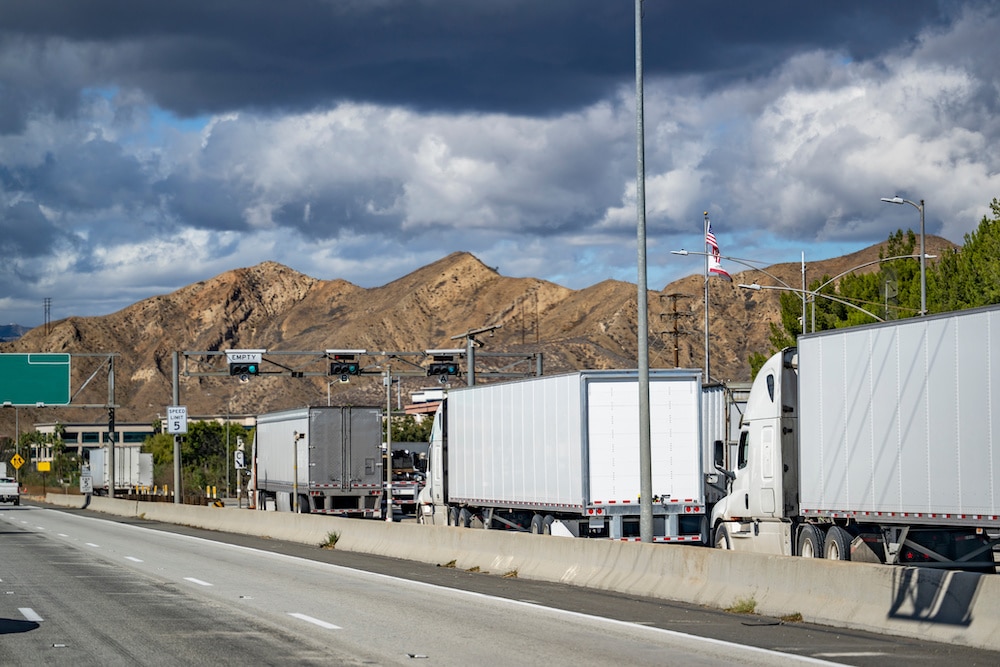
Integrating force measurement into OEM equipment designs isn’t just about picking a catalog item with the right capacity. It’s about finding (or designing) a measurement component that operates reliably in your specific mechanical environment, integrates with your control architecture, and maintains calibration despite whatever abuse your equipment will face in the field.
For OEMs developing equipment across agriculture, process control, construction, or dozens of other industries, proper load cell selection directly impacts your product’s field performance and reputation. This is particularly true in the competitive U.S. manufacturing landscape, where precision requirements keep tightening while operating environments get increasingly hostile.
Massload Technologies provides engineered measurement solutions to OEMs throughout the United States, with particular focus on the manufacturing centers of the Midwest, West and Southern regions. We’re not interested in simply selling components—we’re focused on ensuring your equipment performs as designed throughout its operational life.
How Are Load Cells Used in OEM Settings?
At their core, load cells convert mechanical force into measurable electrical signals. But in OEM applications, this simple concept gets complicated fast. You’re not just measuring static weight on a clean laboratory bench—you’re trying to extract accurate measurements while your equipment vibrates, experiences temperature swings, gets pressure-washed, and operates near electrical noise sources like VFDs and motor controllers.
Different load cell technologies tackle these challenges in fundamentally different ways:
- Strain Gauge Load Cells: Still the workhorses of industrial measurement, these use metallic or semiconductor strain gauges bonded to engineered metal elements.
- Applied force creates microscopic deformation detected as resistance changes in a Wheatstone bridge circuit. Simple concept, but implementation details determine whether they’ll last 10 years or 10 days in your application.
- Capacitive Load Cells: Measure changes in capacitance between plates as force alters their separation distance. Great for high-resolution applications but introduce their own challenges in electrically noisy environments.
- Hydraulic Load Cells: Use fluid pressure to transmit force measurements, eliminating electrical components from hazardous areas. Bulkier than electronic alternatives but practically indestructible in the right applications.
