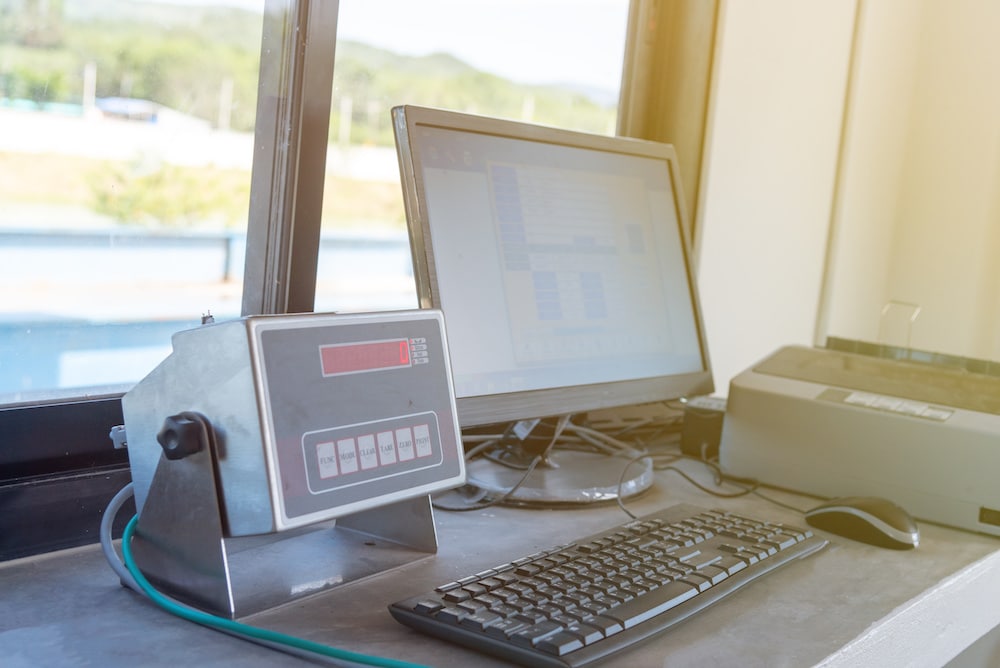
Conveyor belt failures in mining operations aren’t just annoying interruptions; they’re profit-killing disasters that cascade through your entire production chain. When a primary conveyor goes down in a typical mining operation, you’re looking at production losses that can easily hit $10,000+ per hour. Yet, many operations still rely on manual tension checks that are inconsistent at best and completely inadequate at worst.
The reality is that belt tension isn’t just some maintenance checkbox—it’s a critical operating parameter that directly affects belt tracking, material transfer efficiency, drive component life, and ultimately your operation’s bottom line. Modern mining operations are finally catching up to what process engineers have known for years: you can’t effectively manage what you don’t continuously measure.
Load cell automation is transforming belt tension from a maintenance guessing game to a precision-controlled parameter. By implementing strategically placed tension monitoring systems using properly specified load cells, mining operations across Nevada, Wyoming, Arizona, and other major US mining regions are dramatically reducing unplanned downtime while extending component life.
Massload Technologies provides specialized force measurement solutions engineered specifically for the harsh environments and unforgiving operating conditions of mining operations. Our load cells are designed to deliver accurate, consistent measurements despite dust, vibration, temperature swings and all the other challenges that make mining one of the toughest environments for precision measurement.
What Is Belt Tension and Why Does It Matter in Mining?
Belt tension isn’t just about keeping a conveyor tight enough to avoid slippage—it’s a complex balancing act between multiple competing requirements:
- Too loose: slippage, tracking problems, material spillage
- Too tight: excessive bearing loads, reduced belt life, increased energy consumption
- Uneven: tracking issues, belt damage, accelerated component wear
The real challenge? This optimal tension window constantly shifts based on load conditions, environmental factors, and belt aging. What worked perfectly at commissioning gradually becomes inadequate as the system ages, belting stretches, and components wear.
