. The change in resistance is related to the strain by the gauge factor.
7. What are strain gauges bonded to?
Strain gauges are bonded to the object being measured with a suitable adhesive like cyanoacrylate.
Subscribe Now! Read More About Our Weighing Solutions
Read our other blog posts to learn more about load cells, weighing systems and how Massload Technologies can help you across industries.
Explore now and stay informed with expert insights tailored to your needs!