- Pneumatic Load Cells: Similar operating principle to hydraulic, but using air pressure instead of fluid. Inherently explosion-proof and contamination-free, making them ideal for specific niche applications.
The choice between these technologies isn’t academic—it directly impacts whether your equipment will function reliably in the field or become a warranty nightmare.
Why OEMs Require Custom Load Cell Solutions
Here’s the engineering reality most manufacturers won’t tell you: standard catalog load cells are designed for generic weighing platforms, not the complex force measurement requirements of sophisticated OEM equipment.
The challenges arise from fundamental mismatches:
- Load Path Complexity: Your equipment rarely loads cells in the idealized pure axial compression or tension that catalog cells are calibrated for
- Space Constraints: Your design may not have room for standard cell dimensions or mounting hardware
- Environmental Extremes: Your equipment might operate in conditions far outside the -40°F to +176°F operating range, low-humidity environment where standard cells are calibrated
- Signal Integration: Your control system needs clean signals despite the electrical noise generated by your equipment’s motors and drives
- Regulatory Requirements: Industry-specific standards often necessitate specialized materials, documentation, or design features
U.S. manufacturers face particularly stringent requirements due to regulatory frameworks from the FDA for food processing equipment, ASTM for construction and materials handling, API for oil and gas applications, and DoD specifications for military equipment.
What OEMs Need to Consider When Choosing a Load Cell
The engineering factors determining load cell selection go far beyond basic capacity ratings:
Load Capacity and Measurement Range
The conventional wisdom of “select a load cell with capacity 150% of maximum expected load” oversimplifies a complex decision:
- Operating Range: Where in the capacity spectrum do you need optimal accuracy? Cells are typically most linear in the 20-80% range of rated capacity.
- Resolution Requirements: What’s the smallest change you need to reliably detect? This often drives capacity selection downward.
- Dynamic Loading: Are there shock loads, vibrations, or accelerations that add force components beyond static weight?
- Safety Factors: What are the consequences of overload? Safety-critical applications require larger Factors of Safety.
These requirements often conflict, requiring engineering tradeoffs based on the specific measurement priorities.
Environmental Factors
This is where most field failures originate:
- Temperature Range: Both extremes and rate of change matter, as thermal expansion affects both zero balance and sensitivity.
- Moisture/Chemical Exposure: Not just whether exposure occurs, but specific chemicals and concentrations that contact the cell.
- Vibration Profile: Frequency and amplitude characteristics that can cause measurement errors or accelerate fatigue failure.
- Electrical Environment: EMI/RFI sources that can corrupt signals if not properly shielded and filtered.
Standard protection (typically IP67) is sufficient for controlled environments but often inadequate for the real-world conditions your equipment faces.
Different Types of Load Cells for OEM Use
Let’s break down the major load cell types in terms of their practical application advantages:
Strain Gauge Load Cells (Most Common Type)
Still dominating industrial applications due to their versatility and relatively low cost. Key points for OEM integration:
- Excitation Requirements: Typically 5-15V DC, with output proportional to excitation (mV/V), requiring stable power supplies for accuracy
- Temperature Effects: Zero balance typically shifts 0.036%/°F and span 0.036%/°F without compensation.