How Belt Tension Is Measured
Traditional tension measurement in mining operations has typically relied on three fundamentally flawed approaches:
- The “educated guess” method: Maintenance personnel manually adjusting based on experience and visual inspection
- Periodic manual measurement: Using portable tension meters at scheduled intervals
- Motor current monitoring: Indirectly inferring tension from drive motor load
All three methods share critical weaknesses: they’re either subjective, intermittent, or indirect—and none provide the continuous, accurate data needed for true process control.
Modern tension measurement using load cells takes a fundamentally different approach by directly measuring the actual force in the belt path or take-up system. Load cells can be integrated into:
- Take-up frames: Measuring the force applied by gravity or hydraulic tensioners
- Snub rollers or bend pulleys: Measuring the resultant forces from belt path changes
- Bearing blocks: Directly measuring the forces transmitted to pulley bearings
The advantage? Continuous, direct measurement of actual tension rather than indirect indicators or periodic snapshots.
How High-Capacity Load Cells Make Belt Tension Monitoring Easier and More Reliable
High-capacity load cells transform belt tension from a maintenance guessing game to a precisely measured operating parameter. The measurement principle is straightforward—the load cell’s elastic element deforms microscopically under load, causing precisely measured changes in strain gauge resistance—but the application engineering is where things get interesting.
Mining-grade load cells for belt tension applications require several specialized characteristics:
- High overload capacity: Belt systems experience shock loads during start-up, material transfer, and fault conditions that can easily exceed 2-3x normal operating tensions
- Vibration resistance: Conveyor structures transmit substantial vibration that can destroy standard load cells within weeks
- Environmental sealing: IP67/IP68 protection is the minimum viable for mining environments where dust and moisture are constant companions
- Temperature stability: Outdoor mining conveyors can experience 104°F temperature swings daily in desert operations
When properly specified and installed, these specialized load cells provide continuous tension data with accuracy typically within 0.1-1.0% of full scale—more than adequate for effective control while maintaining the robustness needed for mining applications.
Why Load Cells Are the Best Tools for the Job
The technical advantages of load cells over alternative measurement approaches are significant:
- Direct force measurement: Unlike indirect methods (e.g., motor current), load cells measure the actual tension force rather than a related parameter
- Continuous monitoring: Unlike periodic manual checks, load cell systems provide 24/7 data
- No moving parts: Solid-state operation with no mechanical wear mechanisms
- Field-proven technology: Strain gauge load cells have demonstrated decades of reliable operation in mining environments
- Integration capability: Standard output signals (mV/V, 4-20mA, 0-10V) easily interface with existing control systems
For mining operations that can’t afford conveyor downtime, these advantages translate directly to reduced failures, extended component life, and optimized operation.
The Benefits of Automating Belt Tension Monitoring
Implementing automated tension monitoring doesn’t just provide better data—it fundamentally transforms how conveyor systems are operated and maintained:
Enhanced Operational Efficiency
The efficiency improvements go well beyond just avoiding downtime:
- Optimal material transport: Properly tensioned belts carry maximum material with minimum belt wear
- Reduced energy consumption: Over-tensioned belts waste significant energy through increased bearing and flexing losses
- Decreased spillage: Proper tensioning ensures better belt tracking and reduced material loss
- Extended component life: Bearings, pulleys, and belting all last longer when operated at optimal tension
Reduced Downtime and Maintenance Costs
The maintenance impact is equally significant:
- Prevention of catastrophic failures: Early detection of tension issues before they cause belt damage or component failure
- Condition-based maintenance: Schedule interventions based on actual tension trends rather than arbitrary time intervals
- Simplified troubleshooting: Historical tension data provides invaluable insight for solving complex belt problems
- Reduced inspection requirements: Continuous monitoring eliminates the need for frequent manual checks
When a single conveyor failure can cost thousands per hour in lost production, the economic case for automated monitoring becomes compelling.
