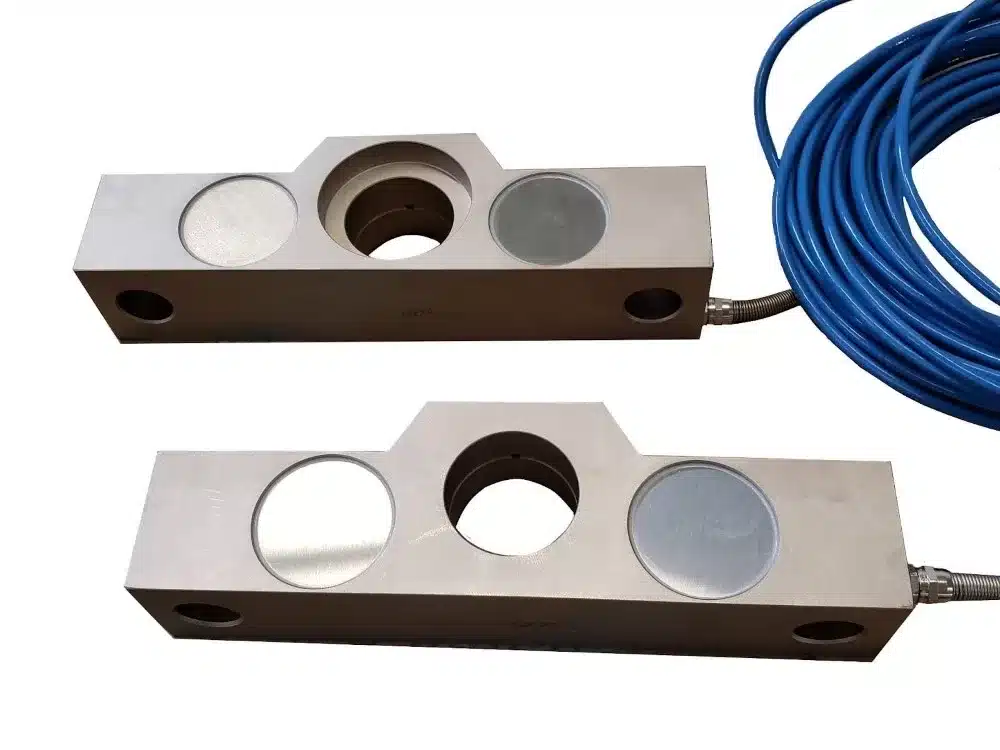
When standard options don’t meet your requirements, custom load cells are the solution. From concept to completion, each stage of custom load cell design is marked by expertise, dedication, and a commitment to excellence.
Join us as we explore the intricacies of custom load cells, from their fundamental principles to the intricate manufacturing processes that bring them to life.
What is a Custom Load Cell Design?
When standard solutions just won’t cut it, when your application demands uniqueness, reliability, and accuracy in every gram measured, it’s time to delve into the world of custom load cells.
So, what exactly is a Custom Load Cell? Imagine a tailored suit crafted by a master tailor, but instead of fabric, we’re talking about precision-engineered components finely tuned to your specific requirements.
These load cells are meticulously designed and manufactured to fit your unique application like a glove, ensuring optimal performance and longevity.
When Are Custom-Designed Load Cells the Best Solutions?
Picture this: you’re navigating the rugged terrain of mining or perhaps delving into the depths of oil & gas exploration. Your operation demands equipment that can withstand harsh conditions while delivering pinpoint accuracy. This is where off-the-shelf solutions falter and custom craftsmanship shines.
Custom design is required when the customer needs a load cell or scale product that does not currently exist and seeks a vendor to design a new product.
Common examples include custom load pins and tension links used in crane modernization projects, underground mining hoists, agricultural machinery, paper mills, and many other applications.
What Is the Mechanical Design of a Load Cell?
At its essence lies a robust framework, typically constructed from durable materials such as steel or aluminum, engineered to withstand the rigors of industrial environments.
Central to the mechanical design are strain gauges, delicate sensors strategically positioned within the load cell’s structure. These gauges are sensitive to even the slightest deformations, allowing them to detect the strain induced by applied forces. As weight is placed upon the load cell, it undergoes subtle changes in shape and dimension, causing the strain gauges to flex accordingly.
This deformation triggers a change in electrical resistance within the strain gauges, which is then measured and converted into a proportional electrical signal. This signal is amplified and processed, accurately representing the applied force or weight.
