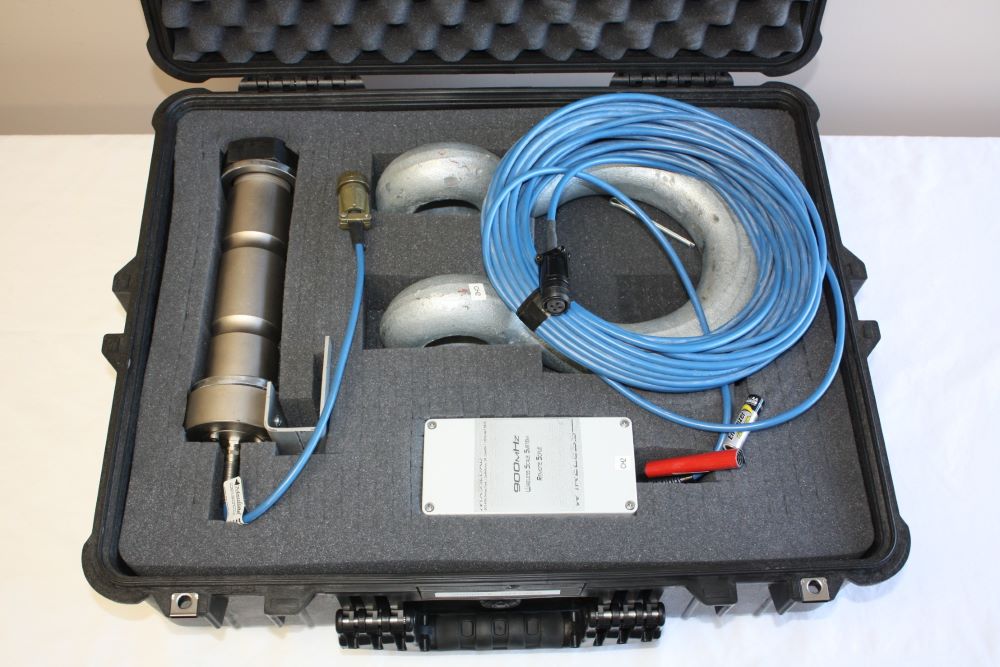
The process of custom designing load pins starts with thoroughly understanding the application’s requirements. This involves consultation between our engineers and the customer to define key parameters such as load capacity, environmental conditions, material specifications, and geometric constraints.
We create detailed 3D designs using advanced CAD software, which the customer reviews and approves before manufacturing begins. The design considers factors such as fatigue resistance, load, factor of safety, output, temperature variations, and potential side loads to ensure long-term durability and accuracy.
Keep reading to understand each step of this journey into efficiency and precision in detail.
How Does a Load Pin Work?
A load pin, also known as a force sensing pin, is a specialized transducer used to measure force or load in various applications. Here’s how it works:
Basic Operation
- Strain Gauges: Load pins are typically equipped with strain gauges bonded to the internal surface of a hole drilled through the pin (internally gauged). When a load or force is applied to the pin, the pin’s material deforms (strains). Some load pin designs require strain gauges to be mounted externally in strain pockets.
- Electrical Resistance: The strain gauges detect this deformation by measuring changes in electrical resistance. As the pin bends or compresses, the strain gauges stretch or compress, causing their electrical resistance to change.
- Signal Conversion: These resistance changes are converted into an electrical signal, usually a voltage, through the use of a Wheatstone bridge circuit arrangement. This signal is proportional to the force applied to the pin. The basic raw output is millivolts per volt (mV/V) but can be conditioned into other forms, such as 4-20mA, 0-10V, wireless, or other industry-standard outputs.
- Data Interpretation: The electrical signal is then interpreted by a data acquisition system or display unit, which translates it into a readable force measurement. This data can be monitored in real-time or logged for further analysis.
Applications and Installation
- Applications: Custom designed load pins are used in a variety of applications, including cranes and lifting equipment, marine and offshore platforms, aerospace, construction, mining and oil & gas plants and industrial and OEM machinery. They are particularly useful in scenarios requiring direct force measurement in confined spaces or challenging environments.
- Installation: Load pins are designed to replace existing clevis or pivot pins in machinery. They must be installed correctly to ensure accurate measurements, which includes proper alignment to avoid side loading and secure attachment to prevent movement. Additional components like keeper plates may be used to maintain alignment and stability.
Advantages
- Durability: Load pins are constructed from robust materials such as stainless steel, making them durable and suitable for harsh environments.
- Accuracy: With proper calibration, load pins can achieve high accuracy, often within 0.1% to 1% of the full scale.
- Versatility: They can be customized to fit various applications, from small-scale measurements to extremely high load capacities.
A load pin uses strain gauges to measure the deformation caused by applied loads, convert this deformation into an electrical signal, and interpret this signal to provide accurate force measurements.
Proper design, calibration, and installation are essential to ensure their effectiveness and reliability in various industrial applications.
How to Make a Loading Pin?
Creating a custom load pin involves several detailed steps, from initial design to final installation.
Here’s a comprehensive overview based on industry practices:
1. Design and Specifications
Consultation and Requirement Gathering
- Client Consultation: Begin with a detailed discussion with the client to understand the specific requirements, including load capacity, factors of safety, force and support arrangements, temperature range, environmental conditions, material preferences, and geometric constraints and signal output type.
Design Process
- CAD Modelling: Use advanced CAD software to create a detailed 3D model of the load pin. This includes defining dimensions, material properties, and placement of strain gauges.
- Finite Element Analysis (FEA): Perform FEA to simulate the load conditions and ensure the design can withstand the specified forces without failure.