Improved Safety Performance
Safety considerations alone justify tension monitoring in many operations:
- Reduced belt slip: Proper tension monitoring virtually eliminates slip conditions that create fire hazards through friction
- Decreased manual inspection: Less need for personnel to access hazardous areas for routine checks
- Fire prevention: Early detection of mechanical issues that could lead to heating and fire risks
- Controlled start-up loads: Monitoring tension during sequential start-up prevents damaging shock loads
With increasing regulatory scrutiny on mining safety, these benefits address both operational and compliance concerns.
How Load Cells Are Used in US Mining Operations That Require Conveyor Belts & Mining Areas That Benefit from Load Cell Automation
Western Hard Rock Mining
Operations throughout Nevada and Arizona face particularly challenging conditions:
- Extreme temperature variations: From sub-freezing nights to 100°F+ days
- Extended conveyor runs: Often miles in length with multiple vertical and horizontal curves
- High capacity requirements: Moving thousands of tons per hour
- Dust-laden environments: Creating abrasive conditions that accelerate wear
These operations particularly benefit from tension monitoring on critical transfer points and high-angle conveyors where tension variations can cause immediate production issues.
Coal Mining Operations
Mining regions in Wyoming, West Virginia, and other coal-producing areas implement tension monitoring for:
- High-tonnage trunk conveyors: Where downtime costs are most severe
- Underground applications: Where access for manual inspection is particularly challenging
- Regenerative decline conveyors: Where proper tension is critical for safe braking
- Multiple flight systems: Where tension variations can cascade through transfer points
The high production volumes in these operations make the cost-benefit analysis for automated monitoring particularly favorable.
What is the load cell principle in mining?
The fundamental principle is straightforward: load cells convert mechanical force (tension) into electrical signals through strain gauge technology. When force is applied to the load cell’s elastic element, it causes microscopic deformation that changes the electrical resistance of strain gauges bonded to the structure. These resistance changes are measured in a Wheatstone bridge configuration, generating an output signal proportional to the applied force.
For mining applications, several specialized characteristics are essential:
- High overload capacity: Typically 150% safe overload and 300%+ ultimate overload protection, up to 1000% ultimate overload for safety critical applications
- Fatigue resistance: Ensuring long-term stability under millions of load cycles
- Temperature compensation: Maintaining accuracy across wide temperature ranges
- EMI/RFI protection: Shielding against electrical noise from VFDs and other equipment
When properly implemented, this measurement principle provides stable, accurate tension data despite the harsh conditions of mining operations.
What is a tension load cell?
Tension load cells are specifically designed to measure forces in tension (pulling) rather than compression. For conveyor applications, they typically feature:
- In-line mounting provisions: Clevises, rod ends, or threaded connections
- High axial load capacity: While rejecting off-axis loading
- Special cable management: Preventing one of the most common failure points
- Enhanced sealing: Often with redundant protection systems
- Wireless options: For cableless operation
These specialized designs are particularly valuable for direct measurement in belt take-up systems where the tensioning force is applied in a straight-line pull.
What is a conveyor load cell?
Purpose-designed conveyor load cells differ from general-purpose force transducers in several key ways:
- Mounting provisions: Designed for direct integration with conveyor structures
- Environmental protection: Specifically engineered for the mining environment
- Capacity ranges: Matched to typical conveyor tensions
- Installation simplicity: Minimizing conveyor modification requirements
These application-specific designs simplify implementation while maximizing reliability in the challenging conveyor environment.
Why Massload is the Right Choice for US Mining Load Cells
Built to Last in Harsh Mining Environments
Massload’s load cells are engineered specifically for the extreme conditions encountered in mining applications:
- Sealed construction: IP67/IP68 rated for protection against dust and moisture
- Wide temperature range: Operating capability from -40°F to +176°F
- Enhanced cable protection: Addressing the most common field failure point
- High shock resistance: Withstanding the impact loads common in mining operations
- Corrosion protection: Materials and treatments selected for mining exposure
These design characteristics ensure reliable operation where standard commercial load cells would rapidly fail.
Tailored Solutions for Mining Needs
Off-the-shelf load cells rarely cut it in mining applications. Every conveyor system has its own unique characteristics—belt width, tension range, mounting constraints, environmental exposure—that requires application-specific engineering rather than catalog-based selection.