- Fatigue Considerations: Welded configurations generally outperform adhesive-bonded assemblies in high-cycle applications
- Moisture Vulnerability: Traditional strain gauge bonding is hygroscopic—moisture ingress causes drift over time
Best suited for OEM applications where:
- Cost-sensitivity is high
- Moderate accuracy (0.1-0.5%) is acceptable
- Environmental exposure isn’t extreme
- Integration space allows for standard form factors
Capacitive Load Cells (For High-Sensitivity Applications)
These excel in precision measurement where ultra-high resolution is required:
- Resolution Advantage: Typically 10x better than strain gauge technology
- Temperature Stability: Inherently less affected by thermal changes
- Signal-to-Noise: Higher output levels mean better resistance to electrical noise
- Overload Recovery: Excellent return to zero after overload events
Ideal for OEM applications requiring:
- Micro-force measurement (medical devices, lab equipment)
- Extended measurement range with high turndown ratios
- Superior long-term stability without recalibration
Hydraulic Load Cells (For Harsh Environments)
When reliability trumps precision, hydraulic cells shine:
- Explosive Environments: No electrical components at the measurement point
- Extreme Duty: Nearly indestructible in high-shock applications
- Remote Mounting: Pressure signals can be transmitted long distances
- Maintenance Advantage: Simple mechanical design means fewer failure points
Perfect for OEM equipment operating in:
- Hazardous areas requiring intrinsic safety
- High-shock and vibration environments
- Applications where electronics quickly fail
- Extreme temperature or pressure conditions
Pneumatic Load Cells (For Explosion-Proof Applications)
The niche solution when both explosion hazards and contamination concerns exist:
- Inherent Safety: No electricity or hydraulic fluid that could contaminate processes
- Cleanroom Compatibility: No risk of fluid leakage in sensitive environments
- Simplicity: Fewer components than hydraulic systems
- Low Maintenance: Self-cleaning operation through constant air flow
Best fitted to OEM applications in:
- Chemical and pharmaceutical processing with explosion risks
- Food processing where contamination prevention is critical
- Classified hazardous areas where intrinsic safety is mandatory
Load Button and Miniature Load Cells (For Compact OEM Devices)
Load button and miniature load cells provide force measurement in extremely space-constrained applications, offering precision in remarkably compact form factors. These specialized sensors feature:
- Compact dimensions: Typically ranging from 0.5″ to 2″ in diameter with minimal height
- Integrated mounting features: Often including threaded holes or studs for direct integration
- Precision measurement: Despite their small size, many offer accuracy comparable to larger cells
- Simplified integration: Designed for easy incorporation into existing structures with minimal modification
- Various capacity options: Available from a few pounds to several tons despite compact size
OEMs integrate these compact measurement devices into applications where space limitations prohibit standard load cell use, or where multiple measurement point are required in close proximity. Their small size makes them ideal for both new designs and retrofitting existing equipment with force measurement capability.
Multi-Axis Load Cells (For Complex Force Measurements)
Multi-axis load cells represent some of the most sophisticated force measurement technology available to OEMs. Unlike standard load cells that measure force along a single axis, these advanced sensors simultaneously measure forces and moments in multiple directions—typically three force components (Fx, Fy, Fz) and three moment components (Mx, My, Mz).
The technical complexity behind these devices is significant:
- Specialized strain gauge arrays: Carefully positioned to isolate and measure individual force components
- Advanced signal processing: Separating the interaction effects between different measurement axes
- Complex calibration procedures: Establishing accurate response across all measurement axes
- Sophisticated temperature compensation: Maintaining accuracy across all channels despite thermal effects
- Enhanced structural design: Providing consistent mechanical response with minimal crosstalk between axes
These multi-dimensional sensors find critical applications in:
- Robotics: Providing complete force feedback for robotic arms and end effectors, enabling precise control and safety monitoring during complex operations
- Aerospace testing: Measuring the complete force profile on components and structures during wind tunnel testing and structural validation
- Biomechanical analysis: Capturing the complex forces in prosthetics, orthopedic implants, and human movement studies
- Advanced manufacturing: Monitoring multi-directional forces during assembly, testing, and quality verification
For OEMs developing equipment requiring comprehensive force characterization, these sensors provide complete measurement in a single device, eliminating the complexity of multiple single-axis sensors while providing more accurate correlation between force components. The ability to measure all force vectors simultaneously transforms certain applications from basic force monitoring to sophisticated force control.
Single Point Bending Beam vs. Shear Beam Load Cells
These strain-gauge based designs represent common implementations for industrial OEM applications:
- Single Point Cells: Typically aluminum or steel bending elements with strain gauges mounted to measure bending strain.
- Usually single-ended: Fixed at one end, loaded at the other, capacities usually from 1kg to 1,000kg
- Compensate for off-center loading within specified limits
- Low profile form factor ideal for space-constrained designs
- Cost-effective for lower capacity applications
- Shear Beam Designs:
- Single-ended: Fixed at one end, loaded at the other, capacities from 110.23 lbs to 22,046.2 lbs
- Double-ended: Supported at both ends, loaded in center, capacities from 5,511.55 lbs to 220,462 lbs
- Superior stability in industrial environments
- Better overload protection than bending designs
- Ideal for medium to high capacity applications
What is the Best Type of Load Cell for OEM Applications?
