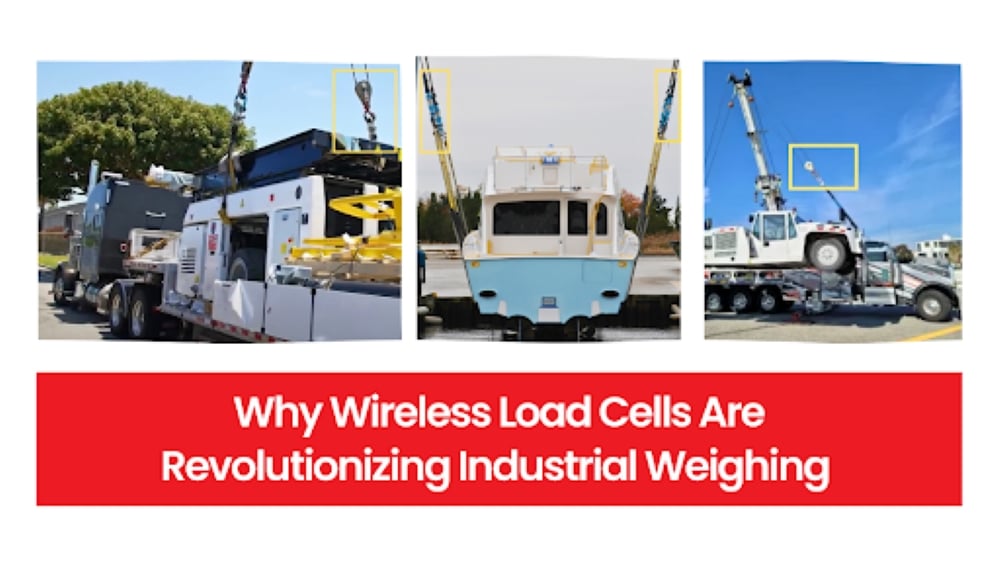
A wireless load cell is a sensor that measures weight or force and transmits the data without cables. It operates using radio frequency (RF) signals, including ISM 2.4GHz, Bluetooth, or Wi-Fi.
This is especially handy in situations where running cables is difficult or unsafe, like on large industrial sites, with moving equipment, or in outdoor settings. While they work much like traditional load cells by converting force into an electrical signal, wireless load cells have a built-in transmitter that sends the data to a receiver or monitoring system.
Even though they’re wireless, they still need a power source, which is typically a battery or an energy-harvesting system, depending on the design.
What Devices Can Connect to a Wireless Load cell?
A wireless load cell can connect to many types of devices depending on the communication protocol it uses (e.g. Bluetooth, Wi-Fi or RF). Here are the most common devices that can receive and process data from a wireless load cell:
1. Handheld Indicators & Displays
- Portable digital readouts that show weight or force in real time.
- Great for field use where mobility is required.
- Used in crane weighing, material handling and vehicle weighing.
2. Industrial Controllers & PLCs (Programmable Logic Controllers)
- Wireless load cells can send data to PLCs used in automated systems.
- Used in manufacturing, automation and quality control applications.
- Can integrate with SCADA systems for industrial monitoring.
3. Computers & Laptops
- Wireless load cells can send data to PC software for analysis and logging.
- Used in testing environments, research labs and manufacturing.
- Supports real-time graphing, statistical analysis and custom reports.
4. Smartphones & Tablets
- Many modern wireless load cells operate on 2.4GHz, Bluetooth, or Wi-Fi and can connect to a mobile app. Massload’s wireless load cells use the T24 system, which runs on 2.4GHz for reliable data transmission.
- Useful for portable applications, remote monitoring and field measurements.
- Allows data logging and sharing without extra equipment.
5. Cloud-Based Systems & IoT Platforms
- Data can be sent to cloud-based storage and IoT dashboards for remote access. Used in industries that require real-time global monitoring, like oil & gas, logistics and remote asset tracking.
- Can integrate with AI-driven analytics for predictive maintenance.
6. Industrial Wireless Receivers
- Dedicated RF receivers can pick up signals from wireless load cells and convert them into a standard output (e.g. analog, digital or serial).
- Used in factory automation, crane safety systems and remote weighing operations.
7. Digital Weighing Indicators with Wireless Modules
- Some weighing indicators support wireless input to display data from multiple load cells.
- Common in multi-point weighing applications like truck scales, hoppers and silos.
8. Data Loggers & Measurement Systems
- Wireless load cells can send data to logging devices that store weight readings over time.
- Used for long-term monitoring in industries like agriculture, construction and aerospace testing.