Massload approaches belt tension monitoring from an application-first perspective:
- Custom capacities: Sized precisely for the application’s tension range rather than forcing you into standard increments that might be significantly oversized or dangerously undersized
- Application-specific mounting: Designed to integrate with your existing structure without major modifications or downtime
- Environmental optimization: Protection systems matched to your specific exposure conditions, whether it’s acidic mine water in underground operations or extreme UV and temperature cycling in desert installations
- Signal conditioning: Tailored to your control system requirements and electrical environment
This customization goes beyond simple mechanical adaptation. For example, a copper mine in Arizona might require special consideration for acidic runoff exposure, while a Wyoming coal operation might prioritize extreme temperature cycling performance. Generic products simply can’t address these specific requirements effectively.
The real value comes from this application-specific approach. Rather than compromising with “close enough” catalog products, you get measurement systems optimized for your exact operating conditions—which translates directly to better data, longer service life, and more reliable operation.
Expert Knowledge and Proven Reliability
Implementing effective tension monitoring isn’t just about buying load cells. It requires deep understanding of both measurement technology and conveyor dynamics. Massload brings critical expertise to these applications:
- Conveyor dynamics analysis: Understanding the complex interplay between tension, tracking, material loading, and component wear
- Installation optimization: Identifying the ideal measurement points for meaningful data without excessive complexity
- Calibration methodology: Establishing accurate baseline measurements and verification procedures
- Data interpretation: Translating raw measurements into actionable operational insights
- Troubleshooting expertise: Rapidly diagnosing issues when things don’t work as expected
This practical know-how comes from decades of field experience across hundreds of mining applications. We’ve seen what works and what fails in real-world conditions, not just laboratory testing.
Reliability in mining isn’t theoretical—it’s proven through performance in the harshest conditions:
- Continuous operation: Load cells that maintain accuracy despite 24/7 duty cycles
- Extended service life: Typically 5+ years without replacement in properly specified applications
- Minimal maintenance: No scheduled recalibration or component replacement
- Field repairability: Designed for practical maintenance when necessary
- Compatibility with existing systems: Seamless integration without obsoleting your current control infrastructure
When your operation depends on reliable conveyor performance, these factors matter far more than brochure specifications or laboratory accuracy claims.
Picking the Right Load Cell for Your US Mining Needs
Selecting the optimal load cell solution for belt tension monitoring requires systematic evaluation across multiple dimensions:
Application Analysis
Start with a detailed examination of your specific requirements:
- Tension range: What are your minimum and maximum tensions during normal operation? What about during transient conditions like start-up or fault scenarios?
- Measurement points: Where in your conveyor system can you most effectively measure meaningful tension data? Take-up frames often provide the simplest integration, but pulley bearings or direct belt path measurements may provide more actionable data.
- Control requirements: Are you simply monitoring for maintenance trending, or implementing closed-loop tension control? The latter demands higher accuracy and stability.
- Existing infrastructure: What control systems, communications protocols, and power supplies are available at the measurement points?
This analysis establishes the fundamental performance parameters your measurement system must deliver.
Environmental Assessment
Mining environments present significant challenges that often drive load cell selection more than basic capacity requirements:
- Temperature exposure: Both extremes and rate of change matter. Daily cycling from subfreezing to 100°F+ stresses sealing systems and affects measurement stability.
- Moisture conditions: Is your application exposed to rain, wash-down, or process water? Do you have high humidity conditions that create condensation during temperature changes?
- Dust exposure: Mining dust isn’t just a cleanliness issue—it’s often abrasive and chemically active. Silica dust, coal dust, and mineral particulates each present unique challenges.
- Chemical presence: Process chemicals, naturally occurring acids in mine water, and even cleaning solutions can attack standard sealing materials.
- UV radiation: Often overlooked, but ultraviolet exposure degrades many polymers used in cable jackets and sealing systems. UV resistant cabling is imperative in some harsh outdoor environments.
These factors often determine long-term reliability more than any other consideration, particularly in outdoor or harsh process environments.