What Is the Construction and Working of Load Cells?
At its core lies a strain gauge – a marvel of modern engineering capable of detecting the minutest of deformations.
The strain gauge undergoes subtle changes as force is applied, translating mechanical stress into measurable electrical signals.
It’s a delicate dance of resistance and resilience, culminating in precise weight measurement.
How Are Load Cells Made?
Material Selection: It all begins with the selection of high-quality materials. Steel, aluminum, and alloys are carefully chosen for their durability, strength, and resistance to environmental factors.
- Fabrication of Components: The chosen materials are then transformed into the various components that comprise the load cell.
- Integration of Strain Gauges: Strain gauges are central to the construction of a load cell. These delicate sensors are strategically positioned within the load cell’s structure to detect the slightest deformations. Skilled technicians carefully affix the strain gauges to the designated locations, ensuring optimal sensitivity and accuracy.
- Assembly Process: With all components in hand, the assembly process commences. Each part is meticulously integrated into the load cell framework, following exacting specifications and tolerances.
- Calibration and Testing: The load cell undergoes rigorous calibration and testing procedures once assembled.
- Quality Assurance: Throughout the manufacturing process, stringent quality assurance measures are implemented to uphold the highest standards of excellence. Inspections, checks, and audits are conducted at each stage to identify and rectify any deviations or defects, ensuring that only flawless products leave the production line.
Each load cell undergoes a final inspection before being dispatched to customers to confirm compliance with specifications and quality standards.
What Makes a Good Load Cell?
It’s not just about precision engineering or robust construction – it’s about reliability. A good load cell is a stalwart companion, unfaltering in the face of adversity and steadfast in its commitment to accuracy.
It’s a testament to craftsmanship and quality, embodying the ethos of excellence in every gram measured.
What Are Load Cell Specifications?
From capacity to accuracy and sensitivity to operating temperature, these specifications serve as the blueprint for performance.
They’re the yardstick by which load cells are measured, ensuring that each product meets the exacting standards of excellence demanded by the industry.
How Does Massload Design and Manufacture Custom Load Cells?
We specialize in the rapid and quality execution of custom design, engineering, manufacture, and testing of a wide range of custom load cell systems and weigh solutions to meet the needs of our industrial customers.
Our custom design process is about simplifying, clarifying, and multiplying the best solutions. Simply, Clarify, Multiply™ is Massload’s culture translated into a trademark.
This is Our 6 Steps Process:
- Briefing: We start by discussing your weighing application. Typically, our engineers will work with your management and engineers to identify the optimal load cell design.
- Design: We will work on designing the best solution for your project based on the information given in the briefing, our 40+ years of experience in the market, and the latest and most efficient techniques and technologies available.
- Quote: A price estimate is then provided. When you are ready to proceed, we typically request a deposit on the order.
- Approval: Upon receipt of the deposit, we engineer the load cell and provide you with engineered approval drawings for final approval.
- Production: When drawings are approved, detailed engineering and manufacturing commences. Lead time is subject to material availability and production loading but is typically quite fast.
After That, the Sixth and Final Step is Making the Solution Real. This is Our Manufacturing Process:
- Mill Certified materials procurement
- CNC machining
- ISO 9000 heat treating and sandblasting
- Strain gauge bonding, wiring, and cabling
- Linearity testing, trimming, and calibration to NIST traceable standards
- Sealing and final testing
- Packaging and shipping
Extra: Ultrasound material testing, proof load testing, and magnetic particle testing may also be performed as required.
We have a long history of custom design clients that keep coming back to us year after year.
In a Recent Conversation With Thom Hewitt, a Massload Client For Over Two Decades, Here’s What He Had to Say About Our Load Cells:
“The particular load cell we get from Massload, we’re extraordinarily happy with because it does everything we want it to do. It performs very well in the field for the customers. We are very happy with the product and the service they provide. Completely satisfied with the load cells and the service.”
Massload is the partner you can trust to develop and manufacture to the exacting standards required to meet your customers’ expectations.
If you want to build a custom solution for your project with a company you can always rely on, let’s talk!
Massload’s Custom-Designed Load Cells for Weigh Industrial Equipment
Our in-house engineering and product specialists are available to custom design a load cell or industrial weighing scale to your unique requirements, and Massload’s dedicated after-sales customer support and service personnel are here to ensure your industrial weighing solution will continue to perform year after year.
Tell us the demands of your project, and we will help you figure out the best solution.