Single-Point vs. Multi-Point Wireless Load Cell Systems
With wireless load cells, you can choose between a single-point or multi-point setup, depending on your needs and how many load cells are part of your system. Massload Technologies’ T24 wireless system makes it easy to use either option.
1. Single-Point Wireless Load Cell System
A single-point system consists of one wireless load cell transmitting data to one or multiple receivers or displays. Typical applications include:
- Crane and Hoist Weighing: One wireless tension load cell measuring the weight of a lifted object.
- Material Testing: A single load cell used in a force measurement application.
- Portable Vehicle Weighing: A single wireless axle scale pad measuring one wheel load at a time.
2. Multi-Point Wireless Load Cell System
A multi-point system uses multiple wireless load cells that send data to a single display, receiver or software system. This allows for real-time load distribution monitoring. Typical applications include:
- Tank and Hopper Weighing: Multiple load cells under a tank sending data to one indicator.
- Crane and Rigging: Several wireless load shackles monitoring the forces on different rigging points.
- Vehicle Weighing: Multiple wireless axle scales summing the total truck weight.
- Structural Monitoring: Multiple sensors measuring stress and strain in large structures (e.g., bridges)
Key Differences Between Single-Point and Multi-Point Wireless Systems
Feature | Single-Point System | Multi-Point System |
Number of Load Cells | 1 | Multiple |
Setup Complexity | Simple | More advanced |
Data Display | Reads one load cell at a time | Summarizes multiple load cells |
Best For | Portable use, simple weighing tasks | Complex load distribution, large structures, multipoint lifting |
When Should I Use a Wireless Load Cell?
Whether you should use a wireless load cell depends on your application, environment, and operational needs. Here are some key factors to consider:
When a Wireless Load Cell is a Good Choice | When a Wired Load Cell Might Be Better |
✅Hard-to-Reach Locations
✅ Moving Equipment
✅ Safety Concerns
✅ Portability Needs
✅ Remote Monitoring Requirements
|
❌ If Continuous Power Supply is Required
❌ If the Environment Has High Wireless Interference
❌ If Cost is a Primary Concern
❌ If High-Speed, High-Precision Data is Needed
|
If you need flexibility, ease of installation and remote access, wireless load cells are the way to go. But if you prioritize continuous operation, precision and cost effectiveness, a wired system might be better.
Why Wireless Load Cells Are Revolutionizing Industrial Weighing
Industrial weighing systems have always used wired load cells, with extensive cabling, complex installations and frequent maintenance. But with the adoption of wireless load cells, industrial weighing is getting a whole new level of efficiency, flexibility and reliability. Here’s why wireless is transforming industrial weighing:
1. No Cables: More Flexibility, Less Downtime
Wired systems rely on long cables to transmit data which can be prone to damage, wear and environmental hazards. Wireless load cells remove these limitations by transmitting weight data wirelessly, so you get:
- Faster setup: No need to run or protect cables across long distances.
- Less downtime: No cable related failures or costly maintenance.
- Easier installation: Ideal for mobile applications or hard to reach locations.
Construction, mining and aerospace industries benefit from the ability to deploy wireless weighing solutions in rugged and remote environments.
2. Increased Safety in Hazardous Environments
Industrial environments like oil & gas, chemical processing and offshore drilling are hazardous where wired connections are impractical or unsafe. Wireless load cells make it safer by:
- Reducing the need for workers to access hazardous areas to check weight readings.
- Eliminating cable related trip hazards and electrical interference.
- Providing real-time alerts to prevent accidents due to excessive loads or equipment failure.
3. Portability and Versatility
Unlike wired systems which require fixed installations, wireless load cells are portable, so they’re perfect for:
- Temporary weighing applications, such as on-site vehicle weighing or field testing.
- Dynamic force measurement, such as load monitoring on moving conveyor belts or industrial robots.
- Rotating and moving equipment, where wired systems would be impractical.
Example: Portable axle scales use wireless load cells to measure truck loads quickly at temporary checkpoints without the need for fixed infrastructure.
4. Cost Savings Over Time
While wireless load cells have a higher initial cost, they’ll save you in the long run by:
- Reducing installation costs: No expensive wiring or infrastructure needed.
- Less maintenance: No cables to replace or repair.
- Fewer manual steps: No need to visit each weight indicator.
Industries like manufacturing, logistics and bulk material handling see big operational cost savings by switching to wireless weighing solutions.
5. Precision and Reliability
Early wireless systems had issues with signal interference and accuracy. But modern wireless load cells, like those using T24 wireless telemetry, have advanced features like:
- Encrypted, interference-free communication for secure and stable data transfer.