Integration Requirements
Effective tension monitoring requires seamless integration with existing systems:
- Signal compatibility: What inputs does your control system accept? Common options include mV/V (requiring separate amplification), 4-20mA (standard for longer cable runs), and 0-10V.
- Communication protocols: For digital systems, what protocols are supported? Modbus, Ethernet/IP, Profibus, and others each have different integration requirements.
- Power availability: What power sources are available at the measurement points? Some load cell systems require regulated power while others can operate with standard 24VDC.
- Data management: How will you collect, store, and analyze the tension data? Without proper data management, you’re just collecting numbers without actionable insights.
Addressing these integration factors upfront prevents costly retrofits or compromised performance after installation.
Why Massload’s Custom Load Cells Are Ideal for US Mining
Mining operations present unique measurement challenges that demand specialized solutions. Massload’s engineering approach addresses these challenges through purpose-designed load cells rather than adapted general-purpose products.
Our approach to mining applications is thoroughly demonstrated in our informative video on mining load cell applications. This video showcases real-world implementations and the critical role that proper load cell selection plays in mining operations. The video highlights how Massload’s solutions address common challenges like dust exposure, vibration, and extreme temperature variations while maintaining measurement accuracy.
Visit our YouTube channel to watch the mining load cell applications video
Features illustrated in this video include:
- Custom load pin applications for hoisting and sheave monitoring
- High-capacity tension links for critical safety applications
- Specialized mounting solutions for existing infrastructure integration
- Wireless monitoring options for remote or hard-to-access applications
These application examples demonstrate how proper load cell technology implementation delivers real operational benefits in challenging mining environments.
Designed for Automation
Today’s mining operations increasingly implement automated control systems to optimize performance, reduce manpower requirements, and enhance safety. Load cells serve as the critical sensing elements that provide the data foundation for these automation systems.
Massload’s load cells are specifically engineered to support automation requirements:
- High signal stability: Providing consistent, reliable data even in electrically noisy environments with VFDs, motor starters, and high-power switching
- Fast response time: Capturing dynamic events that affect tension, such as material transfer impacts or start-up transients
- Standardized outputs: Direct compatibility with common PLC and control system inputs without complex signal conditioning
- Continuous operation capability: Maintaining accuracy during 24/7 operation without drift or degradation
- Self-diagnostics: Signal validation and fault detection to ensure measurement integrity
These characteristics transform load cells from simple measuring devices into critical components of comprehensive automation systems. For example, in conveyor applications, these load cells enable:
Automated tensioning systems: Maintaining optimal tension despite changing load conditions
- Start-up sequence control: Managing tension during the critical start-up phase when most belt damage occurs
- Preventive maintenance triggering: Initiating maintenance activities based on tension trend analysis rather than arbitrary schedules
- Emergency response systems: Triggering rapid shutdown when tension anomalies indicate potential failure conditions
The value of automation goes beyond simple labor savings. By maintaining optimal tension continuously rather than intermittently, these systems dramatically extend component life while reducing energy consumption and unplanned downtime.
Unlike basic measuring devices, automation-grade load cells maintain calibration stability over extended periods, provide consistent measurement despite temperature variations, and offer the reliability required for critical control systems. When your operation depends on automated systems, these performance characteristics directly impact your bottom line through improved uptime, extended component life, and optimized operation.
Reach Out to Massload for Your US Mining Solutions
Implementing effective belt tension monitoring through load cell automation represents a significant opportunity for mining operations to enhance efficiency, reduce downtime, and improve safety. The right measurement solution combines appropriate sensor technology with effective integration and support to deliver sustained operational benefits.
Massload Technologies provides comprehensive load cell solutions for mining operations throughout the United States, with particular expertise in belt tension monitoring applications. Our technical team understands both the theoretical principles and practical challenges of implementation in harsh mining environments.
Massload load cells have demonstrated Proven Durability Under The Toughest Conditions. Contact Massload today to discuss your specific tension monitoring requirements and discover how our load cell technology can transform your conveyor belt management from periodic manual inspection to continuous automated monitoring.