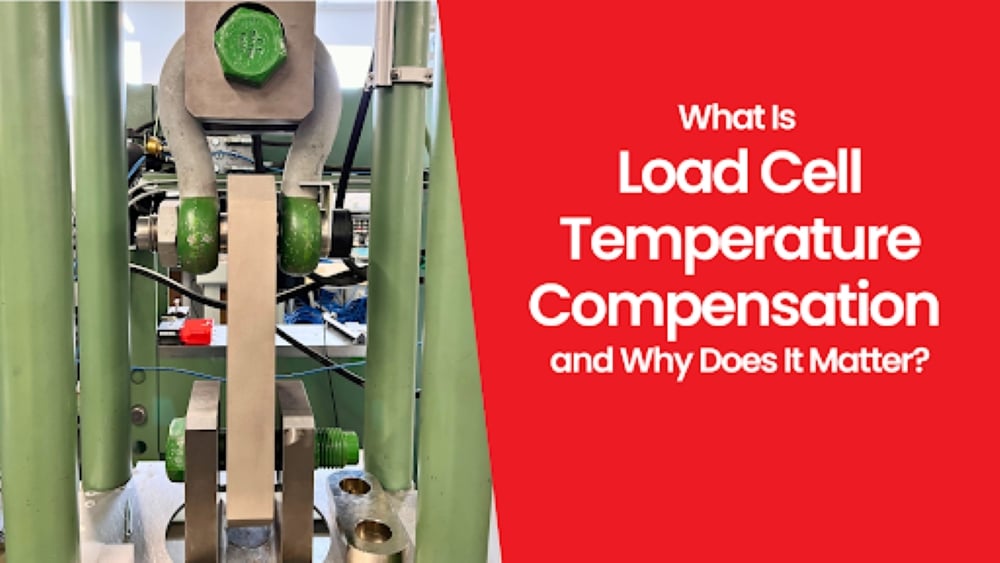
Load cells are precise devices to measure weight or force. But like most materials, the metal inside a load cell expands when it gets hot and contracts when it gets cold. That slight change in size can affect how well the load cell measures weight.
Temperature compensation is a built-in feature that fixes that. Engineers design load cells with special materials and electronic adjustments so temperature changes won’t affect accuracy.
Whether it’s freezing cold or extremely hot, the load cell will keep providing reliable measurements.
Let’s take a closer look at how load cell temperature compensation works and why it’s important for accuracy.
How Does Load Cell Temperature Compensation Actually Work?
Temperature compensation in load cells works through a combination of material selection, strain gauge design, and electronic adjustments. Here’s how:
1. Special Materials
Different metals expand and contract at different rates when exposed to temperature changes. Engineers choose materials for the load cell body that have minimal expansion or predictable behavior. Some load cells use alloys that are more resistant to temperature-related distortions.
2. Compensating with Strain Gauges
Strain gauges are the little sensors inside a load cell that detect deformation (strain) caused by weight. These gauges are designed with materials that counteract temperature effects. For example, if the load cell body expands due to heat, the strain gauges may be designed to compensate for that expansion so the electrical output remains stable.
3. Wheatstone Bridge Circuit Adjustments
Most load cells use a Wheatstone bridge circuit, a system of four strain gauges that work
together. Engineers carefully place these strain gauges so temperature changes affect them in a balanced way, cancelling out errors caused by thermal expansion.
4. Temperature Compensation Resistors
Inside the load cell, tiny temperature-sensitive resistors (also called thermistors) adjust excitation voltage to correct for temperature-related changes. These resistors either increase or decrease electrical resistance depending on the temperature, so the output remains accurate.
5. Electronic Calibration in the Signal Conditioner
Some advanced load cells have digital compensation through microprocessors. These systems monitor temperature and apply software-based corrections in real-time, so you get precise measurements no matter the environmental changes.
Why It Matters
Without temperature compensation, a load cell’s readings could drift up or down as temperatures change, resulting in incorrect weight measurements. By using a combination of mechanical, electrical and digital methods, engineers ensure the load cell stays stable and reliable even in extreme conditions.
Why Temperature Changes Cause Load Cell Drift?
Load cell drift due to temperature refers to gradual, unintended changes in weight readings as temperature changes. As temperature rises or falls, the materials inside the load cell expand or contract, affecting how strain gauges respond to force. This can cause small, continuous shifts in the output even if the actual load remains the same.
Thermal Expansion and Contraction
Load cells are made of metal (e.g. stainless steel or aluminum). Metals expand when heated and contract when cooled, which can slightly change how strain gauges measure force. Even tiny changes can introduce errors over time.