There’s no universal “best”—it depends entirely on your specific requirements. But here’s a quick field guide:
- Need highest accuracy in controlled environment: Strain gauge (0.02%-0.10%) combined error)
- Need maximum resolution at low forces: Capacitive
- Need indestructibility in harsh conditions: Hydraulic
- Need explosion-proof, contamination-free: Pneumatic
- Need multi-directional force measurement: Multi-axis
- Need compact integration in tight spaces: Load button/miniature cell
For most industrial OEM applications, strain gauge technology still offers the optimal balance of performance, cost and design flexibility—but implementation details matter enormously.
How Do OEMs Determine What Load Cell to Use?
The systematic approach that prevents field failures:
- Document Actual Operating Conditions—not just ideal lab conditions:
- Real temperature ranges including rate of change
- All chemicals that contact the cell (cleaning agents are often overlooked)
- Vibration profiles during normal operation
- Electrical noise sources in proximity to measurement
- Define Precision Requirements Honestly:
- Actual accuracy needed (not marketing-driven “wish” specs)
- Stability requirements over time
- Calibration interval expectations
- Map Mechanical Integration Completely:
- Available space envelope
- Mounting points and structure stiffness
- Cable routing considerations
- Load introduction path
- Identify Regulatory Requirements:
- Industry-specific certifications needed
- Safety factors required
- Documentation and traceability needs
- Consult With Application Engineers:
- Work with specialists who understand both load cell theory and practical implementation
- Review application-specific failure modes before they occur in the field
- Evaluate cost/benefit of custom vs. standard solutions objectively
What are the Applications of Load Cells in OEM Systems?
Load cells find their way into diverse OEM equipment across multiple sectors:
Process Batching Plants & Mobile Concrete Batch Plants
These represent some of the harshest environments for load measurement:
- Cement dust that finds its way past many sealing systems
- Vibration that loosens connections and fatigues components
- Temperature swings from freezing mornings to baking afternoons
- Caustic materials that attack standard sealing materials
- Transportation shock for mobile plants
Load cells in these applications need exceptional environmental protection and mechanical durability while maintaining the accuracy needed for mix consistency.
Agriculture
Modern agricultural equipment integrates sophisticated weighing systems for:
- Seed and fertilizer application rate
- Yield monitoring during harvesting
- Livestock management and feed optimization
- Grain handling and storage management
These applications face unique challenges from continuous outdoor exposure, chemical contact with fertilizers and pesticides, rough terrain operation, and seasonal use patterns that include long storage periods.
Oil & Gas
Few industries present more challenging measurement environments:
- Explosive atmosphere hazards requiring intrinsic safety
- Exposure to hydrogen sulfide and other corrosive gases
- Temperature extremes from desert installations to arctic operations
- High-pressure washdown during maintenance
- Remote installations where reliability is paramount
Load cells in these applications require specialized design features, materials, and certifications beyond standard industrial offerings.
Mining & Construction
The combination of extreme loads, harsh environments, and safety-critical operations makes these demanding applications:
- Continuous exposure to abrasive dust
- Shock loading during material handling
- Vibration from equipment operation
- Weather exposure from outdoor operation
- Heavy cyclic loading that accelerates fatigue
Load cell solutions for these sectors must prioritize durability and reliability while maintaining sufficient accuracy for operational efficiency.
Transportation & Logistics
Transportation and logistics OEMs incorporate load cells for applications where accuracy, reliability, and regulatory compliance are essential:
- Vehicle weighing systems: Onboard scales for trucks, forklifts, and material handling equipment that provide real-time weight data to prevent overloading and optimize payload
- Cargo distribution monitoring: Load cells positioned strategically to ensure proper weight distribution for safety and compliance
- Shipping container verification: Systems that verify declared weights to meet international shipping regulations
- Automated sortation equipment: High-speed systems that weigh and route packages based on weight and dimensions
- Railway car weighing: Specialized load cells that withstand the unique dynamic forces of rail vehicles
U.S. transportation hubs in regions like Chicago, Memphis, Los Angeles, and New York implement these systems to ensure both operational efficiency and regulatory compliance. The load cell technologies used must withstand the specific challenges of transportation environments:
- Vibration and shock loading from vehicle movement
- Wide temperature ranges encountered during transport
- Exposure to road chemicals including salt and de-icing solutions
- Electrical noise from vehicle systems and nearby equipment
- Continuous duty cycles with minimal maintenance opportunities
The measurement data provided by these systems enables transportation companies to maximize payload efficiency while ensuring compliance with weight regulations that vary across different jurisdictions.