- Client Approval: Share the design with the client for review and approval before manufacturing.
2. Manufacturing
Material Selection
- Choose high-strength materials like stainless steel (e.g., 17-4PH) that can endure high stress and harsh environmental conditions.
Machining
- Drilling and shaping the pin to the specified dimensions, including drilling holes for strain gauges.
- Heat treating of material to required harness followed by surface conditioning.
- Bonding preparation and attaching strain gauges to the internal surface of the pin in a way that maximizes sensitivity and minimizes interference from external factors.
- Testing to ensure the integrity of the strain gauge circuit and collection of performance parameters such as mV/V output, non-linearity error, etc.
Assembly
- Integrate signal conditioning electronics if required. This might include amplifiers, transmitters, or wireless modules to facilitate data collection and transmission.
3. Calibration
Initial Calibration
- Use calibration adapters replicating the application conditions to calibrate the load pin.
- This ensures the calibration reflects the real-world stress distribution and loading conditions.
Multi-Point Calibration
- Conduct multi-point calibration to enhance accuracy, typically achieving precision levels of 0.1% to 0.2% of the full scale.
Verification
- Verify the calibration against known standards and adjust as necessary to ensure the load pin provides accurate and consistent readings.
4. Installation
Site Preparation
- Ensure the installation site is ready and meets the requirements for alignment and mounting.
- This may involve preparing the mounting points and ensuring they are free from debris and contaminants.
Mounting the Load Pin
- Carefully install the load pin into the designated position, ensuring proper alignment to prevent side loading.
- Use keeper plates or other devices to maintain alignment and stability.
Connection and Setup
- Connect the load pin to the data acquisition system or display units. Ensure all electrical connections are secure and protected from environmental factors.
Final Calibration and Testing
- Perform a final calibration in situ to ensure the load pin operates correctly under actual working conditions.
- Conduct thorough testing to verify accuracy and reliability.
By following these steps, manufacturers can create custom loading pins that meet precise specifications and perform reliably in various industrial applications.
At Massload, we have our proprietary load cell manufacturing process, which you can understand further in this article.
How to Install Custom Loading Pins?
Proper installation is critical to ensure the load pin functions correctly and maintains accuracy. Installation guidelines often include instructions for orienting the load pin correctly, securing it with keeper plates to prevent side loading, and ensuring it is integrated seamlessly into the existing structure.
Anti-rotation devices may also be used to maintain proper alignment. The installation process is tailored to the specific application, whether it involves replacing a sheave pin in a lifting device or integrating the load pin into a complex machinery setup.
Installing a custom load pin involves several critical steps to ensure accurate and reliable force measurements. Here’s a detailed guide on the process:
1. Preparation
- Review Specifications: Before installation, thoroughly review the load pin specifications and installation instructions provided by the manufacturer. Ensure you understand the requirements for alignment, mounting, and electrical connections.
- Site Preparation: Prepare the installation site by cleaning and inspecting the mounting points. Make sure that the mounting holes are free of debris and contaminants to avoid any interference with the load pin’s performance.
2. Installing the Load Pin
- Alignment: Proper alignment is crucial to avoid side loading, which can affect the accuracy of the load pin. Use alignment tools or fixtures if necessary to ensure the load pin is positioned correctly within the mounting holes.
- Mounting:
- Insertion: Carefully insert the load pin into the designated holes. Ensure it fits snugly and is aligned with the load direction.
- Securing: Use keeper plates or other securing mechanisms to hold the load pin in place and prevent rotation or displacement. These components help maintain the correct orientation and ensure consistent load application.
3. Electrical Connections
- Wiring: Connect the load pin to the data acquisition system or display units. Ensure all electrical connections are secure and protected from environmental factors such as moisture or mechanical damage.
- Signal Conditioning: If the load pin includes built-in signal conditioning electronics, verify that they are properly connected and configured.
- This may involve connecting amplifiers, transmitters, or wireless modules as specified by the manufacturer.
4. Calibration and Testing
- Initial Calibration: Perform an initial calibration of the load pin to ensure it is functioning correctly.
- Use calibration equipment that replicates the actual application conditions to verify the accuracy of the load pin’s measurements.
- Verification: After initial calibration, verify the readings under no-load and loaded conditions. This helps identify any potential issues with the installation or calibration process.
- In Situ Calibration: Conduct a final calibration with the load pin installed in its actual working environment.
- This step ensures that the load pin provides accurate measurements under real-world conditions.
5. Final Checks and Maintenance
- Inspection: Inspect the entire setup to ensure all components are securely mounted and properly connected.
- Check for any signs of wear or damage that could affect performance.
- Routine Maintenance: Establish a routine maintenance schedule to inspect and recalibrate the load pin periodically. This ensures long-term accuracy and reliability.
Following these steps, you can ensure that your custom load pin is installed correctly and functions reliably in its intended application.
Proper installation and calibration are crucial for achieving precise and consistent force measurements.
In conclusion, designing, calibrating, and installing custom load pins is a meticulous process that blends advanced engineering with precision craftsmanship.
From the initial consultation and detailed CAD modeling to the careful bonding of strain gauges and rigorous multi-point calibration, each step ensures the load pins meet the highest standards of accuracy and durability.
Proper installation, which includes precise alignment and secure connections, is crucial for achieving reliable force measurements in a variety of industrial applications.
Precision and Reliability in Every Pin: Reach Out to Massload
Ready to take your project to the next level? Massload’s team is here to help.
Contact us today to discuss how we can provide custom load pin solutions tailored to your specific needs. Let’s innovate together and drive efficiency and precision in your operations!