- Long range transmission (up to 800 meters) in open air.
- Battery powered with long life (up to 5 years standby) to ensure continuous operation.
This means industrial grade accuracy even in harsh environments.
Wireless load cells are transforming industrial weighing. They eliminate cables, provide real-time monitoring, improve safety, and reduce costs. The result is a simpler, safer, and more efficient way to work.
As IoT, automation and AI driven analytics evolve, wireless weighing solutions will play a key role in smarter, safer and more efficient industrial operations.
Massload Wireless Load Cell Systems
Massload integrates the T24 wireless telemetry system to turn traditional load cells into wireless devices, reducing the need for cumbersome cabling. Here’s how they do it:
1. Wireless Load Cell Transmitters
Massload uses T24 transmitters, like the WL-T24-ACM, to transmit data from load cells wirelessly. Features include:
- Wireless Transmission: 2.4 GHz frequency, 800 meters (2,600 feet) open air.
- Power Options: Two “D” size replaceable batteries, up to 5 years battery life or external power.
- Durability: IP67 rated enclosure, dust and water ingress protection.
These transmitters can be connected to various load cells, tension links and load shackles, turning them into wireless measurement devices.
2. Wireless Indicators and Receivers
To receive and display data from the wireless load cells, Massload offers:* Handheld Indicators: The WL-T24-HA is a multi-channel handheld indicator that can receive data from up to 12 transmitters. Features:
- Summing Capability: Displays total load from multiple inputs.
- Long Range Reception: 800 meters (2,600 feet) open air.
- Portability: Two AA batteries, up to 40 hours continuous use, IP67 rated.
- USB Wireless Receivers: The WL-T24-BSu connects to a PC via USB, data logging and analysis through software interfaces.
- Analog Output Modules: The WL-T24-AO1 converts wireless data to analog signals (e.g. 4-20 mA) for PLCs and other industrial control systems.
3. Complete Wireless Solutions
By combining T24 transmitters with compatible receivers and indicators, Massload offers complete wireless load monitoring systems for various industrial applications:
- Crane and Hoist Monitoring: Wireless load shackles send real-time load data to handheld indicators, improving safety and efficiency.
- Vehicle Weighing: Wireless axle pad scales send weight data to portable indicators or PCs for vehicle load management.
This wireless integration simplifies installation, reduces maintenance vs wired systems and offers flexible data monitoring solutions across different industrial environments.
Massload Wireless Crane Scale
The Massload Wireless Load Shackle is a high accuracy weighing system for lifting and hoisting applications. It uses wireless load cells (typically tension links or wireless load shackles) to measure loads in real time and send data to a handheld indicator or computer.
How It Works:
Load Measurement:
- A wireless load cell (tension link or shackle) is attached between the crane hook and the load.
- The sensor measures the force applied to it, converts it to weight.
Wireless Data Transmission:
- The T24 wireless transmitter inside the load cell sends weight data using a 2.4 GHz radio signal.
- Data can be transmitted up to 800 meters (2,600 feet) in open air. * Data is received by a T24-HA handheld indicator, T24-BSu PC-based receiver or an industrial PLC system.
- Operators can see the load in real time and prevent overloading.
Long Battery Life & Rugged:
- Wireless system is battery-powered, up to 5 years standby life.
- IP67 rated, withstands harsh industrial environment.
Massload Wireless Tension Link
The Massload Wireless Tension Link is a high accuracy load measurement device for lifting, hoisting and tension monitoring applications. It measures the force between two attachment points and sends data wirelessly.
How It Works:
Load Measurement:
- The tension link is installed between a crane hook and the load or between two anchor points.
- When force is applied, the strain gauges inside the load cell detect the tension and convert it into an electrical signal.
Wireless Data Transmission:
- The T24 wireless transmitter inside the tension link converts the signal into a digital value.
- The weight data is then sent via 2.4 GHz radio frequency to a receiver.
Real-Time:
- Data can be seen on a T24-HA handheld indicator, T24-BSu PC-based receiver or an industrial control system (PLC).
- Operators can see real-time tension readings from up to 800 meters (2,600 feet) away.
Battery & Durability:
- Tension link is battery-powered, up to 5 years standby life.
- IP67 rated, suitable for harsh industrial and outdoor environments.
Precision Without the Tangle: Try Wireless Today
Ready to experience the benefits of wireless load cells in your industrial operations? Whether you need improved safety, real-time monitoring, or seamless data integration, Massload’s wireless weighing solutions offer the flexibility and reliability you need.