Strain Gauge Sensitivity to Temperature
Strain gauges work by detecting very small deformations in the load cell structure. If temperature affects the strain gauge’s resistance, it can cause false readings—making it seem like the weight is increasing or decreasing when it’s not.
Uneven Temperature Distribution
If different parts of the load cell heat up or cool down at different rates, it can create uneven expansion leading to unpredictable measurement shifts.
Temperature-Induced Electrical Drift
The electronic parts inside a load cell, like resistors and circuits, can be sensitive to temperature changes. As the temperature shifts, their electrical properties can fluctuate slightly, which may cause small changes in the load cell’s readings over time.
How to Reduce Load Cell Temperature Drift
To minimize temperature-related drift, load cells use temperature compensation techniques:
- Matched strain gauges: Strain gauges are placed so temperature effects cancel out, preventing shifts in readings.
- Temperature compensation resistors: These resistors adjust the electrical signal to counteract drift caused by thermal expansion.
- High quality materials: Using metals with low thermal expansion rates reduces unwanted movement.
- Digital compensation: Some modern load cells have built-in sensors that detect temperature changes and apply software-based corrections.
- Let the load cell stabilize when moving from one temperature environment to another.
- Install load cells in temperature controlled areas whenever possible.
- Enclosures or shielding for outdoor or high-temperature applications.
- Calibrate regularly to account for long-term drift.
The Bottom Line
Load cell drifting due to temperature is caused by thermal expansion, strain gauge sensitivity and electrical shifts. While it can’t be eliminated totally, temperature compensation, good materials and proper installation will get you stable and accurate measurements over time.
How to Choose Good Load Cells to Avoid Temperature Drift and Inaccurate Results
When selecting a good quality load cell, especially for environments where temperature fluctuations are a concern, you should consider several key factors. High-quality load cells are designed to minimize drift and ensure accuracy over time. Here’s what to look for:
1. Material Selection
- Best: Stainless steel or high-grade alloy steel.
- Why: They have lower thermal expansion rates, reducing temperature related drift.
- Avoid: Cheap aluminum load cells for high-precision applications, they expand and contract more with temperature changes.
2. Temperature Compensation Features
- Look for load cells with built-in compensation:
- Good load cells have temperature compensation resistors that adjust the signal based on temperature changes.
- Some have active digital compensation using internal temperature sensors and microprocessors.
- Operating temperature range: Ensure the load cell’s compensated temperature range matches your environment.
3. Accuracy Specifications
- Look at Non-Linearity & Hysteresis Errors:
- Non-linearity: The maximum deviation from a straight line
- Hysteresis: If the load cell gives the same reading when the weight is increasing vs decreasing.
- If weight is applied for a long time, does the reading change?
- Look for creep error < 0.03% of full scale over 30 minutes.
4. Type of Strain Gauges & Circuit Design
- Four strain gauge Wheatstone bridge design: Ensures better temperature balance and more stable readings.
- Matched strain gauges: Some load cells use strain gauges that have been temperature-matched to reduce expansion-related drift.
5. Application-Specific Considerations
- For high-precision industrial weighing: Choose load cells with a temperature compensation range suited to your working conditions.
- For outdoor or harsh environments: Look for fully sealed, stainless-steel load cells.
- For dynamic weighing (e.g., conveyor belts, weigh-in-motion): Ensure the load cell can handle rapid temperature changes without signal drift.
Top Takeaways When Choosing a Load Cell
- Choose stainless steel or alloy steel load cells for minimal temperature effects.
- Ensure built-in temperature compensation for stable readings in fluctuating environments.
- Look at accuracy specs (non-linearity, hysteresis, creep error) to ensure precision.
- Buy from trusted manufacturers and check for certified calibration like the Verified Conformity Assessment Program (VCAP) — a certification that Massload proudly upholds.
Following these guidelines, you can select a high-quality load cell that provides consistent, accurate results with minimal temperature drift.
Ensure Accuracy in Any Climate with Massload Load Cells
When it comes to minimizing load cell temperature drift and ensuring long-term accuracy, Massload Technologies offers Canadian-made load cells designed for durability and precision in harsh environments. Our load cells feature:
- Stainless steel construction for minimal thermal expansion
- High accuracy specifications meeting industrial standards
- Custom-engineered solutions for specialized applications
Need reliable load cells for your operation? Contact Massload Technologies today and get expert advice on the best weighing solutions for your industry.