Material Handling & Crane Modernization
While full modernization projects typically fall under custom design work rather than original equipment manufacturing, many OEMs incorporate load cells into new material handling systems and cranes:
- Integrated load monitoring in lifting beams and hooks
- Overload prevention systems that prevent dangerous lifting attempts
- Load position monitoring that tracks both weight and location during lifting
- Dynamic load calculation that accounts for acceleration forces during movement
- Load summation systems that monitor multiple lifting points simultaneously
These integrated measurement systems enhance both safety and efficiency by providing accurate, real-time weight data throughout lifting operations. For OEMs, the key distinction from modernization projects lies in designing the measurement system as an integral component from the beginning, rather than adapting it to existing equipment.
This approach allows for more seamless integration, optimized performance, and often lower overall cost compared to retrofit solutions. The load cells used in these applications must withstand the demanding conditions of material handling:
- Dynamic loading during lifting and movement
- Shock loading from sudden stops or load shifts
- Environmental exposure in outdoor or industrial environments
- Continuous duty cycles in high-throughput operations
By integrating load measurement directly into the equipment design, OEMs can optimize both mechanical and measurement systems for maximum reliability and performance.
Our Custom Load Cell Solutions for OEM Manufacturers
When standard load cell configurations don’t meet the specific requirements of your OEM application, Massload Technologies provides custom-engineered solutions that address your exact needs:
Application-Specific Engineering
Rather than simply recommending catalog products, our engineering approach focuses on your specific application requirements:
- Detailed application analysis to understand the exact measurement needs and operating conditions
- Custom capacity optimization providing ideal measurement range without compromising overload protection
- Form factor customization for seamless integration with your equipment design
- Environmental protection tailored to your specific operating conditions
- Signal conditioning designed for your control system interface
This application-specific approach eliminates the compromises inherent in adapting standard products to specialized requirements, resulting in optimized performance, simplified integration, and enhanced reliability.
Comprehensive Development Support
Beyond the load cell itself, we provide complete support throughout the development process:
- Design consultation during your equipment development phase
- Prototype testing to validate performance in your specific application
- Production implementation support ensuring consistent quality in volume manufacturing
- Documentation packages supporting your quality and regulatory requirements
- Ongoing technical support as your applications evolve
This development partnership ensures your measurement system functions as an integral part of your equipment rather than an afterthought, enhancing both performance and reliability.
U.S. Market Focus
With extensive experience serving OEMs throughout the United States, Massload understands the specific requirements of the U.S. market:
- Regulatory compliance with U.S. standards and certification requirements
- Industry-specific expertise in key U.S. manufacturing sectors
- Regional support throughout major U.S. manufacturing centers
- Supply chain reliability ensuring consistent availability for production needs
- Technical documentation meeting U.S. quality system requirements
This market-specific focus ensures that our load cell solutions meet both your technical requirements and the broader business needs of manufacturing for the U.S. market.
Whether you’re developing agricultural equipment in the Midwest, mining machinery in the West, or specialized industrial equipment for nationwide distribution, our custom load cell solutions provide the precision measurement capability your applications require with the reliability your customers demand.
Trust Massload for Standard and Custom Load Cells and Weighing Solutions
The right load cell for your OEM application isn’t just about capacity—it’s about finding or engineering a measurement component that functions reliably in your specific operating environment, integrates seamlessly with your equipment, and delivers the accuracy your process requires.
Massload Technologies has been engineering standard and custom load cell solutions for OEMs across North America since 1981. Our technical team understands not just theoretical load cell principles, but the practical challenges of real-world industrial applications.
Contact Massload today to discuss your specific OEM measurement requirements and discover whether standard or custom solutions represent the optimal approach for your application.